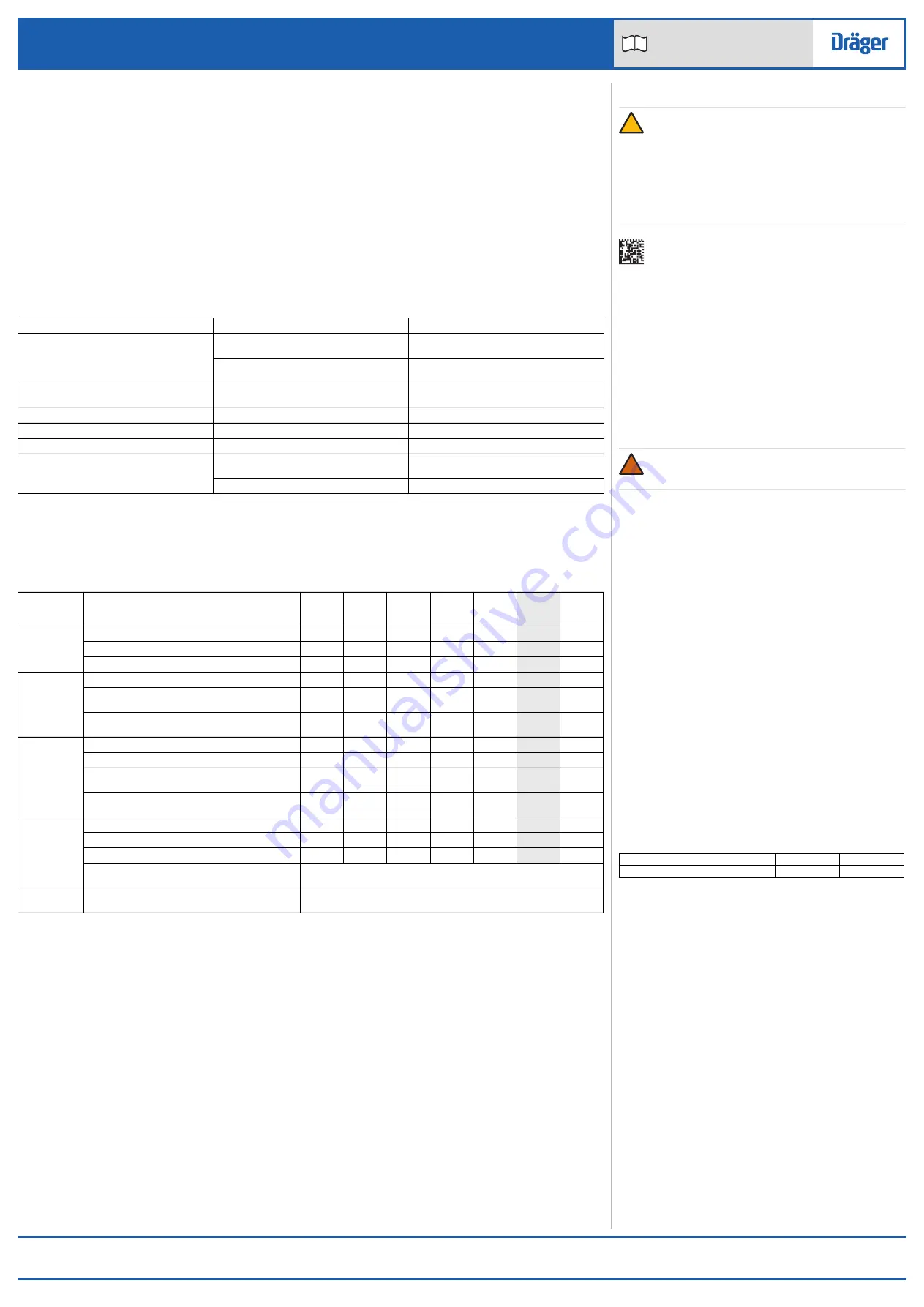
PAS
®
Lite Series
Self contained breathing apparatus
Instructions for Use
i
Dow Corning
®
and Molykote
®
are registered trademarks of Dow Corning Corporation
3357781 (A3-D-P) Page 2 of 2
3357781
© Dräger Safety UK Limited
Edition 06 – July 2018 (Edition 01 – December 2009)
Subject to alteration
Draeger Safety UK Limited
Ullswater Close
Tel +44 1670 352 891
Blyth, NE24 4RG
Fax +44 1670 356 266
United Kingdom
www.draeger.com
Leak test and whistle warning test
1. Press the reset button when using a positive-pressure lung demand valve.
2. Slowly and fully open the cylinder valve (anticlockwise). During pressurization a momentary sounding of the whistle will occur.
3. Fully close the cylinder valve.
4. After one minute, check the contents gauge and then reopen the cylinder valve. The gauge must not show an increase in pressure of more than 10 bar
(one radial marking on the gauge face). Investigate and repair a failed leak test (see Section 4), and then repeat the leak test.
5. Fully close the cylinder valve.
6. Observe the contents gauge and slowly release the pressure as follows:
a. Positive-pressure lung demand valves – Cover the outlet port of the valve with the palm of the hand. Press the rubber cover to switch on the
positive pressure. Vent the system by carefully lifting the palm of the hand from the outlet port to maintain a slow pressure decrease.
b. Negative-pressure lung demand valves – Slowly vent the system by carefully pressing the rubber cover.
7. The whistle must begin to sound in the range 60 bar to 50 bar.
8. Continue to vent the system until fully exhausted.
9. Press the reset button when using a positive-pressure lung demand valve.
4
Troubleshooting
The troubleshooting guide shows fault diagnosis and repair information applicable to breathing apparatus users. Further troubleshooting and repair
information is available in Instructions for Use supplied with associated equipment.
Where the troubleshooting guide shows more than one fault or remedy, carry out repair actions in the order that they appear in the table.
Contact service personnel or Dräger when the remedy information indicates a service task, or if the symptom remains after all remedy actions have been
attempted.
5
Maintenance
5.1
Maintenance table
Service and test the breathing apparatus, including out-of-use apparatus, in accordance with the maintenance table. Record all service details and
testing. Refer also to the Instructions for Use for the lung demand valve, face mask and other associated equipment.
Additional inspection and testing may be required in the country of use to ensure compliance with national regulations.
Symptom
Fault
Remedy
High-pressure air leak or failed leak test
Loose or dirty connector
Disconnect, clean and reconnect couplings and
retest
Faulty hose or component
Substitute user replaceable accessories and
retest
Air leak from medium-pressure hose connection
at the pressure reducer (safety relief valve)
Faulty O-ring, retainer, spring or pressure
reducer
Service task
High or low medium pressure
Pressure reducer fault
Service task
Poor sounding whistle
Whistle dirty
Clean whistle flute and retest
Whistle not functioning correctly
Activation mechanism fault
Service task
Difficulty connecting or disconnecting the
medium-pressure quick coupling
Dirty connector
Disconnect, clean and reconnect couplings and
retest
Burring of the male coupling
Replace the hose with the male coupling
Component/
System
Task
Before
use
After
use
Every
month
Every
3
months
Every
year
Every
6
years
Every
10
years
Complete
apparatus
Visual inspection (see Note 1 Section 3.5.1)
Notes
O Dräger recommendations
1
Clean the equipment if it is dirty. If it the equipment has been exposed to contaminants, disinfect any components that come into direct and prolonged
contact with the skin.
O
O
O
Functional testing (see Section 3.5.3)
O
O
O
Breathing cycle and static tests (see Note 2)
2
These maintenance tasks may only be carried out by Dräger or trained service personnel. Details of the tests are contained in the Technical Manual
which is issued to service personnel that have attended a relevant Dräger maintenance course.
O
Lung demand
valve
Check push-in type connectors for lubricant
(Note 3)
3
For type A check the O-ring on the lung demand valve; and for type ESA check the outer surface of the male part of the push-in connector on the
lung demand valve. As a guide, lubricant should be felt on the fingers but not seen. If relubrication is required, lightly apply Dow Corning
®
Molykote
®
111 (other lubricants are not tested and may damage the equipment).
O
Check the male element of the quick coupling for
burring (see Step 3 in Section 3.1)
O
Overhaul. Contact Dräger for the Repair Exchange
(REX) service (see Note 4)
4
Overhaul every 6 years is applied to equipment users subject to German regulations only. Users in Germany must meet the requirements of: German
fire brigade regulations (FwDV 7 and vfdb – RL0804), and German national regulations (BGR 190 or GUV R190 and GUV-I-8674).
O
Pressure
reducer
Medium-pressure check (see Note 2)
O
Inspect the sintered filter (see Note 2 and Note 5)
5
Replace the sintered filter if a drop in reducer performance is observed during a flow check or if it is visibly damaged.
O
Inspect the high-pressure connector O-ring (see
6
Replace the high-pressure connector O-ring if it is found to leak during functional testing or if the O-ring is visibly damaged.
O
Overhaul. Contact Dräger for the Repair Exchange
(REX) service (see Note 7)
7
Where the breathing apparatus is subjected to a high level of use (in training establishments etc.), reduce the overhaul period for the pressure
reducer. In these circumstances, Dräger recommend that the overhaul fre-quency should be less than 5,000 applications of use. An application of
use is defined as a single use of the fully assembled breathing apparatus, where the user breathes from the air cylinder. It does not include system
pressurization for pre-operational checks.
O
O
Cylinder
Charge cylinder to correct working pressure
O
O
Check charged pressure (stored cylinders only)
O
Check test date of cylinder
O
Recertification according to national regulations in the
country of use
According to national regulations in the country of use
Cylinder valve
Overhaul when necessary or at time of cylinder
recertification
At the time of cylinder recertification
5.2
Cleaning and disinfecting
CAUTION
Do not exceed 60 °C for drying, and remove components from the
drying facility immediately when dry. Drying time in a heated dryer
must not exceed 30 minutes.
Do not immerse pneumatic or electronic components in cleaning
solutions or water.
If water is trapped and then freezes inside the pneumatic system of
the breathing apparatus (such as the lung demand valve), operation
will be impaired. Prevent any liquid from entering, and thoroughly dry
the breathing apparatus after cleaning to prevent this from occurring.
For information about suitable cleaning and disinfecting agents
and their specifications refer to document 9100081 on
www.draeger.com/IFU.
Refer also to the Instructions for Use for the lung demand valve, face mask
and other associated equipment.
●
Use only clean lint-free cloths
1. Clean the breathing apparatus manually using a cloth moistened with
cleaning solution to remove excess dirt.
2. Apply disinfecting solution to all internal and external surfaces.
3. Rinse all components thoroughly with clean water to remove all
cleaning and disinfecting agents.
4. Dry all components using a dry cloth, in a heated dryer or in air.
5. Contact service personnel or Dräger if disassembly of the harness,
space frame or pneumatic components is required.
5.3
Maintenance work
5.3.1
Air cylinder charging
WARNING
The air supply shall meet the requirements for breathable air
according to EN12021.
Refer to the instructions supplied with the cylinder and the charging
apparatus for recharging a compressed air cylinder.
6
Storage
6.1
Storage preparation
●
Extend the shoulder straps, waist belt and the straps of the face mask.
●
For storage, place the face mask in a protective bag (contact Dräger
for supply of a suitable bag).
●
Route rubber hoses in such a way that the bend radius is not too acute
and the hose is not stretched, compressed or twisted.
6.2
Storage conditions
●
Store the equipment between -15 °C and +25 °C. Ensure that the
environment is dry, free from dust and dirt, and does not subject the
equipment to wear or damage due to abrasion. Do not store the
equipment in direct sunlight.
●
Fix the breathing apparatus securely to any raised mounting point to
prevent it from falling.
7
Technical data
High-pressure connection
Standard G5/8” as per EN 144-2
(200 bar or 300 bar)
Other connections are available to
national regulations
Compressed air cylinders
4 litre to 9 litre (200 bar or 300 bar), steel
or composite materials
Whistle warning
Initial activation: 60 bar to 50 bar
Medium pressure
6 bar to 9 bar
Operating temperature
EN137 temperature range
8
Order list
Description
Quantity
Order code
Dow Corning
®
Molykote
®
111
100 grams
3331247
!
!