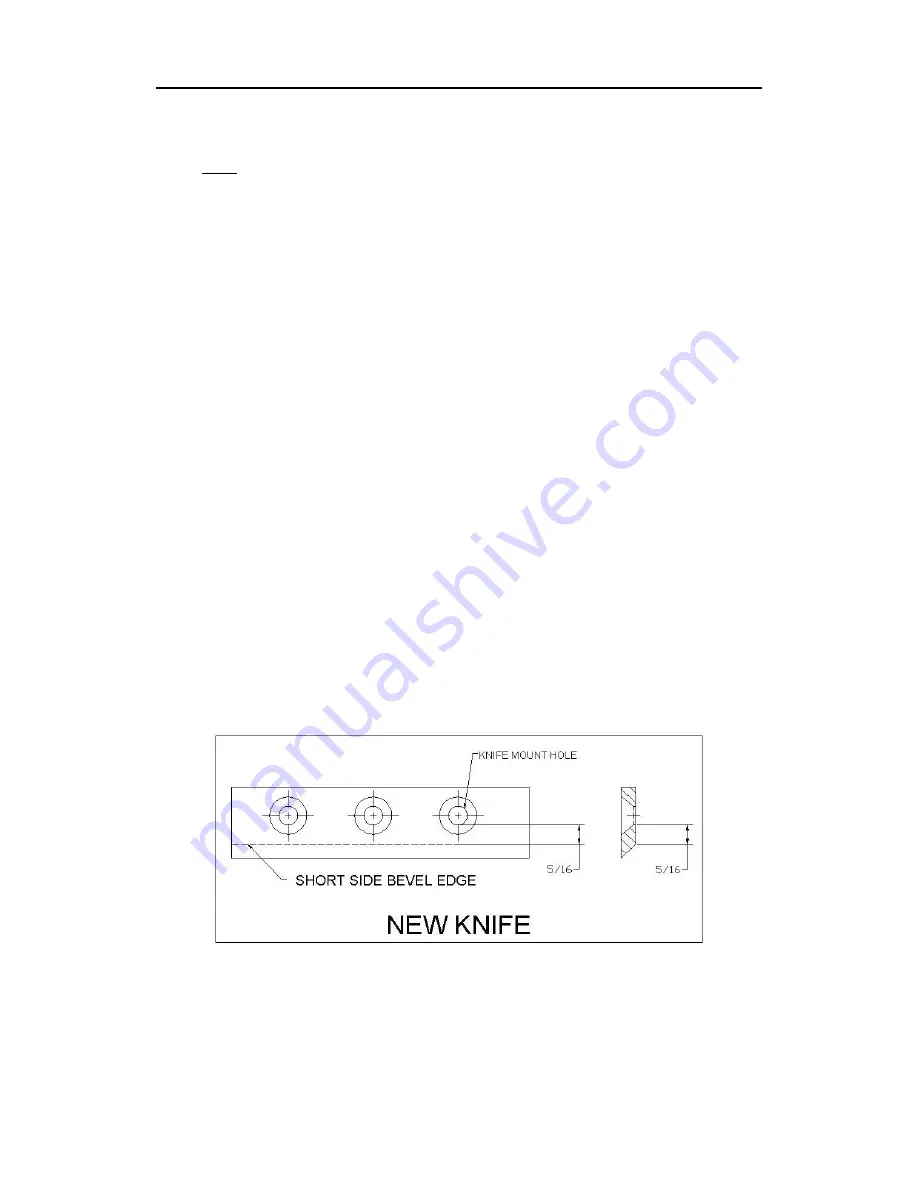
REMOVAL, SHARPENING AND RE-INSTALLATION OF CHIPPER KNIFE
HOW TO REMOVE THE KNIFE
•
Stop the engine.
•
Remove both spark plug wires and keep away from spark plugs.
•
Disconnect battery at negative terminal.
•
Remove both access covers from the chipper basic machine.
•
Rotate the chipper disk until the three countersunk screws and nylock nuts attaching the
knife to the flywheel are visible through the access doors.
•
Clean out the heads of the allen screws with an awl or sharp tool.
•
Insert a 3/16” allen wrench into the heads of the screws.
•
Use a ½” socket and ratchet to remove the nylock nuts from the screws.
•
Remove all three allen screws and nuts in this manner.
KNIFE SHARPENING
•
You should never attempt to sharpen the chipper knife (or knives) freehand.
•
It is extremely important that the 45 degree angle be maintained consistently for proper
performance.
•
The chipper knife should be taken to a machine shop for proper sharpening.
•
Excessive heat generated during the sharpening process will damage knives and weaken
the metal.
Be sure the knife is not overheated.
KNIFE INFORMATION
•
The chipper knife should be checked routinely for sharpness.
•
Using a dull knife will decrease performance and cause excessive vibration that will
cause damage to the chipper.
•
How many times a knife can be sharpened is determined by how much material needs to
be taken off to sharpen or to compensate for dents or gouges.
•
A new chipper knife has 5/16” measurement between the short side bevel edge and the
knife mounting holes. See figure 2.
Figure 2
22
Summary of Contents for TLC18-CHP
Page 4: ...091 0057 091 0059 091 0062 091 0088 091 0093 4...
Page 5: ...091 0256 091 0378 091 0379 091 0380 091 0381 5...
Page 6: ...091 0384 913 0265 6...
Page 31: ...31...
Page 32: ...32...
Page 34: ...34...
Page 35: ...NOTES 35...