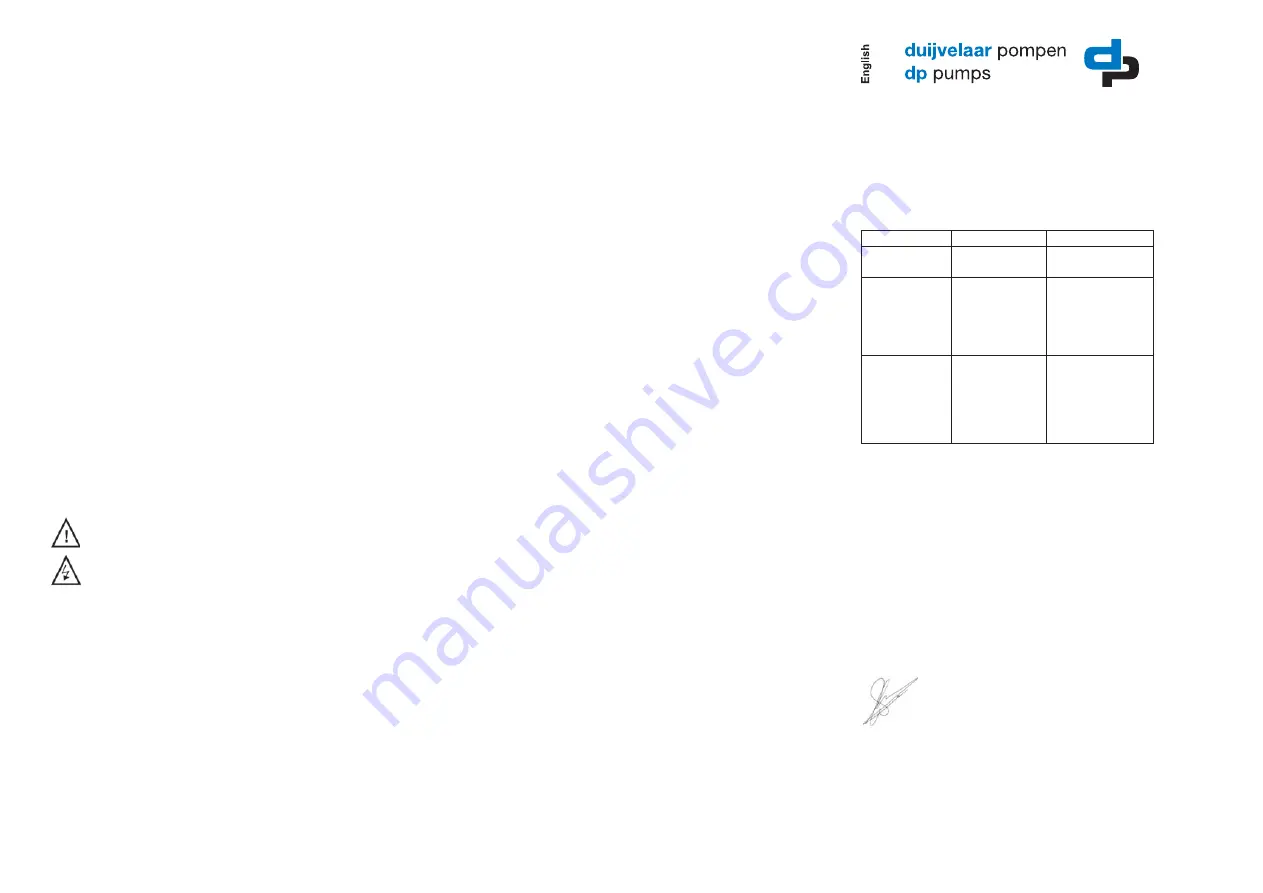
This installation guide gives basic instructions which are to be observed during
installation, operation and maintenance of the pump. It is therefore imperative that
this manual be read by the responsible person/operator prior to the installation and
should always be kept available at the site. It is not only the general safety
instructions under this main heading “Safety” that are to be observed but also the
specific information provided under the other main headings.
Serial No.: See nameplate
Application
DHC Pumps are available with automatic regulation (DHC-A) and with manual
regulation (DHC-M). The DHC-BM series is suitable for tap water and the DHC-CM
series for hot/cold water applications.
Pump medium:
Clean, thin, non-aggressive and non-explosive fluids without any solids or fibres.
Antifreeze products without mineral oil (special model upon request).
Please note:
If any liquid other than water is being pumped, we recommend that
you contact DP-Pumps or their representatives as the pump characteristics may
change.
Technical Data
Electrical data
See nameplate
Max. working pressure 10 bar
Min. static head at 82°C
2-3m (dependent upon model)
Min. static head at 95°C 4-6m (dependent upon model)
Medium temperature (C)
- 15°C to + 120°C
Medium temperature (B)
- 15°C to + 65°C
* except DHC25-30/40 and single phase pumps DHC40-90 and above, max.
medium temperature 100°C
Safety
- The surface temperature of the pump might be hot!
- When venting the pump
(Fig. 5)
, it could result in a slight escape of
hot water or steam!
- Pump should be wired in line with the existing regulations.
- The electrical supply to the pump is to be switched off before
adjusting the speed plug.
Installation
1) The pump should always be installed with the pump shaft horizontal
(Fig. 1).
Direction of flow through the pump casing is indicated by an arrow.
2) Ensure pipe work alignment is correct and the pump and pipe work are adequately
supported. Sharp bends should be avoided adjacent to the pump.
3) If pump is mounted in vertical pipe work, flow should be upwards. If flow is downwards,
an air-vent must be fitted at the highest point before pump suction. This applies
specially with tap water applications, which should be vented regularly.
4) Pumps should never be allowed to operate for a long period in a closed valve condition.
5) Pumps should never be installed with terminal box facing downwards. If terminal box
is repositioned by rotating head, care must be taken to ensure the casing O-ring is
correctly positioned.
6) To avoid accumulation of impurities in the pump, ensure that it is not mounted at the l
owest point in a system.
7) It is recommended that isolating valves are fitted on either side of the pump.
8) System should be thoroughly flushed out to clear any solder, steel wool, plaster or any
other foreign matter that may be lodged in the pump.
Electrical Connection
A wiring diagram is located under the terminal box cover lid
(Fig. 2)
. PG standard
compression glands are fitted to allow cable entry to the terminal box. The larger pumps
need overload protection. When wired through a 132 Starter, overload protection is
automatically achieved, immaterial of speed selected, using terminals “a” and “b”,
fitted in the terminal box.
Note:
If standard motor starter is used, the overload should be
adjusted in accordance with the full load current shown on the pump nameplate.
Overload must be readjusted when speed is changed.
After wiring, direction of rotation should be checked by removing plug in the centre of the
nameplate
(Fig. 5)
which will reveal the motor shaft. If incorrect, exchange any two supply
leads, on 3-phase pumps. On single-phase pumps check that units are wired strictly in
accordance with
(Fig. 2)
. If the system is not filled with water, pump should only be run
for a short period to prevent damage to pump bearings which are lubricated by system
water.
Venting
Once the system has been filled and pressurised, if required, and before starting up, the
pump must be vented by removing the plug positioned in the centre of the nameplate
(Fig. 5)
. After venting the vent plug must be tightened before starting the pump. This
process should be repeated periodically, until all air held in suspension in the system,
has been removed. On single-case twin pumps mounted in horizontal pipe work, it is
possible to fit an automatic air vent to the top part of the pump easing.
Speed Selection
All pump motors fitted with electrical regulators, are wound suitable for 3- or 4-speed
operation
(Fig. 3a, 3b, 3c).
The regulator must only be operated when the motor is
isolated. All pumps are supplied with speed plugs set at maximum performance. Speed
plug should always be readjusted to minimum speed, compatible with efficient operation
of the system. This will ensure minimum velocity noise and minimum power consumption.
Manually regulated pumps should also be readjusted
(Fig. 4)
.
Service/Maintenance
DP’s DHC circulator range of glandless pumps are maintenance free and in a well
designed system, should give many years of service. If motor shaft is seized as a
result of pump standing for a long period without use, or by the accumulation of
magnetite or other impurities, it should be freed. Insert a screwdriver through vent
hole into the slot in the end of the shaft and rotate
(Fig. 5)
. Pump can also be
stripped down and cleaned, system drained, flushed out and refilled.
Failure table
Fault
Cause
Action
Pump running
Air in system.
b
XWQRÀ
ow
Pump will
Power supply
failure. Loose
electrical
connections.
Seized shaft
Check starter and
fuses. Remake
connections.
See above
Service/Maintenance.
not start
Pump noisy
Incorrect rotation.
Check rotation and
correct.
Reduce speed
regulator setting.
Increase inlet pressure.
Vent pump and
system
Pump speed
too high.
Static head too
low.
Air in the system.
.
Vent pump
and system
Declaration of Conformity
We, DP-Pumps, hereby declare that our glandless circulators type DHC-M are in
conformity with:
- Directive 2006/95/EC on the harmonisation of the laws of Member States relating
to electrical equipment designed for use within certainvoltage limits.
- Directive 2004/108/EC on the harmonisation of the laws of the Member States
relating to electromagnetic compatibility.
- Directive 2006/42/EC on the harmonisation of the laws of the Member States
relating to construction and making of machines.
If further information is required, please contact DP-Pumps or their representatives.
Used EN standards: EN 60335-1, EN 60335-2-51, EN 61000-6-4,
EN 61000-6-2:2002 and EN 809, EN 16297-1: 2012, EN 16297-2: 2012
BE00000512-A / version 11/2012
Wil Ouwehand
Technical Director
Per
VRQQHOTXDOL¿FDWLRQW
raining
Personnel responsible for installation, operation, maintenance and inspection of
the pump must be in possession of the necessary qualifications for this kind of
work. Furthermore the owner should assure that the contents of the operation
manual is understood by his personnel.
Airborne sound pressure level (distance 1 m)
DHC15-40 to DHC40-80, max 43 dB(A)
DHC40-90 to DHC80-110, max 55 dB(A)
Installation and operating manual
Glandless circulators
Series: DHC -M
2
Summary of Contents for DHC -M Series
Page 3: ...3 ...