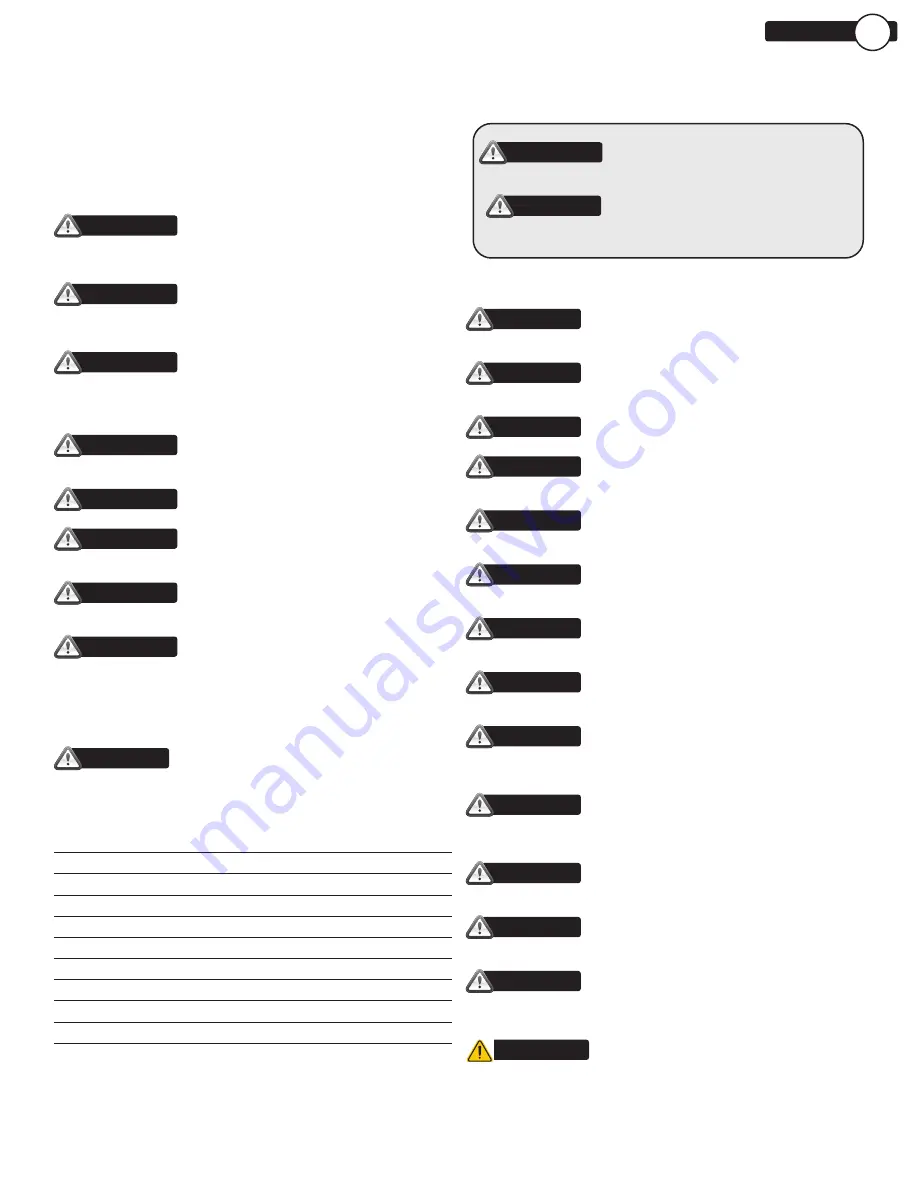
ALF-13080-E-01
All-Flo
3
SECTION
1
READ THESE WARNINGS AND SAFETY PRECAUTIONS PRIOR TO
INSTALLATION OR OPERATION. FAILURE TO COMPLY WITH THESE
INSTRUCTIONS COULD RESULT IN PERSONAL INJURY AND OR
PROPERTY DAMAGE. RETAIN THESE INSTRUCTIONS FOR FUTURE
REFERENCE.
WARNING
Pump, valves and all containers must be properly
grounded prior to handling flammable fluids and/or whenever static
electricity is a hazard.
WARNING
Prior to servicing the pump, ensure that the air and
fluid lines are closed and disconnected. While wearing personal protective
equipment, flush, drain and process liquid from the pump in a safe manner.
WARNING
For pump models with non-metallic manifolds,
air valves, or chambers: When the relative humidity in the surrounding
atmosphere is above 30%, the equipment must not be touched by
personnel unless first wiped down with a damp cloth.
WARNING
Maintenance must not be performed when a
hazardous atmosphere is present.
WARNING
Use only with liquid process fluid.
WARNING
This equipment’s ambient temperature range is
32
°
F (0
°
C) to 104
°
F (40
°
C)
WARNING
Do not operate the pump with fluids or in
temperatures which are less than 32
°
F (0
°
C)
WARNING
The T6-T3 marking refers to the maximum
surface temperature depending not on the equipment itself, but mainly
on operating conditions. In this case, the maximum surface temperature
depends upon the temperature of the process fluids. Do not exceed the
maximum recommended process fluid temperature of the configured
materials.
CAUTION
The temperature of the process fluid and
air input must be no more than 36°F (20°C) less of the maximum
temperature allowed for the appropriate non-metallic material. See the
list of temperatures below for each material’s maximum recommended
temperature and applicable ATEX temperature class:
Buna-N (Nitrile):
10°F to 180°F (-12°C to 82°C)
T6
Geolast
®
:
10°F to 180°F (-12°C to 82°C)
T6
EPDM:
-40°F to 280°F (-40°C to 138°C)
T4
Santoprene
®
:
-40°F to 225°F (-40°C to 107°C)
T5
FKM:
-40°F to 350°F (-40°C to 177°C)
T3
PTFE:
40°F to 220°F (4°C to 104°C)
T6
Polyethylene:
32°F to 158°F (0°C to 70°C)
T6
Polypropylene:
32°F to 180°F (0°C to 82°C)
T6
PVDF:
0°F to 250°F (-18°C to 121°C)
T4
Nylon:
0°F to 200°F (-18°C to 93°C)
T6
Temperature limits are solely based upon mechanical stress and certain
chemicals will reduce the maximum operating temperature. The allowable
temperature range for the process fluid is determined by the materials
in contact with the fluid being pumped. Consult a chemical resistance
guide for chemical compatibility and a more precise safe temperature
CAUTIONS — READ FIRST!
WARNING
CAUTION
= Hazards or unsafe practices which
could result in severe personal injury,
death or substantial property damage
= Hazards or unsafe practices which
could result in minor personal injury,
product or property damage.
limit. Always use minimum air pressure when pumping at elevated
temperatures.
CAUTION
It is the end user’s responsibility to maintain the
process fluid’s temperature during use.
CAUTION
Do not connect a compressed air source to the
exhaust port of the pump.
CAUTION
Do not lubricate air supply.
CAUTION
Do not exceed 120 psig (8.3 bar)
air-inlet pressure.
CAUTION
Do not exceed 10 psig (0.7 bar)
or 23 ft-H
2
O suction pressure.
CAUTION
Ensure all wetted components are chemically
compatible with the process fluid and the cleaning fluid.
CAUTION
Ensure pump is thoroughly cleaned and flushed
prior to installation into a process line.
CAUTION
Always wear Personal Protective Equipment (PPE)
when operating pump.
CAUTION
Close and disconnect all compressed air and bleed
all air from the pump prior to service. Remove all process fluid in a safe
manner prior to service.
CAUTION
Blow out all compressed air lines in order to
remove any debris, prior to pump installation. Ensure that the muffler is
properly installed prior to pump operation.
CAUTION
Ensure air exhaust is piped to atmosphere prior to a
submerged installation.
CAUTION
Ensure all hardware is set to correct torque values
prior to operation.
CAUTION
The equipment must be inspected for visible
damage prior to use.
This product can expose you to chemicals including
Nickel, Chromium, Cadmium, or Cobalt, which are known to the State of
California to cause cancer and/or birth defects or other reproductive harm.
For more information, go to www.P65Warnings.ca.gov.
WARNING