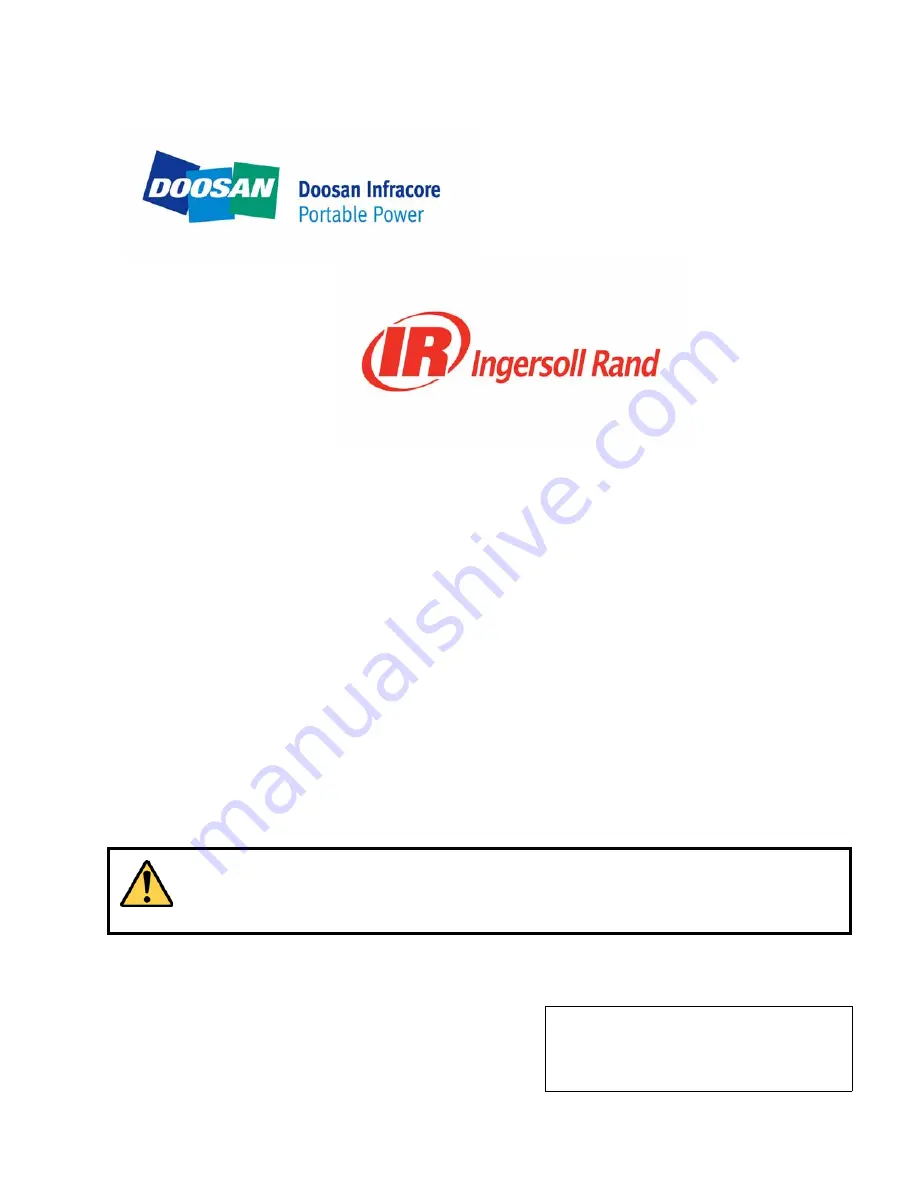
VHP300WIR, HP375WIR, XP375WIR, P425WIR
CODE: A & B
Doosan Infracore Portable Power
1293 Glenway Drive
Statesville, N.C. 28625
www.doosanportablepower.com
Book: 22442578 (02-09) Rev. A
This manual contains important safety information.
Do not destroy this manual.
This manual must be available to the personnel who operate and maintain this machine.
Operating & Maintenance Manual
Compressor Models
Doosan purchased Bobcat Company from Ingersoll-Rand Company in
2007. Any reference to Ingersoll-Rand Company or use of trademarks,
service marks, logos, or other proprietary identifying marks belonging
to Ingersoll-Rand Company in this manual is historical or nominative
in nature, and is not meant to suggest a current affiliation between
Ingersoll-Rand Company and
Doosan
Company
or the
products
of
either.
Revised (
10
-12)
Summary of Contents for Ingersoll Rand HP375 WIR
Page 2: ...2...
Page 7: ...7 TABLE OF CONTENTS Operating Maintenance Manual TITLE PAGE...
Page 8: ...8 Always use Ingersoll Rand Replacement parts...
Page 9: ...22442578 9 Foreword...
Page 12: ...12 22442578...
Page 13: ...22442578 13 Decals...
Page 15: ...Decals Operating Maintenance Manual 22442578 15...
Page 16: ...Operating Maintenance Manual Decals 16 22442578...
Page 17: ...Decals Operating Maintenance Manual 22442578 17...
Page 19: ...Decals Operating Maintenance Manual 22442578 19...
Page 22: ...22 22442578...
Page 23: ...22442578 23 Noise Emission...
Page 28: ...28 22442578...
Page 29: ...22442578 29 Safety...
Page 34: ...34 22442578...
Page 35: ...22442578 35 General Arrangement...
Page 43: ...22442578 43 Operating Instructions...
Page 62: ...62 22442578...
Page 63: ...22442578 63 Lubrication...
Page 84: ...84 22442578...
Page 85: ...22442578 85 Maintenance...
Page 103: ...Maintenance Operating Maintenance Manual 22442578 103...
Page 104: ...Operating Maintenance Manual Maintenance 104 22442578...
Page 107: ...22442578 107 Machine Systems...
Page 111: ...22442578 111 Service Tools...
Page 117: ...22442578 117 Fault Finding...
Page 122: ...122 22442578...
Page 123: ...22442578 123 Options...
Page 126: ...126 22442578...