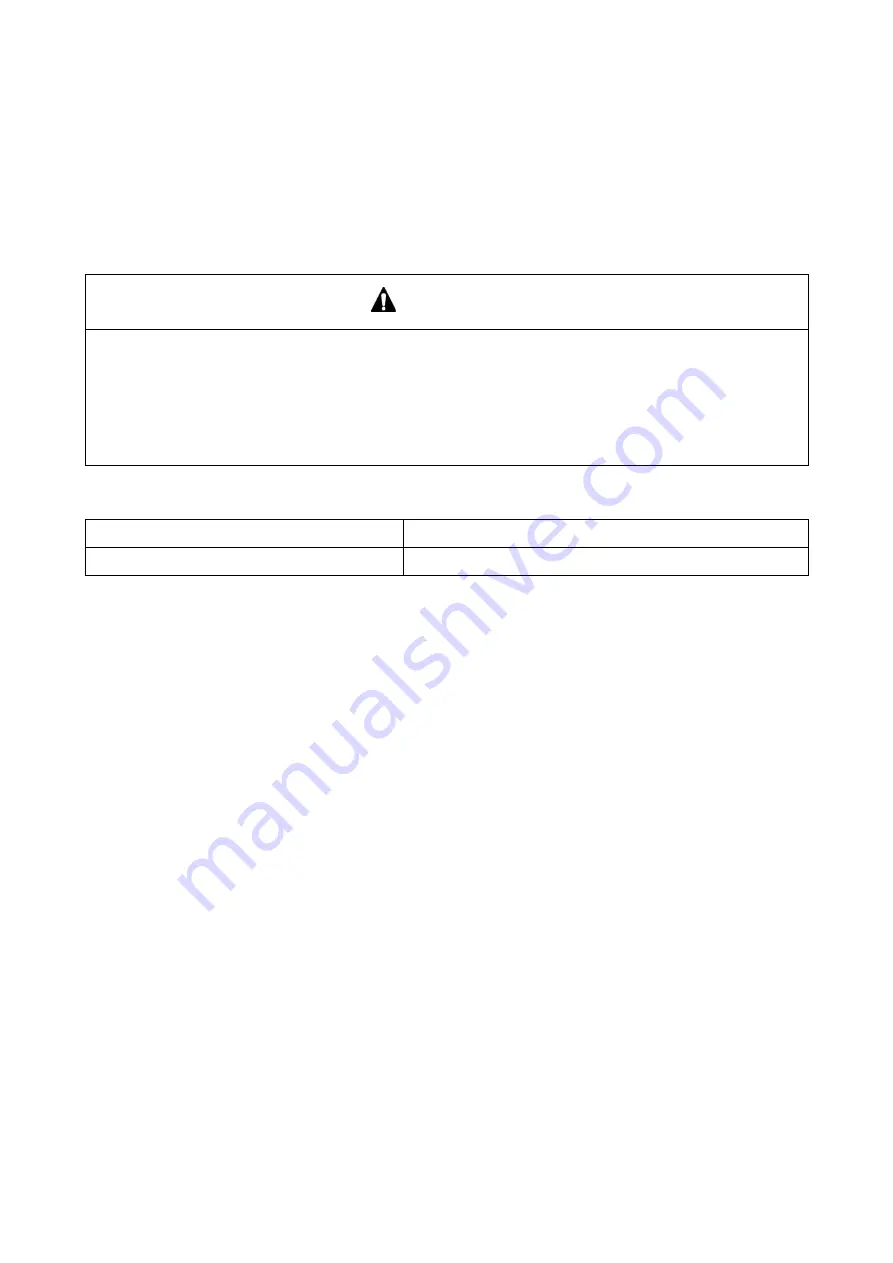
SPC000017
Steering Unit
CAUTION!
Follow all safety recommendations and safe shop practices outlined in the front of this manual or those
contained within this section.
Always use tools and equipment that is in good working order.
Use lifting and hoisting equipment capable of safely handling load.
Remember, that ultimately safety is your own personal responsibility.
MODEL
SERIAL NUMBER RANGE
SD310
010001 and Up
Steering Unit SPC000017
Page 1
Summary of Contents for DISD SD 310
Page 2: ......
Page 5: ...1SAFETY ...
Page 6: ......
Page 42: ...S0103010K Wheel Loader Safety Page 36 ...
Page 43: ...1SPECIFICATIONS ...
Page 44: ......
Page 47: ...Specifications for SD310 SPC000001 Page 3 ...
Page 51: ...Specifications for SD310 SPC000001 Page 7 ...
Page 52: ...ENGINE PERFORMANCE CURVES SPC000001 Specifications for SD310 Page 8 ...
Page 58: ...SPC000001 Specifications for SD310 Page 14 ...
Page 59: ...11GENERAL MAINTENANCE ...
Page 60: ......
Page 74: ...S0302000 General Maintenance Procedures Page 14 ...
Page 87: ...1FFRAME ...
Page 88: ......
Page 90: ...TABLE OF CONTENTS Specifications 3 Counterweight 3 SPC000003 Counterweight Page 2 ...
Page 98: ...SPC000005 Center Joint Articulation Joint Page 6 ...
Page 99: ...1ENGINE AND DRIVE TRAIN ...
Page 100: ...SPC000006 ...
Page 106: ...1 3 Engine Specifications 1 3 1 Specification SPC000006 5ton Diesel Engine Page 6 ...
Page 107: ...1 3 2 Engine power Production tolerance 5 5ton Diesel Engine SPC000006 Page 7 ...
Page 121: ...5ton Diesel Engine SPC000006 Page 21 ...
Page 122: ...SPC000006 5ton Diesel Engine Page 22 ...
Page 123: ...5ton Diesel Engine SPC000006 Page 23 ...
Page 124: ...SPC000006 5ton Diesel Engine Page 24 ...
Page 125: ...5ton Diesel Engine SPC000006 Page 25 ...
Page 126: ...SPC000006 5ton Diesel Engine Page 26 ...
Page 127: ...5ton Diesel Engine SPC000006 Page 27 ...
Page 128: ...SPC000006 5ton Diesel Engine Page 28 ...
Page 193: ...4 1 4 Diagnostics and troubleshooting 5ton Diesel Engine SPC000006 Page 93 ...
Page 198: ...1 DE08TIS 225PS SPC000006 5ton Diesel Engine Page 98 ...
Page 199: ... 7 Governor adjustment DE08TIS 225PS 5ton Diesel Engine SPC000006 Page 99 ...
Page 200: ...2 DE08TIS 240PS SPC000006 5ton Diesel Engine Page 100 ...
Page 201: ... 7 Governor adjustment DE08TIS 240PS 5ton Diesel Engine SPC000006 Page 101 ...
Page 208: ...4 3 6 Diagnostics and troubleshooting SPC000006 5ton Diesel Engine Page 108 ...
Page 209: ...5ton Diesel Engine SPC000006 Page 109 ...
Page 211: ...3 Construction 5ton Diesel Engine SPC000006 Page 111 ...
Page 218: ...4 4 7 Diagnostics and troubleshooting SPC000006 5ton Diesel Engine Page 118 ...
Page 219: ...5 SPECIAL TOOL LIST 5ton Diesel Engine SPC000006 Page 119 ...
Page 220: ...SPC000006 5ton Diesel Engine Page 120 ...
Page 223: ... Maintenance specification table 5ton Diesel Engine SPC000006 Page 123 ...
Page 224: ...SPC000006 5ton Diesel Engine Page 124 ...
Page 225: ...5ton Diesel Engine SPC000006 Page 125 ...
Page 226: ...SPC000006 5ton Diesel Engine Page 126 ...
Page 227: ...5ton Diesel Engine SPC000006 Page 127 ...
Page 228: ...SPC000006 5ton Diesel Engine Page 128 ...
Page 252: ...SPC000007 Transmission and Torque Converter Page 24 ...
Page 253: ...Transmission and Torque Converter SPC000007 Page 25 ...
Page 263: ...Transmission and Torque Converter SPC000007 Page 35 ...
Page 264: ...SPC000007 Transmission and Torque Converter Page 36 ...
Page 271: ...Transmission and Torque Converter SPC000007 Page 43 ...
Page 272: ...SPC000007 Transmission and Torque Converter Page 44 ...
Page 283: ...Transmission and Torque Converter SPC000007 Page 55 ...
Page 284: ...SPC000007 Transmission and Torque Converter Page 56 ...
Page 291: ...Transmission and Torque Converter SPC000007 Page 63 ...
Page 301: ...Transmission and Torque Converter SPC000007 Page 73 ...
Page 302: ...SPC000007 Transmission and Torque Converter Page 74 184 ...
Page 456: ...Hub drive axle assembly SPC000009 Front Axle Page 6 Figure 4 ...
Page 458: ...Main drive assembly SPC000009 Front Axle Page 8 Figure 5 ...
Page 500: ...Hub drive axle assembly SPC000010 Rear Axle Page 6 Figure 4 ...
Page 502: ...Main drive assembly SPC000010 Rear Axle Page 8 Figure 5 ...
Page 538: ...SPC000010 Rear Axle Page 44 ...
Page 539: ...1HYDRAULICS ...
Page 540: ......
Page 552: ...PARTS LIST Figure 2 SPC000012 Main Pump Page 4 ...
Page 562: ...PARTS LIST Figure 2 SPC000013 Steer Pump Page 4 ...
Page 576: ...Detailed list of spare parts Figure 2 SPC000014 Main Control Valve Page 4 ...
Page 580: ...SPC000014 Main Control Valve Page 8 ...
Page 583: ...GENERAL DESCRIPTION Work principle Figure 1 Feed Unit SPC000015 Page 3 ...
Page 585: ...Disassembly and assembly steps Figure 3 Feed Unit SPC000015 Page 5 ...
Page 586: ...SPC000015 Feed Unit Page 6 ...
Page 604: ...20 Take out oil compensating valve 4EA SPC000017 Steering Unit Page 10 Figure 22 ...
Page 611: ...GENERAL DESCRIPTION Work principle diagram Figure 1 Motor SPC000018 Page 3 ...
Page 620: ...SPC000018 Main Motor Page 12 ...
Page 627: ...General description Schematic diagram Hydraulic Schematic SD310 SPC000020 Page 3 ...
Page 628: ...SPC000020 Hydraulic Schematic SD310 Page 4 ...
Page 629: ...Hydraulic Schematic SD310 SPC000020 Page 5 ...
Page 630: ...SPC000020 Hydraulic Schematic SD310 Page 6 ...
Page 631: ...BRAKE ...
Page 632: ......
Page 636: ...PARTS LIST 2 Structure Chart of Brake System 3 SPC000021 Brake System Page 4 Figure 2 ...
Page 646: ...PARTS LIST Assembly structure chart SPC000022 Parking System Page 4 Figure 1 ...
Page 648: ...SPC000022 Parking System Page 6 ...
Page 649: ...1ELECTRICAL SYSTEM ...
Page 650: ......
Page 690: ...TABLE OF CONTENTS General Description 3 SD310 4 SPC000027 Electrical Schematic SD310 Page 2 ...
Page 692: ...SD310 ZF SPC000027 Electrical Schematic SD310 Page 4 ...
Page 693: ...Electrical Schematic SD310 SPC000027 Page 5 ...
Page 694: ...SPC000027 Electrical Schematic SD310 Page 6 ...
Page 695: ...1ATTACHMENTS ...
Page 696: ......