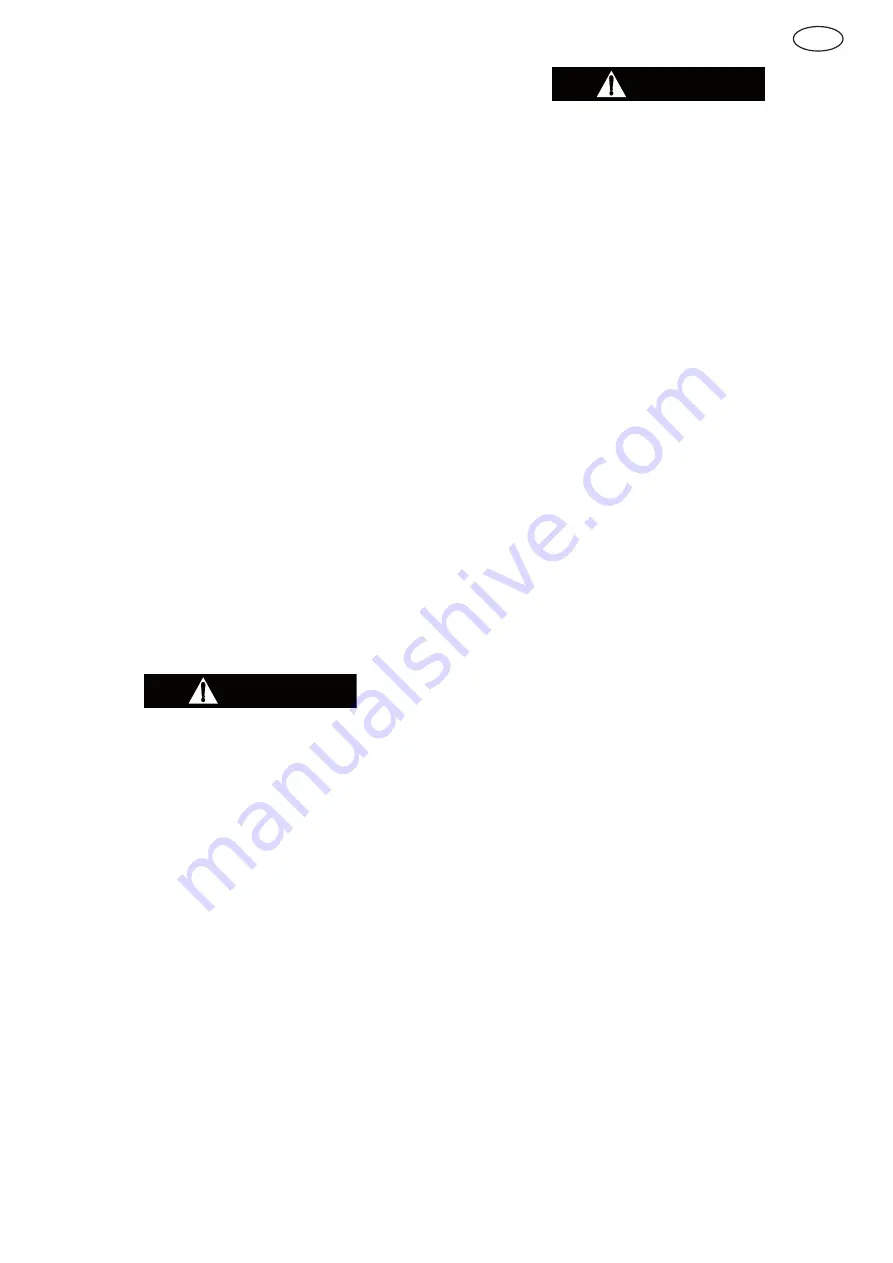
PLACING TOOL IN SERVICE
EN
7
OPERATION
Before starting the Hammer Drill, make certain the Assembly
Rod Nuts are tight 8Nm (6Ibs.ft.). If the tool is new, check and
tighten the Nuts after one or two hours of operation. Running
the tool with loose Assembly Rods will cause rapid wear and
breakage of parts.
Almost immediately after starting the Hammer Drill, check for
presence of oil at the exhaust ports and on the drill steel
shank. This is the only assurance that oil is travelling all the
way through the Hammer Drill. Break in a new Hammer Drill
slowly, usually half throttle for at least 30 minutes. Heating is
not unusual in a new Hammer Drill and it should be checked
carefully during the first few hours of operation. In most cases,
heating will be localized around the front end of the cylinder.
Test this area frequently with the hand. As long as the hand
can be held on the part comfortably, it is safe to continue
drilling. When the heat is great enough to cause discomfort,
stop the Hammer Drill and let it cool. Since lack of oil can
cause excessive heating, check again to see that the steel
shank is oily.
Collaring the Hole
1. When starting the bole hold the Hammer Drill firmly
against the work and use a steel short enough so that the
Hammer Drill can be handled comfortably.
2. Open the throttle gradually and drill at half throttle or less.
3. The Hammer Drill should be kept at right angles to the
work until the hole is collared, then repositioned for angled
drilling.
Drilling the Hole
1. Hold the Hammer Drill with both hands, spread feet apart,
and apply a firm steady pressure.
Spread legs and feet clear of the drill steel to prevent
injury if a steel breaks. When a steel breaks, the Hammer
Drill, with a piece of broken steel projecting from the
fronthead, drops to the ground suddenly.
2. Hold the Hammer Drill against the work to get maximum
efficiency from the tool. Failure to do this can result in an
excessive heat buildup at the front end of the Cylinder
which can damage the steel holder. Never back the steel
out of the hole at full throttle.
3. The correct amount of pressure for maximum drilling
efficiency can be gained only through experience, but
generally, the correct pressure is usually recognizable by
the rhythmic sound of the exhaust and the free rotation of
the steel.
4. Insufficient pressure will cause the Hammer Drill to
bounce and may crack carbide inserts.
5. Too much pressure will slow down the Hammer Drill and
may result in a stuck steel.
6. Keep the Hammer Drill, steel, and hole aligned at all
times. Hold the Hammer Drill with both hands.
Excess pressure on one side throws the Hammer Drill out
of alignment. Misalignment causes a drag on the rotation
parts which impairs drilling efficiency by reducing the
drilling speed and force of the blow. Misalignment will
also cause unnecessary chuck wear, and will soon cause
spalling of the piston and chipping or premature breakage
of the drill steel.
Cleaning the Hole
Always keep the hole clean and free of cuttings by "blowing"
the hole frequently. The bit must work on fresh material. If the
bit churns in its own cuttings, drilling speed is reduced, and the
possibility of the steel becoming stuck is increased.
Stuck Steel
When drilling moist formations there is often a tendency for
cuttings to pack in the hole immediately behind the bit forming
a "mud collar", Through action of the rotating bit, wet cuttings
pack solidly against the wall of the hole; the condition can
become aggravated and cause a stuck steel.
To remove a stuck steel:
1. Remove the Hammer Drill and make an attempt to loosen
the steel with a wrench.
2.
Do not try to pull a stuck steel with the Hammer Drill.
Heavy thrust loads can damage front end parts or loosen
the bit from the steel.
To prevent a stuck steel:
1.
Blow the hole often.
2.
Keep the bit working against fresh material.
Suggestions for Drillers
1. Never pound on a stuck steel. Nothing is accomplished,
and the drill and bit may be permanently damaged in the
process.
2. Never retract the Hammer Drill at full throttle.
3. Never strike the Hammer Drill with tools. The cylinder or
other part may become dented or damaged.
4. Never try to repair the Hammer Drill on the job. Take it to a
repair shop.
5. Never drag a Hammer Drill along the ground as the
exhaust port and other openings will scoop up dirt.
6. Always clear the air supply line before attaching it to the
Hammer Drill. Purging the line will prevent moisture, pipe
scale and other foreign matter from being carried into the
Hammer Drill with the air.
7. Always be sure the Hammer Drill is well lubricated. Adjust
the line oiler so that the shank of the steel always shows
an oil film but does not cause fogging.
8. Always keep the assembly rods tight and at an equal
tension.
9. Always keep the Hammer Drill aligned with the drill steel
and hole.
WARNING
CAUTION