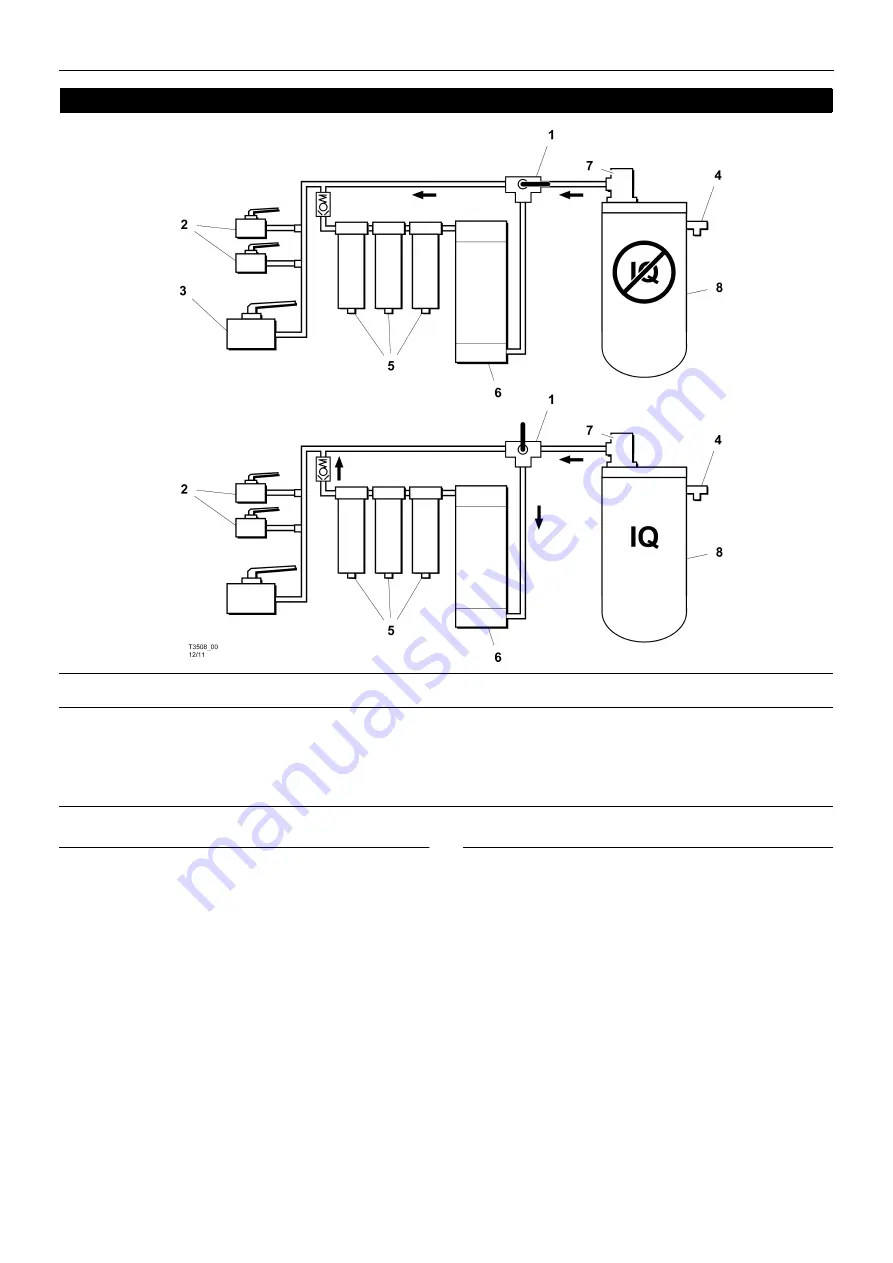
56
OPTIONS
9/235HA, 10/215HA
KEY
IQ SYSTEM
The IQ System is a complete, self-contained system which provides
cooler, cleaner air than from a standard portable compressor. The
system utilises an integral aftercooler, high-efficiency filtration, and a
patented condensate disposal system to provide the cool, clean air.
The condensate disposal system injects all liquid condensed from the
moisture separator and filters into the engine exhaust system where it
is vaporised by heat. This eliminates the need for collecting the
condensate, and the added cost of disposing of the condensate, which
is often regulated by local regulations.
When equipped with the low ambient feature, the IQ System
automatically adjusts movable louvres to control airflow through the
aftercooler, ensuring that the compressed air temperature always
remains above freezing temperatures (typically 7°C (45°F)) at any
ambient temperature down to -23°C (-20°F). This prevents the need for
heat tracing systems, or any manual adjustment to prevent freezing of
the compressed air system. All drain points for the condensate
handling system are heated with 24 VDC heaters, which are integral to
the compressor heater system.
Standard Non-Louvred configuration not to be operated below
freezing.
IQ SYSTEM OPERATING INSTRUCTIONS - 2
The compressed air exits the separator tank through the top cover
piping, and can then travel along one of two paths, selectable via
manual valving.
One path allows Standard Operation, which bypasses the IQ System,
and delivers air quality equivalent to a standard oil-flooded portable
compressor. If the IQ System is enabled by proper setting of the
selector valve, the compressed air first enters the aftercooler.
The aftercooler is cooled by the incoming compressor package air,
which is controlled by movable louvres mounted on the aftercooler (if
equipped with low ambient option). At most conditions, the louvres are
fully open, and maximum aftercooling is available. The compressed air
and condensate (water with a small amount of compressor lubricant)
exits the aftercooler and enters the moisture separator, where most of
the condensate is removed. The compressed air then flows through
two stages of filtration, where the oil - water and particles are removed
down to 0.01 micron.
At the bottom of the moisture separator and both filters are strainers
and constant-bleed orifices, which are sized to allow the maximum flow
of condensate while minimising compressed air loss.
OPTION - IQ SYSTEM
STANDARD OPERATION
1.
Three way valve
5.
Filters
2.
Ball valve 1
1
/
4
”
6.
Aftercooler
3.
Ball valve 2”
7.
Minimum pressure valve
4.
Safety valve
8.
Separator tank
IQ SYSTEM OPERATION
Summary of Contents for 10/215HA
Page 2: ......
Page 8: ...6 DECALS 9 235HA 10 215HA Engine oil drain...
Page 50: ...48 MACHINE SYSTEMS 9 235HA 10 215HA...
Page 51: ...MACHINE SYSTEMS 49 9 235HA 10 215HA...
Page 52: ...50 MACHINE SYSTEMS 9 235HA 10 215HA...
Page 53: ...MACHINE SYSTEMS 51 9 235HA 10 215HA...
Page 54: ...52 MACHINE SYSTEMS 9 235HA 10 215HA...
Page 55: ...MACHINE SYSTEMS 53 9 235HA 10 215HA...
Page 67: ......
Page 68: ...Doosan Bobcat EMEA s r o U Kodetky 1810 263 12 Dob Czech Republic www doosanportablepower eu...