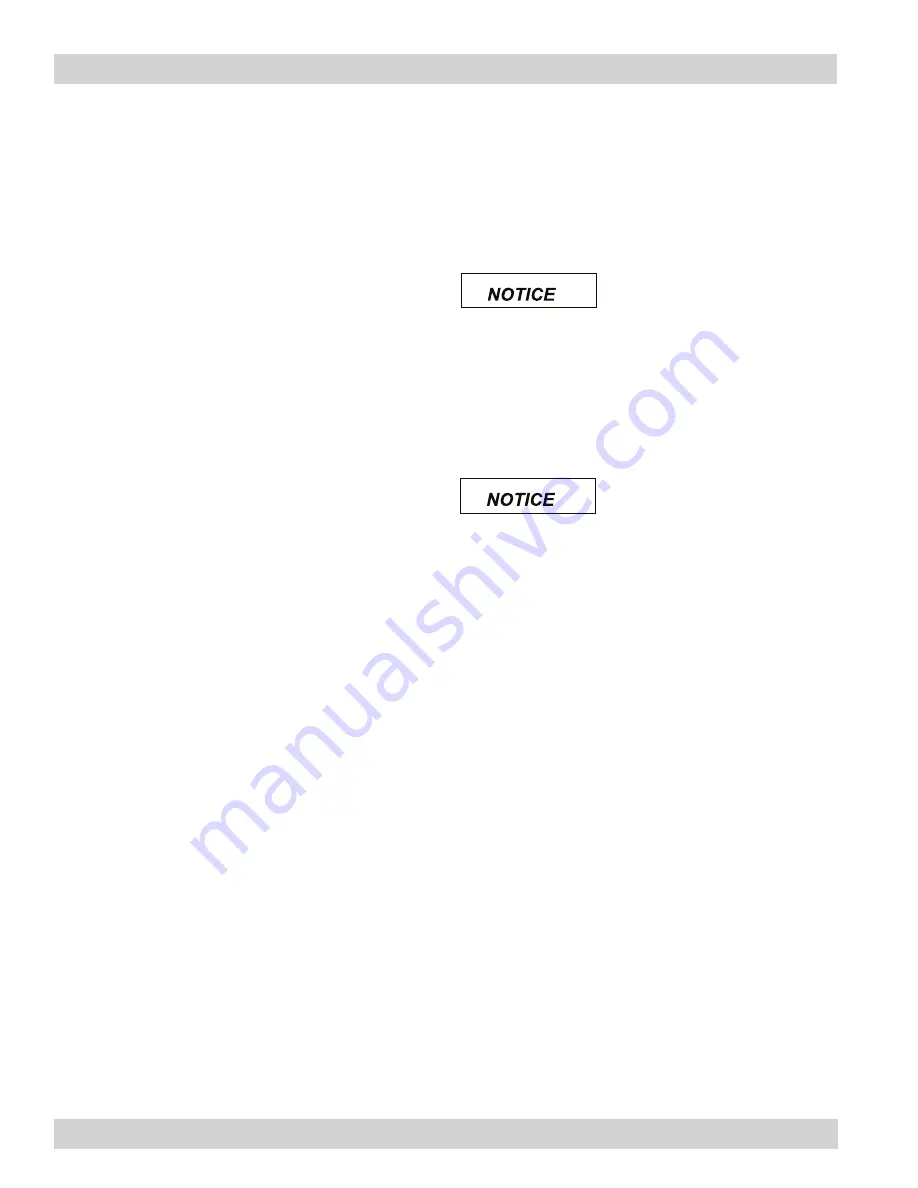
17
Donaldson Company, Inc.
Timer and Solenoid Specifications
Power to the solid-state timer is supplied to Terminals L1
and L2, which are intended to operate in parallel with the
positive displacement blower starter’s low-voltage coil.
On fan start-up, power is supplied to the timer and the
preset OFF time is initiated. At the end of the OFF time,
the timer energizes the solenoid valve to provide the ON
time cleaning pulse for the diaphragm valve and repeats
this cycle until the system is shut down. The timer can
also be wired for on demand cleaning with an external
pressure switch. If this option is selected, the high and
low limit pressure switch relays will be connected to the
TB2 corresponding terminals. Otherwise, the common
and high limit terminals on TB2 are jumpered to provide
continuous operation.
Note: If the collector was supplied with an
electrical control panel, the wiring diagram
supplied with the control panel takes
precedence over the general diagrams
shown in this manual.
Solenoid Connection
The collector is equipped with a solenoid valve (typically
120V) that controls the pulse-cleaning valve, which
cleans the filters.
Wire the solenoids to the solid-state timer following the
wiring diagram supplied with the collector. Filter life and
cleaning operation will be affected if not wired correctly.
Input
102-132V/50-60Hz/1Ph
Output Solenoids
2-3A max per channel
Pulse ON Time
Factory set at 100-milliseconds, or 1/10-second.
Do not adjust pulse ON time
unless the proper test equipment
is available. Too much or too little ON time can
cause shortened filter life.
Pulse OFF Time
Factory set at 10-seconds, the OFF time must be field
adjusted such that the pressure at the air reservoir
peaks at 7.5-psig just before the next pulse. Make final
adjustments by observing the LOAD ON light flashing on
the timer.
Open the valve to the air
reservoir gauge only when
adjusting OFF time.
Operating Temperature Range
-20° F to 130° F
Solenoid Valves
120V/60 Hz intermittent duty @ 20.9 watts
Interlocking
To ensure proper operation of the system the main
blower should not start unless the cleaning mechanism,
positive-displacement blower, and dust removal system
are all operating. It is recommeded that an interlock
device is installed between these motors. Failure of
interlocked devices should generally not shut down
the main blower, but should activate an alarm system,
if available. Failure of either a rotary airlock or screw
conveyor with separate drives should shut down all other
drives and alarm the operator. This will avoid filling the
collector with dust.
Time Delay, Start-Up
Starting motors at 3-second intervals is recommended to
minimize inrush current and to allow interlocking.
Time Delay, Shut-Down
A sequenced shut down approach is recommended for
optimal performance of the collector. After the main
blower shuts down, the remaining components should
continue to run for several minutes to empty the hopper
and dust removal system of all dust that drops from the
filter bags after the primary airflow stops.