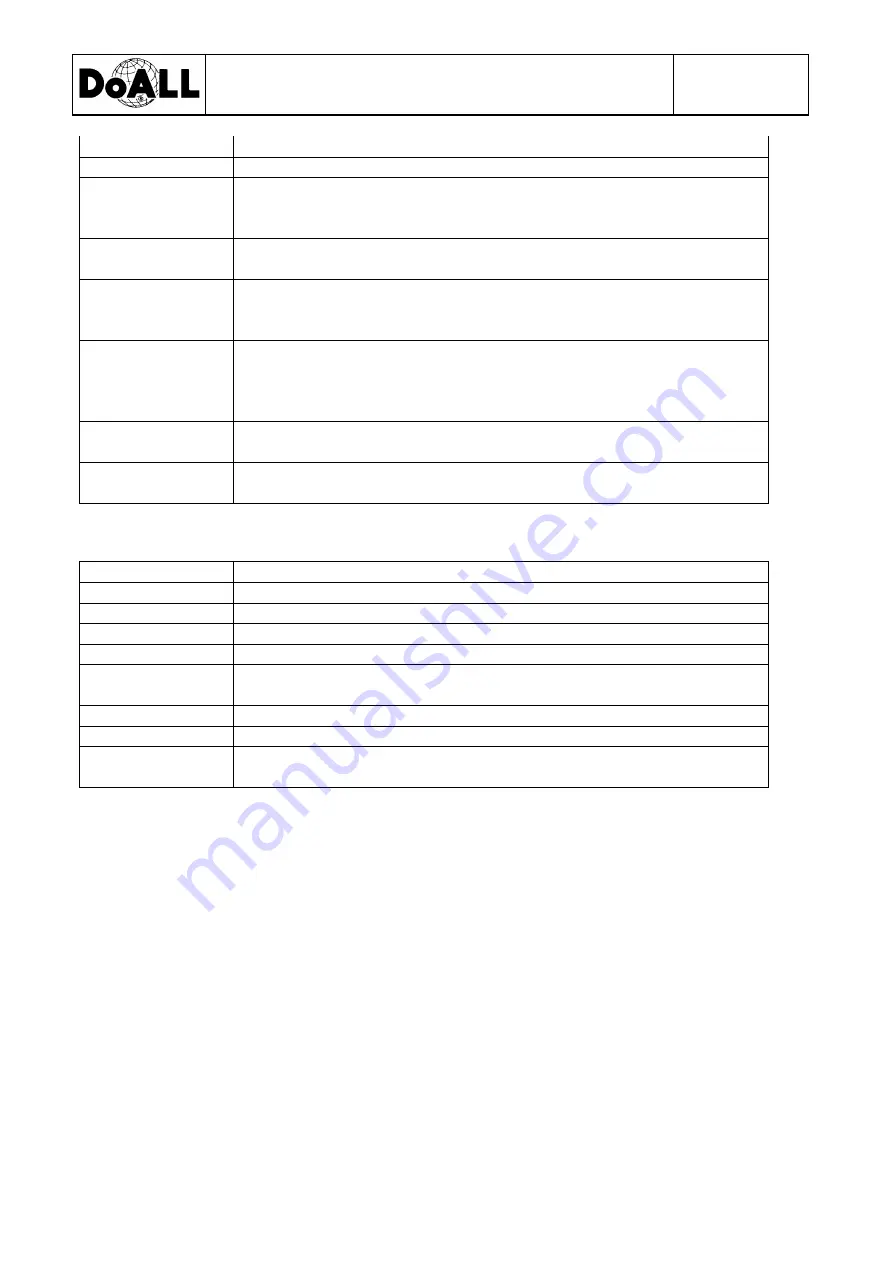
I
NSTRUCTION
&
P
ARTS
M
ANUAL
Pag.
28
Edition A
Undervol
The mains has been reached the Under voltage Limit.
Overload
The output current has almost reached the type-specific limit
HYST
The set limit value for the output current has been exceeded. The output
frequency is reduced step-by-step until the output current falls below the
limit value again (see TAB1, SUB IMOT, function S-INT =4).
RAMP
The set limit value for the output current has been reached. The
acceleration ramp is stopped (see TAB1, SUB IMOT, funct. S-INT = 3).
Br_limit
The dynamic braking power is near the programmed limit (configurable
by TAB2, func. BrLim). This message can be signalized by the relays or
the open collector outputs. (TAB3, funct. REL, OC1, OC2)
MPtFault
Motor potentiometer function: it was enabled a preset frequency with a
motor rotation sense different of the actual. The output frequency re-
mains unchanged (TAB1 funct. JOG = MPt). (Only with Softw. D2A-
STD)
Overtemp
The inverter (heat sink) temperature reaches the limit value.
(Only with Softw. D2A-STD)
Ot_motor
The motor temperature reaches the limit value.
(Only with Softw. D2A-STD)
13.3.6 Operating error messages
M
ESSAGE
D
ESCRIPTION
UNDERVOL
Under voltage has been detected in the link.
OVERVOLT
The voltage in the link has reached the over voltage value.
OVERLOAD
The output current has exceeded the type-specific limit value.
OVERTEMP
The inverter (heat sink) temperature is too high.
ILIMIT
The set limit value for the output current has been exceeded
(see TAB1, SUBIMOT, S-INT = 1 or 2).
1<4Ma
The speed reference line is interrupted or the set point is less than 4 mA.
Br_limit
The dynamic braking power has reached its programmed limit.
Ot_motor
The motor temperature has been reaching the limit
value for more than 7 seconds. (Only with Softw. D2A-STD)
1.
Inverter stopped. Automatic error reset as soon as the link voltage rises above the under volt-
age value.
2.
Inverter stopped. If the AUTORESET function is activated (see TAB3, SUB XPAR, function
SW3), a reset is possible by setting or the
START/STOP
input, or the
ENABLE
input, or by
setting the set point to zero.
3.
The motor is decelerated with the deceleration ramp and the inverter is stopped. An error re-
set can be performed as described in Item 2.
4.
The motor is decelerated with the deceleration ramp and the inverter is stopped until the tem-
perature doesn’t fall below the limit value. If the AUTORESET function is activated (see
TAB3, SUB XPAR, function SW3), a reset is possible by setting or the
START/STOP
in-
put, or the
ENABLE
input, or by setting the set point to zero.
5.
Behavior with Softw. D2A-STD: see 4) Behavior with Softw. D2A-1300: see 2)
13.3.7 Hardware error messages
An error which is established during the self-test phase or during operation is shown on the dis-
play by the message ‘‘ERROR’’ together with an error number. The inverter is stopped by the
safety devices.