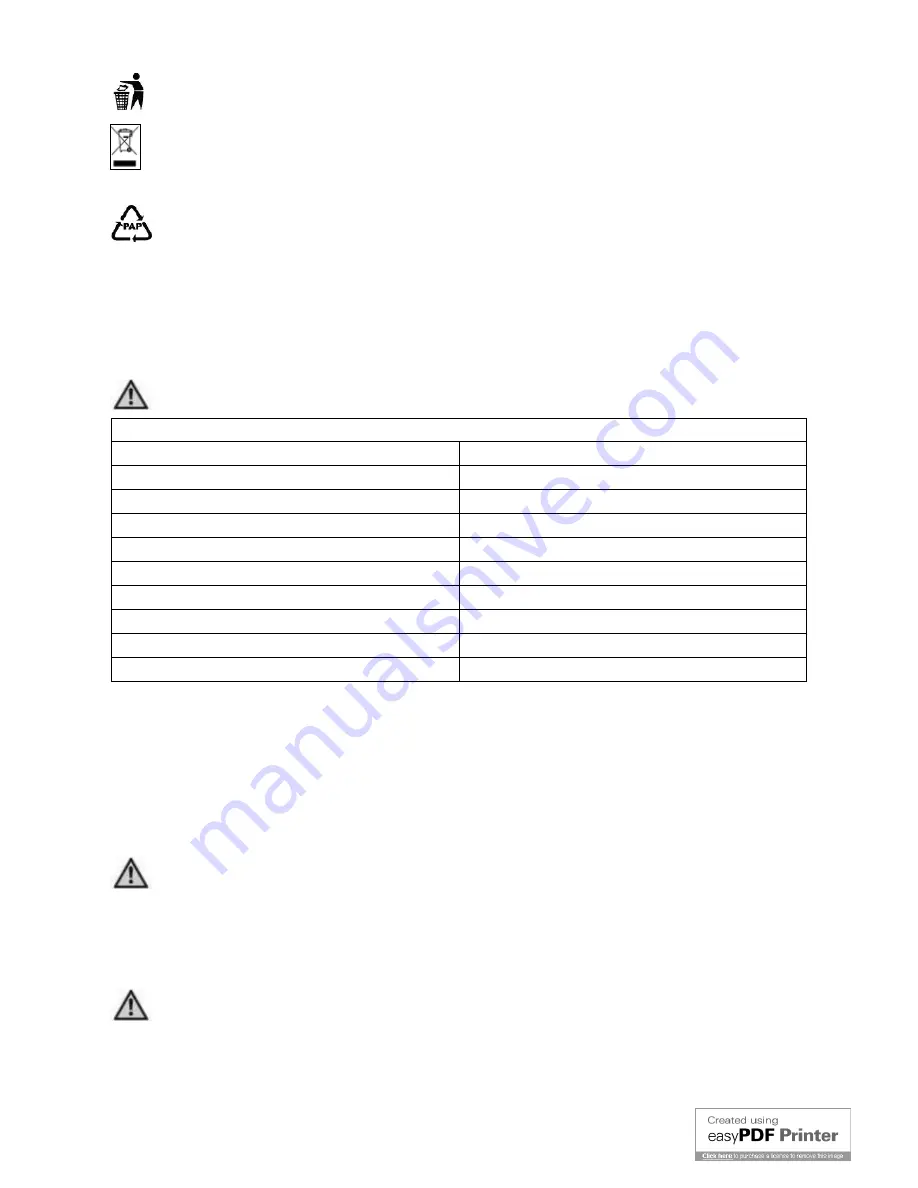
7
Don’t litter, dispose the waste correctly
Damaged and liquidated electric or electronic devices have to be handed over in designated places for
recycling.
Cardboard wrapping can be disposed in designated places only.
ELECTRICAL CONNECTION
Use 230V ~ 50Hz alternate voltage equipped with a ground conductor to supply your machine.
Ensure that the power supply corresponds to this voltage, that it is protected by a differential and magnetic
thermal switch, and that the ground system is efficient. If your machine does not work when connected to a
socket, check carefully the power supply features.
WARNING: KEEP THE TOOLS AND THE EQUIPMENT AT A SAFE DISTANCE FROM CHILDREN
TECHNICAL SPECIFICATIONS
Model No
ST-250 BDS
Motor
230V~50Hz / 800W
Disc speed
1440 min
ˉ
¹
Belt speed
8,6 m/s
Grinding disc diameter
Ø 250 mm
Sander belt size
150 x 1220 mm
Disc worktable tilt
0º to 45º
Belt tilt
0º to 90º
Table size
355 x 200 mm
Weight (Gross/Net)
50 kg / 47 kg
The specifications in this manual are given as general information and are not binding. We reserve the right to
effect, at any time and without prior notice, changes or alterations to parts, fitting and accessory equipment
deemed necessary for any reason whatsoever.
REMOVAL OF PACKAGE AND CLEANING
The machine is delivered into a carton packaging. Take out the machine and all the components from the
packaging. Peel the protection off, where present: the protection can be removed with a damp, soft cloth. Do not
use acetone, petrol or painting solvents.
IMPORTANT:
Always lift the machine by the base or by the transport handle, if present.
Should any part result defective or imperfect, do not use the machine in order not to compromise the
efficiency and the safety of the tool. Contact an authorized Service Centre to have the detective part
replaced.
Do not throw the carton before the machine is completely assembled.
WARNING:
By cleaning the machine, after unpacking, do not use petrol or other petrol-based solvents because
extremely inflammable.
The use of such products causes fire or explosion hazard.