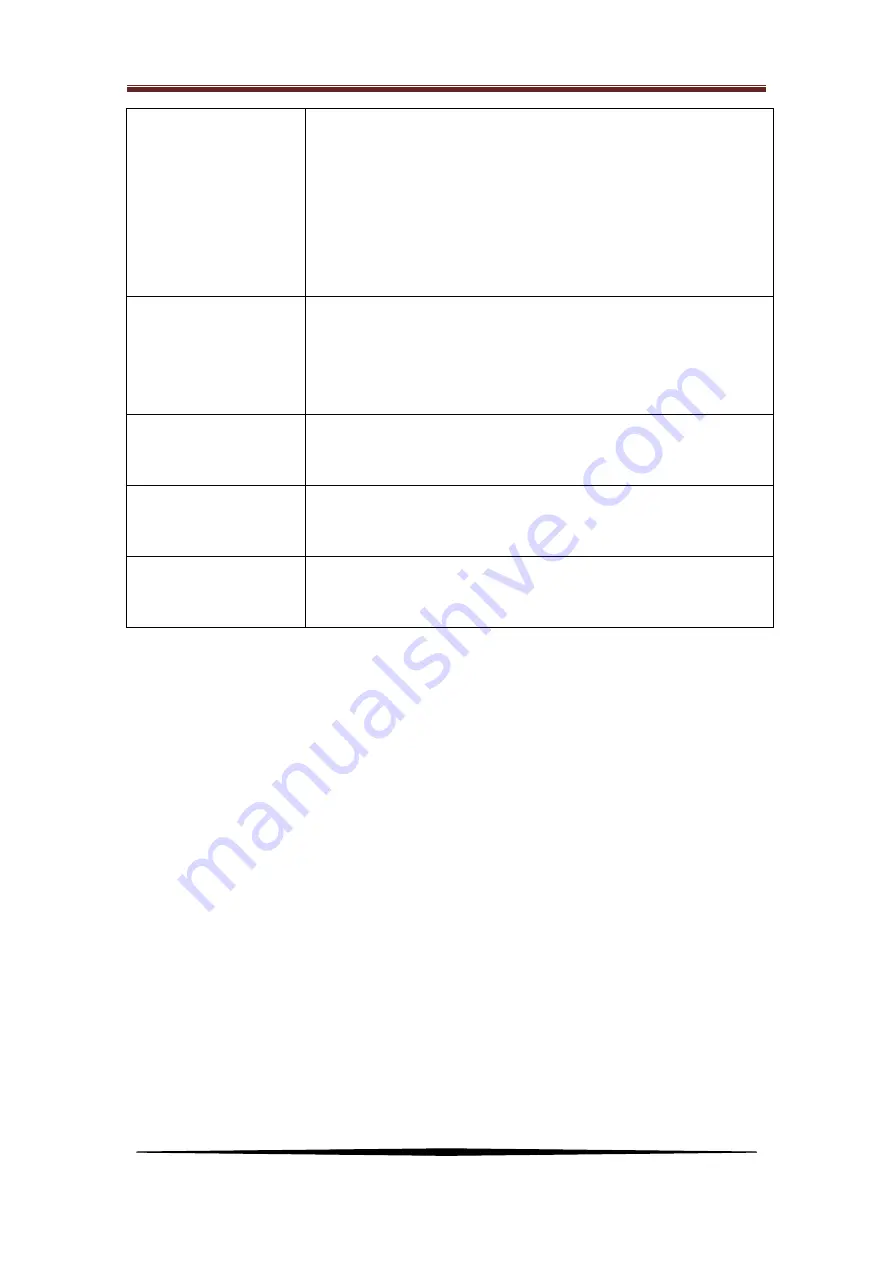
Part V:Troubleshooting
14
Rack catching on tail
tube (at end of stroke).
Rack returning very slow
or not going all the way
back.
➢
Adjust carriage hold downs (slide guides).
➢
Check for wood chips or debris between ram bushing plate and
beam.
➢
Check rack lift bearing for alignment or damage.
➢
Return spring is unhooked or damaged. Reconnect or replace as
needed.
➢
Machine wedge end too low. Must be almost level or wedge end
slightly higher.
Operator Lever
Snapping out of gear or
not staying in gear.
➢
Lever not all the way forward when rack comes under full load.
Push lever quicker and more forcefully into the full forward
position.
➢
Ram has been overloaded at lower part of face. Check rack gear
for straightness.
Rack slamming back too
fast.
➢
Wedge end of machine too high. Must be almost level with ram
end or just slightly higher.
➢
Springs not operating properly. Fix or replace as needed.
Machine does not seem
to have full splitting
power.
➢
The belts may be too loose and slipping. Adjust or replace belts as
needed.
Operator Lever not
engaging rack with
pinion gear.
➢
Clean wood chips or other debris from under rack.
➢
Clean accumulated dirt from frame where carriage assembly rests
against rubber bumpers.