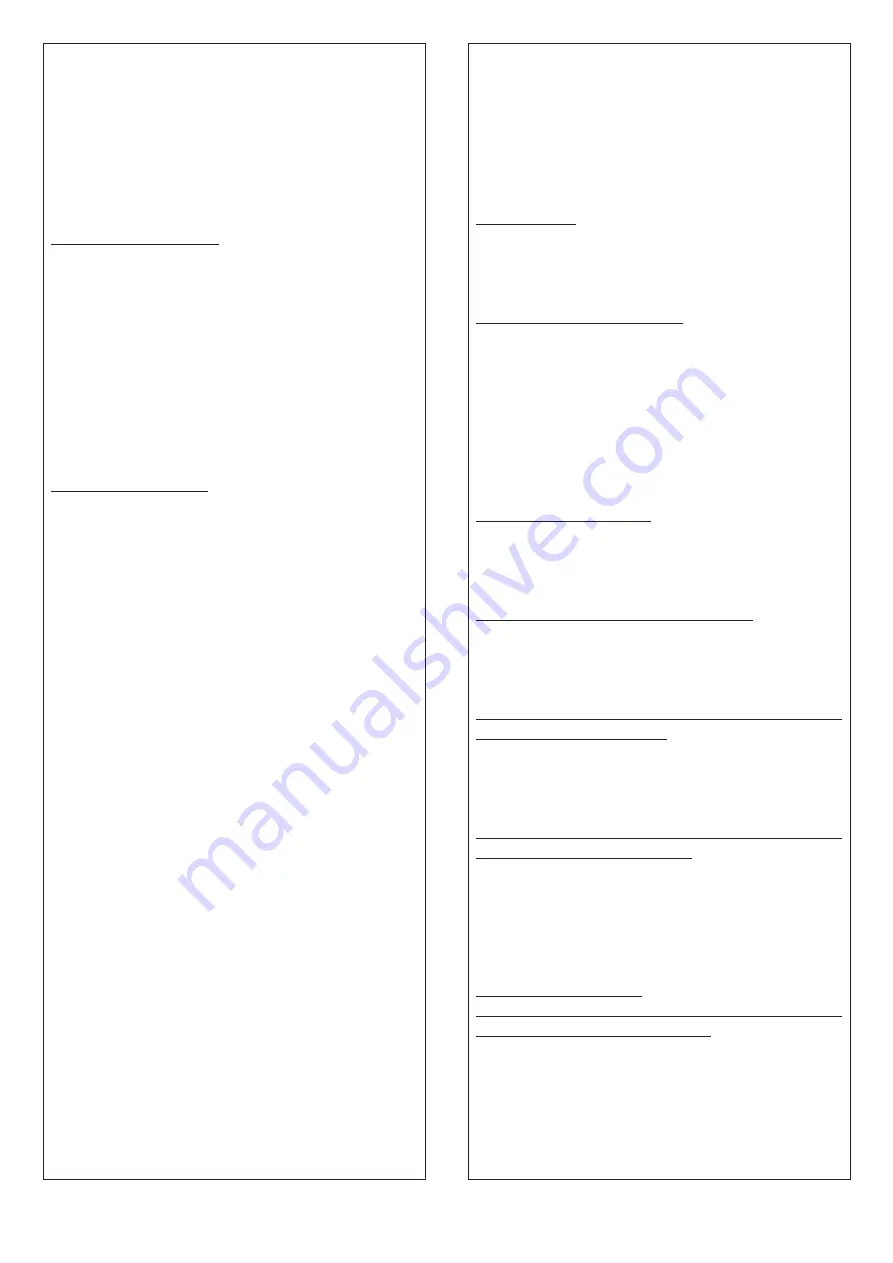
4
Do not use the cable for purposes for which it is not
intended. Do not use the cable to pull the plug out of
the outlet. Protect the cable from heat, oil and sharp
edges.
Have your electric tool repaired by a qualified
electrician. This electric tool conforms to the
applicable safety regulations. Repairs may only be
performed by an electrician using original spare parts.
Otherwise accidents can occur.
Work Area & Store Area
Keep the work area orderly. Disorder in the work area
can lead to accidents.
Take environmental influences into account. Do not
expose electric tools to rain. Do not use electric tools
in a damp or wet environment. Make sure that the
work area is well-illuminated. Do not use electric tools
where there is a risk of fire or explosion.
Securely store unused electric tools. Unused electric
tools should be stored in a dry, elevated or closed
location out of the reach of children.
b) Specific Safety Rules
Machine Use and Care
• Never turn the drill press on until the table is clear
of all foreign objects (tools, scraps, etc.).
• Always keep hands and fingers away from the drill
bit.
• Do not drill materials without a flat surface.
• Never start the drill press with the drill bit pressed
against the workpiece.
• Make sure the table lock is tightened before
starting the drill press.
• Never layout, assemble, or set-up any work on the
table while the drill is on.
• Make sure the drill bit is securely locked in the
chuck.
• Make sure the chuck key is removed from the chuck
before turning power on.
• Adjust the table or depth stop to avoid drilling into
the table.
• Always stop the drill before removing scrap pieces
from the table.
• Use clamps or a vise to secure a workpiece to the
table. This will prevent the workpiece from rotating
with the drill bit.
• Do not wear gloves when operating a drill press.
• Set the drill press to the speed that is appropriate
for the material being drilled.
• If any part of the drill press is missing/ damaged or
if the electrical components fail to perform properly,
shut the power OFF and unplug the drill press. Replace
missing, damaged or failed parts before resuming
operation.
• Before leaving the machine, shut the power off,
remove the drill bit and clean the table.
• Take care of your tools. Keep cutting tools sharp
and clean in order to be able to work better and more
safely. Follow the instructions for lubrication and
for tool replacement. Check the connection cable of
the electric tool regularly and have it replaced by a
recognized specialist when damaged. Check extension
cables regularly and replace them when damaged.
Keep the handle dry, clean and free of oil and grease.
Residual Risks
Despite proper use, additional residual risks cannot
be completely ruled out. The following risks may arise
due to the nature of the drill press:
Mechanical hazards related to:
Machine parts or workpieces:
• Shape
• Relative location
• Mass and velocity (kinetic energy of elements in
controlled or uncontrolled motion)
• Mechanical strength
• Crushing hazard
• Cutting or severing hazard
• Entanglement hazard
• Drawing-in or trapping hazard
Electrical hazards due to:
• Contact of persons with live parts (direct contact)
• Contact of persons with parts which have become
live under faulty conditions (indirect contact)
• Electrostatic phenomena
Hazards generated by noise, resulting in:
• Hearing loss (deafness), other physiological
disorders (loss of balance, loss of awareness)
• Interference with speech communication, acoustic
signals.
Hazards generated by materials and substances (and
their constituent elements)
processed or used by the machinery
• Hazards from contact with or inhalation of harmful
fluids and dusts
• Fire hazard
Hazards generated by neglecting ergonomic principles
in machinery design related to:
• Unhealthy postures or excessive effort
• Hand-arm or foot-leg anatomy
• Local lighting
• Mental overload and underload, stress
• Human error, human behaviour
• Design, location or identifiation of manual controls
Combination of hazards
Unexpected start up, unexpected overrun/ overspeed
(or any similar malfunction) from:
• Failure/disorder of the control system
• External influences on electrical equipment
• Errors made by the operator (due to mismatch of
machinery with human
characteristics and abilities)
Summary of Contents for DJMBD13-40
Page 1: ...Bench Drill Item No DJMBD13 40 BENCH DRILL Original Operating Manual ...
Page 3: ...2 1 2 3 4 5 6 7 8 9 10 11 12 13 14 15 16 17 ...
Page 15: ...14 ...
Page 18: ...17 12 ...