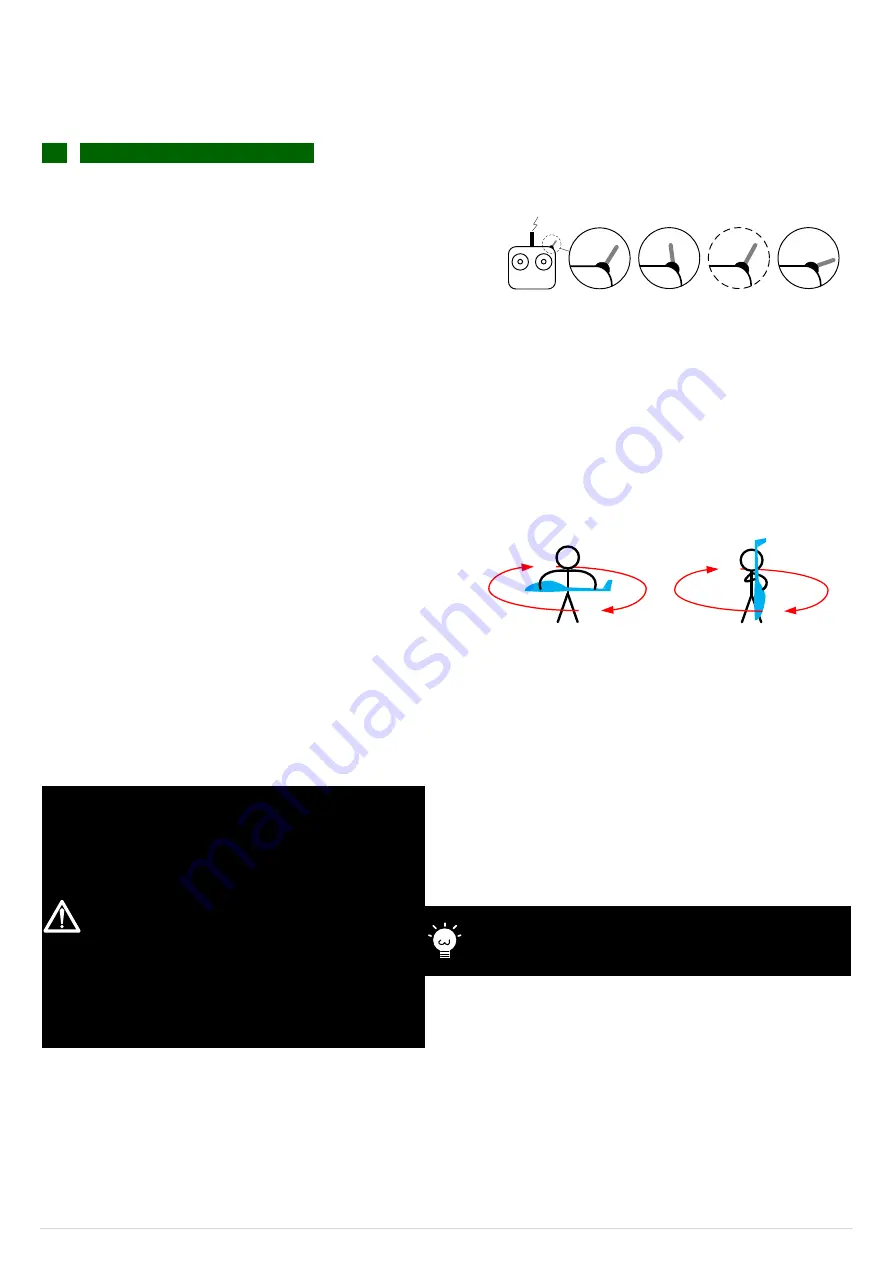
©2012 DJI Innovations. All Rights Reserved.
20 |
Flight
C1
Digital Compass Calibration
Lite
WKH Lite customers can skip this step.
Why calibrate the compass?
Ferromagnetic substances placed on helicopter or around its
working environment will affect the reading of earth magnetic
for digital compass, it also reduces the accuracy of the
helicopter control, or even reads incorrect heading.
Calibration will eliminate such influences, and ensure WKH
system performs well in a non-ideal magnetic environment.
When to do it?
1
The first time you install WKH on your helicopter.
2
When the helicopter mechanical setup is changed:
a) If the GPS/Compass module is re-positioned.
b) If
electronic
devices
are
added/removed/
re-positioned (Main Controller, servos, batteries, etc).
c) When the mechanical structure of the helicopter is
changed.
3
If the flight direction appears to be shifting (meaning the
helicopter doesn’t “fly straight”).
4
The LED indicator often indicates abnormality blinking
when the helicopter yaws. (It is normal for this to happen
only occasionally.)
Where to do it?
Do the calibration in an open area, away from parked cars,
metal railings, and any metal around. Sometimes a bunch of
keys in your pocket might affect calibration.
Calibration procedure:
Tx
1
2
3
3 Position
Switch
STEP1:
Enter calibration mode: quickly slide the control mode
switch from
Position-1
to
Position-3
for 10 times, and LED
indicator will be constantly on in blue;
STEP2:
Calibration in horizontal: rotate you helicopter along with
the horizontal surface until the green light is on constantly,
then go to the next step;
STEP3:
Calibration in vertical: while green light is constantly on,
hold your helicopter vertically and rotate it along with its
vertical axis, keep rotating until the green light is off,
meaning the calibration is finished.
STEP4:
After you finished the calibration, LED indicator will show
whether the calibration was successful or not:
If white light turns on for 3 seconds, calibration succeeds,
calibration mode will
auto exit
;
If red light keeps blinking quickly, the calibration has failed.
Slide the control mode switch one time to cancel current
calibration, and then re-start from step 1 for re-calibration.
1
Don’t calibrate your compass where there is
strong
magnetic
interference,
such
as
magnetite, car park, and steel reinforcement
under the ground.
2
DO NOT carry ferromagnetic materials with you
during calibration, such as keys or cell phones.
3
Y
ou don’t need to rotate your helicopter on a
precise horizontal or vertical surface, but keep at
least 45° difference between horizontal and
vertical calibration.
4
WKH cannot be work in the polar circle.
If you keep having calibration failure, it might suggest that
there is very strong magnetic interference around the GPS
& Compass module, please avoid flying in this area.