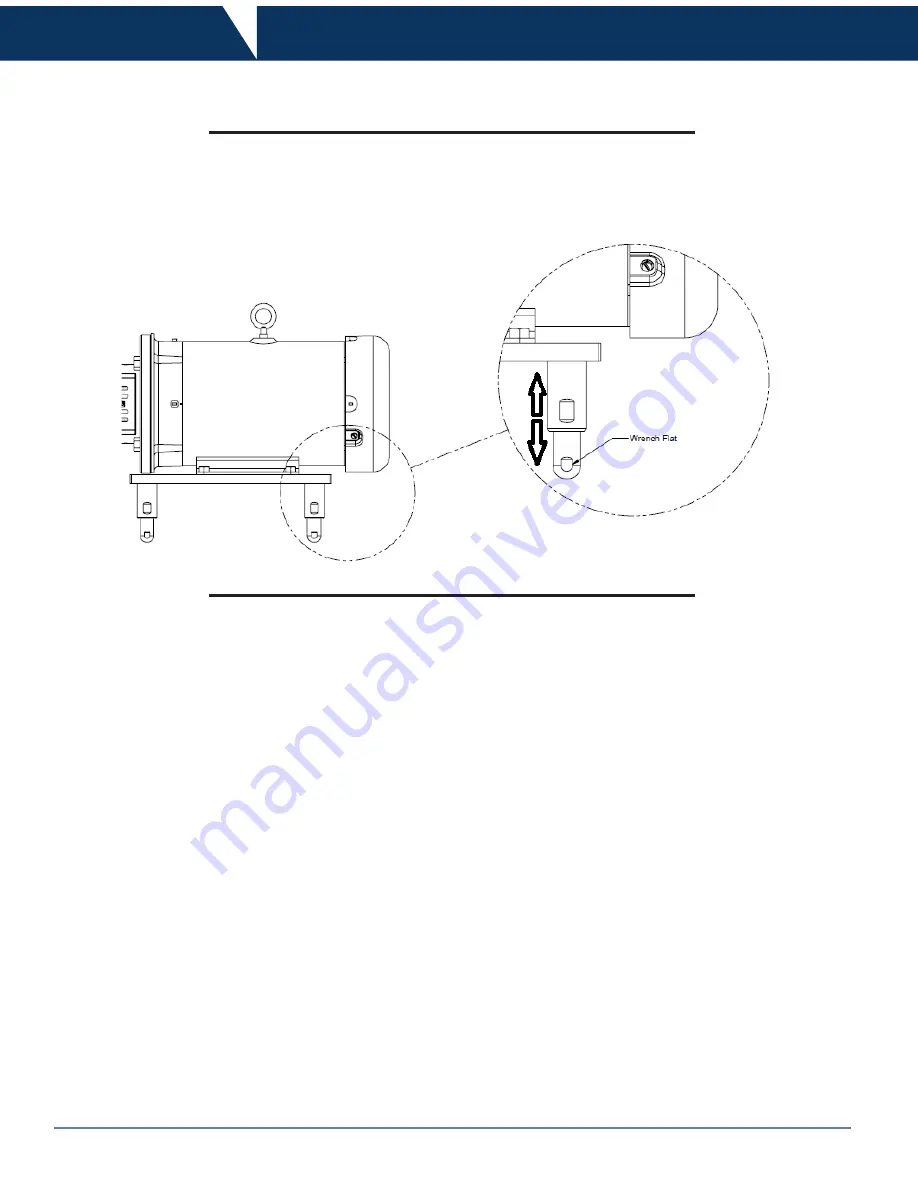
12
Instruction & Operation Manual
800.789.1718
• Pump will perform at its best when located as close as possible to the liquid supply.
•
Supply piping should be short and straight to ensure the pump has an adequate supply of liquid to it at all times.
• The pump should be located in an area where it is easy to inspect and do preventative maintenance or repair.
Location
The pump can be easily leveled by installing the optional leg kit. Using an adjustable wrench, fit the wrench to the wrench flat
shown in the diagram below. When viewed from the top, turn
the wrench in a counter-clockwise direction to lower the leg, or clockwise direction to raise the leg.
Optional Leg Kit Installation and Leveling
Installation