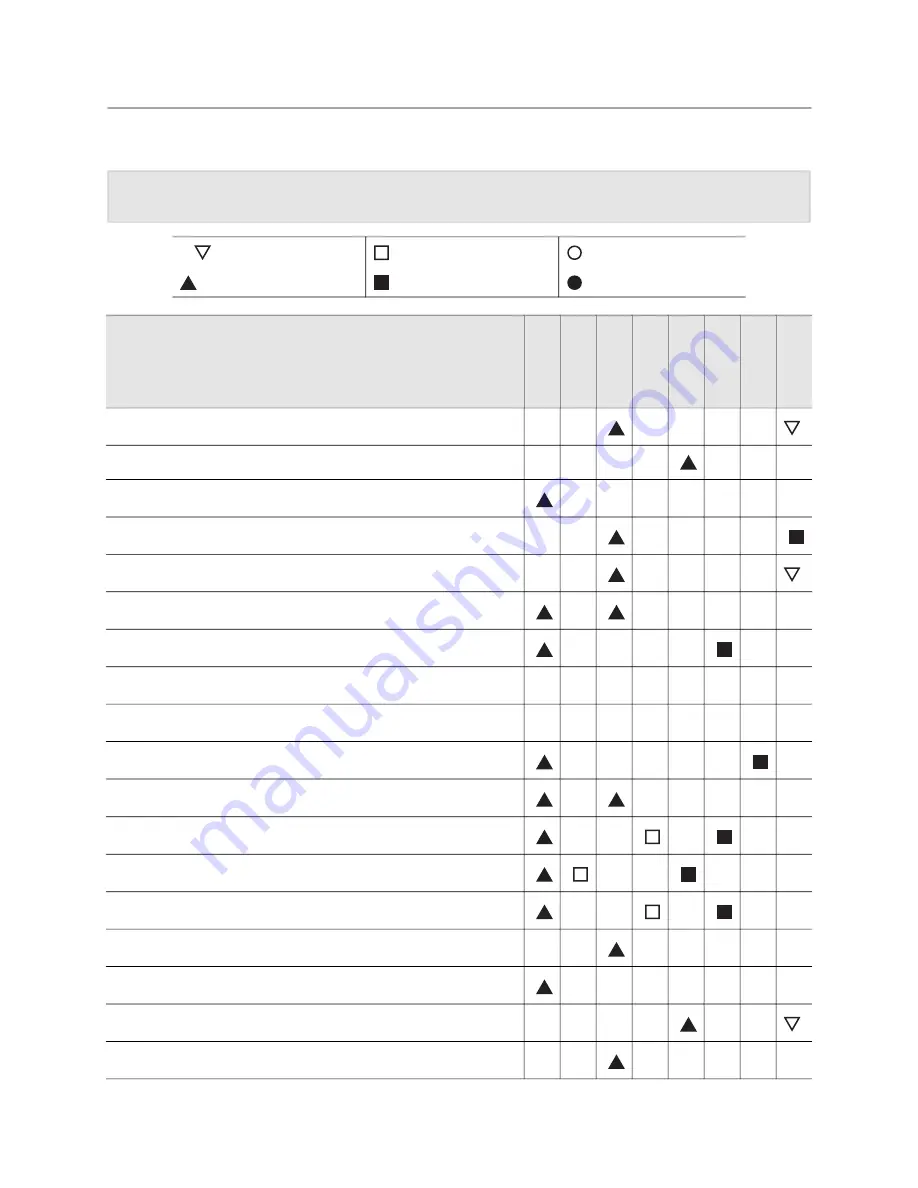
Cx Series Operator’s Manual
Service - 83
Service Interval Chart
Service Interval Chart
IMPORTANT:
Chart indicates first instance of repeated service procedures. See detailed information
below.
Adjust, service, or test
Change, initial
Lube, initial
Check
Change
Lube
Service
St
ar
tu
p
5
Ho
ur
s
10
H
ou
rs
20
H
ou
rs
50
H
ou
rs
10
0
Ho
ur
s
50
0
Ho
ur
s
As
N
ee
de
d
Battery
Boom mounting bolts
Cooler, hydraulic fluid
Digging chain
Digging chain tension
Dust ejector valve (C24x & C30x)
Filter, air
Filter, engine oil (see Oil, engine)
Filter, hydraulic fluid (see Fluid, hydraulic)
Fluid, hydraulic
Hydraulic hoses
Oil, engine (C12x & C24x)
Oil, engine (C16x)
Oil, engine (C30x)
Restraint bar
Track lug nuts
Track tension
Trench cleaner