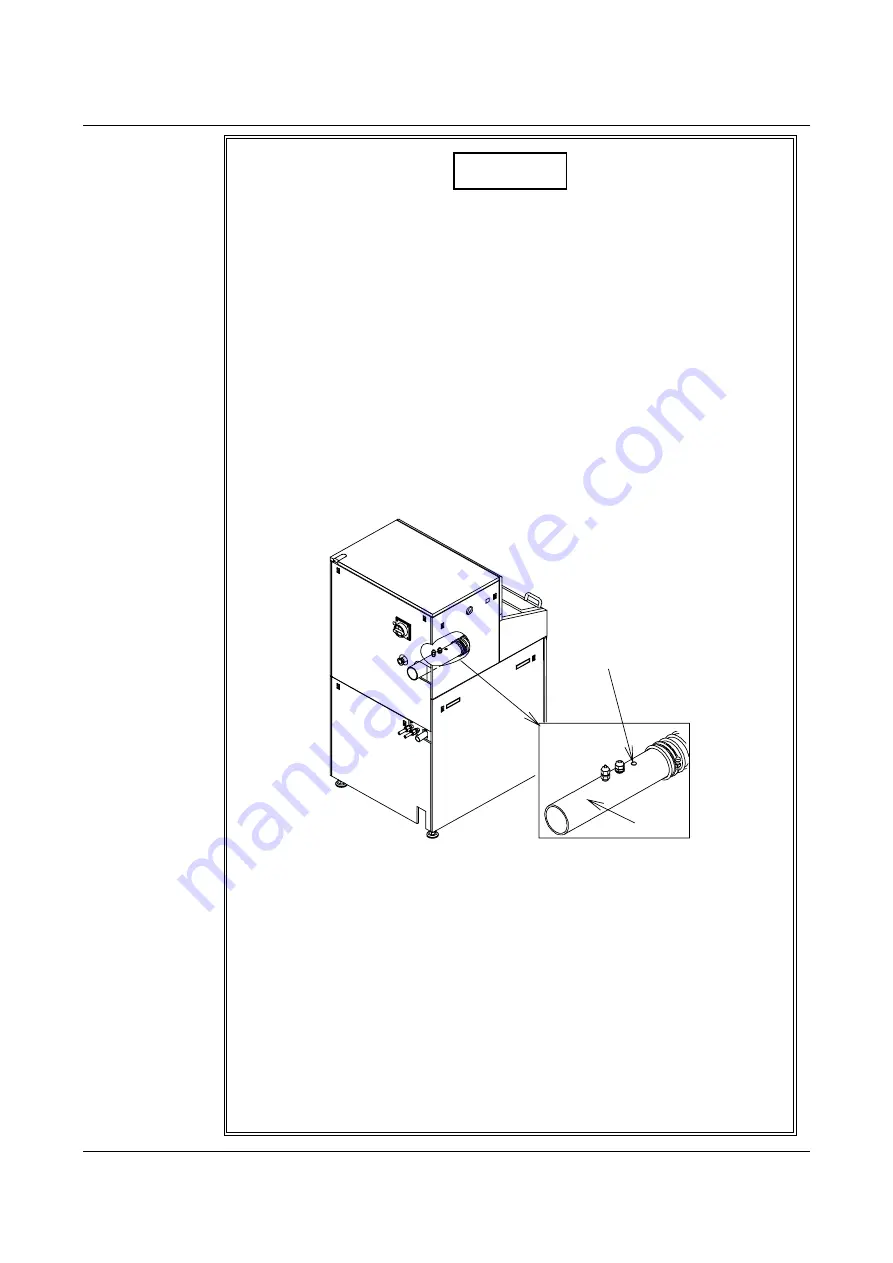
A-3
General safety precautions
Continued
NOTICE
- Proper installation of safety device
If the covers or other parts with safety interlocks are broken,
immediately stop the machine and repair broken parts.
- Air exhaust, water drainage and contamination control
Since harmful substance may be generated depending on the
cutting work type and machining characteristics, air exhaust, water
drainage and contamination control/disposal must be properly
completed in compliance with applicable environmental protection
codes.
- Exhaust sampling port
The machine requires an exhaust operation. When measuring the
exhaust for the machine to fulfill legal requirements, use the
sampling port, which is provided at the location indicated below.
(connection port: Rc1/4)
Duct
Sampling port
[Rc1/4]
- Facility side interlock connection terminal (Special user
specification)
To permit the facility side to provide air exhaust and water drainage
interlock, the machine is equipped with air exhaust and water
drainage reservoir tank interlock connection terminals.
When connecting these terminals to the facility side interlock
system, contact your nearest DISCO office.
- Machine relocation/disposal
In the case of relocation or disposal of the machine, the
presentation of detailed precautionary notes and the management
of new installation site data will be done by DISCO.
If you want to relocate or dispose the machine, contact your nearest
DISCO office or DISCO service office.
Sample