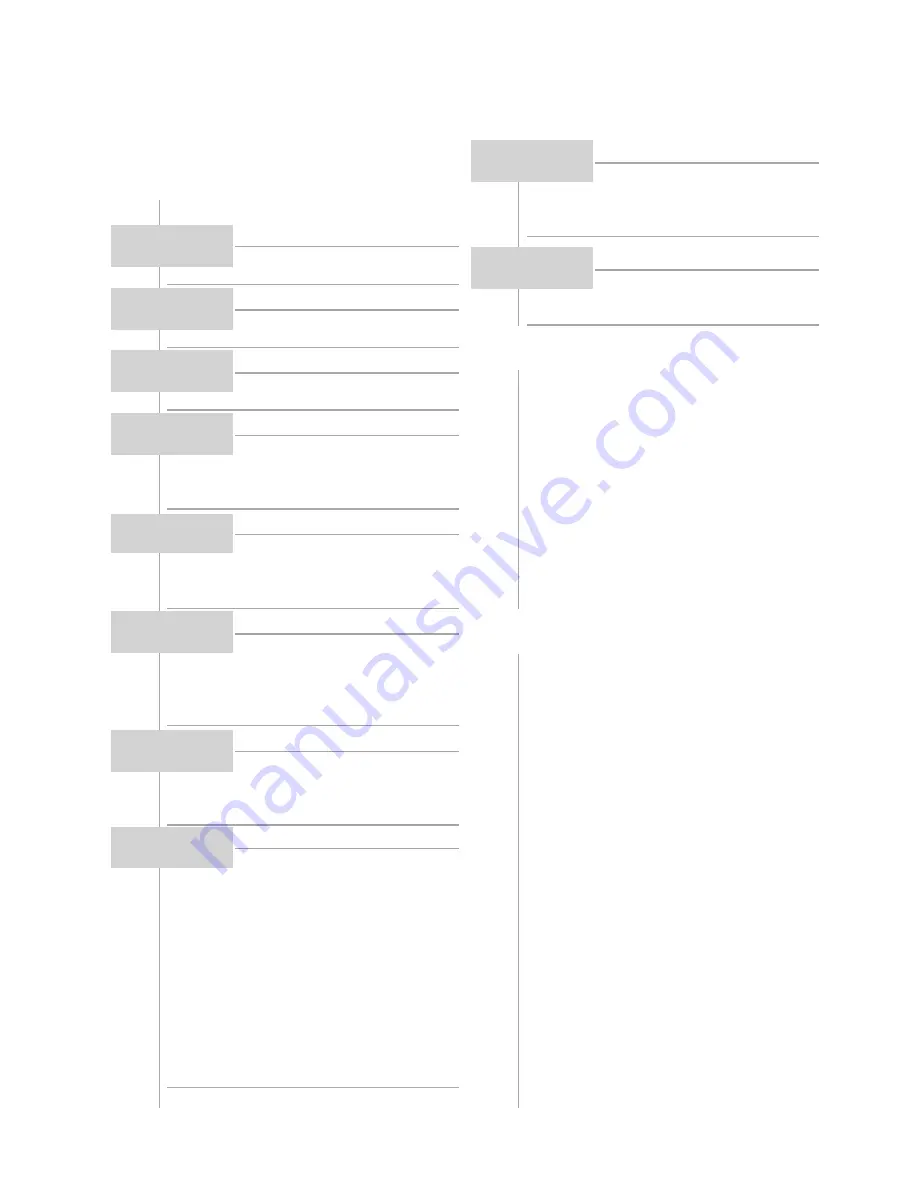
3
READ IMMEDIATELY
1.1 Important Information
The heat pump is not secured to the
wooden pallet.
The heat pump must not be tilted
more than max. 45° (in either direction).
Do not lift unit by the holes in the
panel assemblies!
In the case of large-capacity heating
circuits, the installed expansion vessel (24
litres, 1.0 bar admission pressure) must be
supplemented by an additional vessel.
The brine solution must contain at
least 25 % of an antifreeze and corrosion
protection agent on a monoethylene glycol or
propylene glycol basis.
On connecting the electrical load
lines, the clockwise phase sequence must be
observed (in the case of an incorrect phase
sequence the heat pump will deliver no output
and generate a lot of noise).
Commissioning of the heat pump
must be performed in accordance with the
installation and operating manual of the heat
pump controller.
1
PLEASE READ IMMEDIATELY
CAUTION!
CAUTION!
CAUTION!
CAUTION!
CAUTION!
CAUTION!
CAUTION!
CAUTION!
Caution - Heating Contractors !
Depending on the filling water quality and
quantity, in particular in the case of mixed
installations and plastic pipes, mineral deposits
(rust sludge, lime) may form, impairing the pro-
per functioning of the heating installation. A
reason for this is the water hardness and
oxygen dissolved in the filling water as well as
additional oxygen from the air, which may
penetrate via valves, fittings and plastic pipes
(oxygen diffusion). As a preventive measure it
is recommended that a physical water conditio-
ner such as ELYSATOR be used.
CAUTION!
1.2 Legal Provisions and Directives
This heat pump conforms to all relevant DIN/VDE
regulations and EU directives. For details refer to
the EC Declaration of Conformity in the appendix.
The electrical connection of the heat pump must be
performed according to and conforming with all re-
levant VDE, EN and IEC standards. Beyond that, the
connection requirements of the local utility compa-
nies have to be observed.
The heat pump is to be connected to the heat source
and heat distribution systems in accordance with all
applicable provisions.
1.3 Energy-Efficient Use of the Heat
Pump
By operating this heat pump you contribute to the
protection of our environment. A prerequisite for an
efficient operation is the proper design and sizing of
the heating system and the heat source system. In
particular, it is important to keep water flow
temperatures as low as possible. All energy
consumers connected should therefore be suitable
for low flow temperatures. A 1 K higher heating water
temperature corresponds to an increase in power
consumption of approx. 2.5 %. Underfloor heating
systems with flow temperatures between 30 °C and
40 °C are optimally suited for energy-efficient
operation.
The supplied strainer is to be fitted
in the heat source inlet of the heat pump
in order to protect the evaporator against
contamination.
Any work on the heat pump may
only be performed by authorised and qualified
customer service agents.
CAUTION!