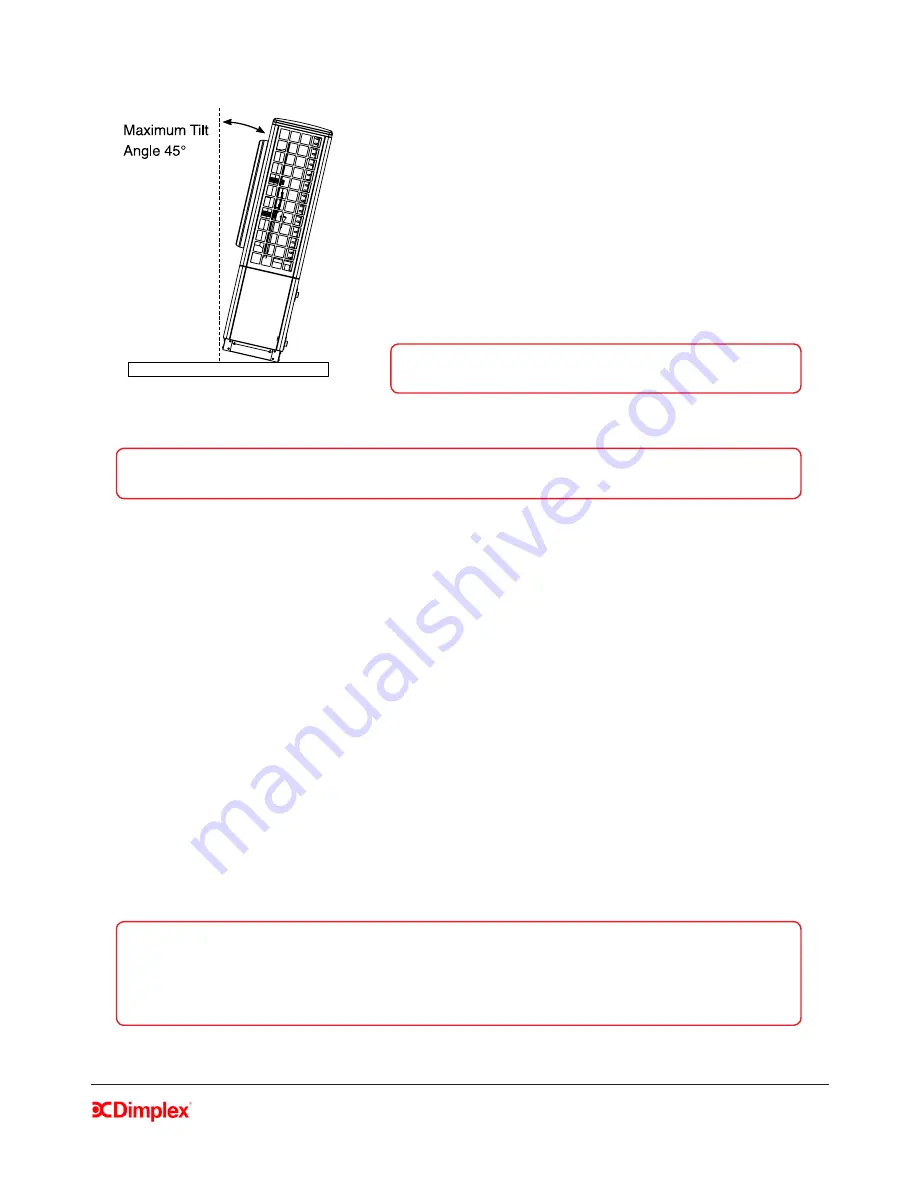
Millbrook House, Grange Drive, Hedge End, Southampton, SO30 2DF
0844 879 3587
dimplex.co.uk | gdcgroup.co.uk
6
1.2 Important Safety Information
•
Do not tilt the heat pump by more than 45° in any
direction.
•
Do not lift without using correct lifting devices.
•
Ensure that all clearance dimensions are observed - this
is important for correct heat pump operation and air flow.
•
Use a suitable lifting device in accordance with any
relevant health and safety regulations.
•
Do not move or transport the heat pump flat.
WARNING:
When using lifting rods to lift the heat pump,
straps must also be used to prevent toppling.
Figure 1: Maximum tilt angle
NOTE:
Leaving a clear pathway for delivery will allow the heat pump to be delivered as close to the
installation site as possible to minimize moving / lifting.
• Never use cleaning agents containing sand, soda, acid or chloride as these can damage surfaces
/ components.
• Do not use muddy or dirty water to fill the heating system. This can cause components to
malfunction and poses a corrosion risk to the system.
• If the heat pump may be disconnected from the power supply for long periods of time, or where
power supplies are susceptible to failure, antifreeze must be added to the system.
Example: Mono ethylene glycol at 25% volume to protect down to -14°C in a holiday home.
• Use a suitable filtration protection system and a corrosive additive to prevent the formation of
oxides or solids in the heat pump condenser.
• This appliance can be used by children aged from 8 years and above and persons with reduced
physical, sensory or mental capabilities or lack of experience and knowledge if they have been
given supervision or instruction concerning use of the appliance in a safe way and understand
the hazards involved.
• Children shall not play with the appliance.
• Cleaning and user maintenance shall not be made by children without supervision.
NOTE:
The heat pump contains refrigerant at high pressure.
Safety measures are in place to avoid system pressure build up;
Stage 1: Pressure transducer stops compressor.
Stage 2: Pressure switch switches heat pump off. All safety devices reset automatically.