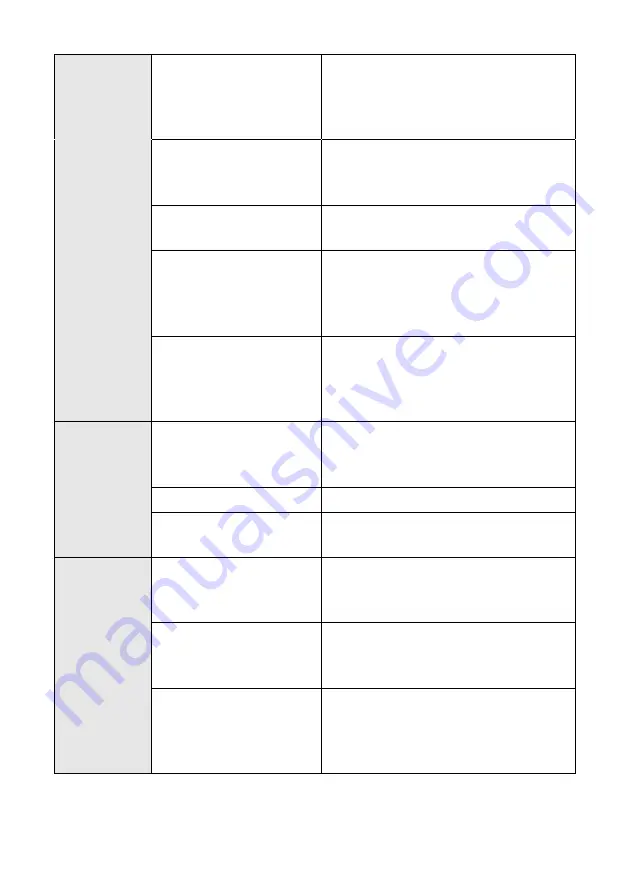
26
The expansion valve
bulb failure or
incorrect mounting
position
An expansion valve replacement,
and proper installation position
bulb
Summer too much
refrigerant perfusion
Remove excess refrigerant, the
high pressure in the control 2.3~
Between 2.8 Mpa
Outdoor condenser
fouling
Cleaning the surface of dust and
dirt condenser
Axial fan does not turn
Check axial fan static resistance
and the grounding resistance, such
as fan coil burning should be
replaced;
Systems non-
condensable gases
mixed with
Height from the system gas
discharge portion, the system re-
evacuated if necessary, charge
fluoride work
Fan
overload
Airflow is too large
Check the filter installation,
whether to select an error
windshield
Voltage is too low
Check input power
Fan motor winding
fault
Check whether the motor windings
normal
Low-
pressure
protection
alarm
Low Voltage
Protection Switch
Fault
Replace the low protection switch
Expansion valve is too
small
Appropriately adjusting the
opening degree of the expansion
valve
The expansion valve
bulb failure or
incorrect mounting
position
An expansion valve replacement,
and proper installation position
bulb