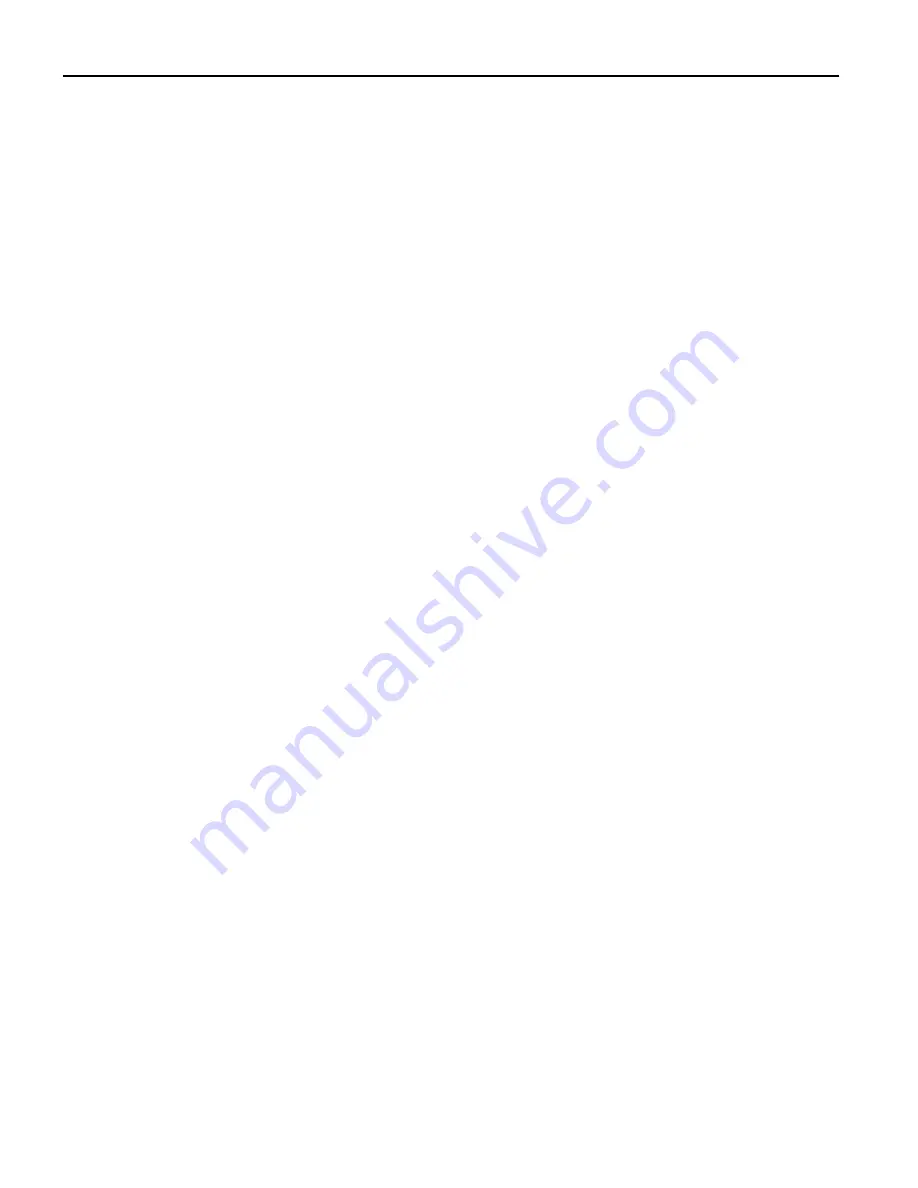
26 PKC SERIES PACKAGED STEPPER DRIVES USER GUIDE
The ideal method of setting up the clock for optimum performance is
to use the control system as an indexer so that the number of step
pulses fed to the motor is controlled. If this is not possible or if the
system is to be manually controlled, refer to the following sections
which explains the procedure to adopt when no indexer is available.
Adjustment Using
an Indexer
Attach a light pointer to the motor shaft and align it with a reference
mark. Turn preset controls RV1, RV2 & RV3 fully anticlockwise, RV4
& RV5 fully clockwise (see Figure 2-10).
Arrange to index through one revolution of the motor, i.e. 400 steps
in the 400 step/rev. mode, using only the Home speed. (If the
control system wants to call up Fast speed, detach the lead from the
Fast input). Index the motor and check that the pointer is aligned
when the motor stops. Repeat the indexing operation and slowly
turn the Home speed preset RV2 clockwise until stalling occurs when
the motor starts or stops. This will be indicated either by the motor
failing to run at all or by the pointer being misaligned when the motor
stops.
The point where stalling is about to occur represents the upper limit
of the Home speed, so to allow a safety margin the control should be
turned back about 1 turn. The speed setting obtained by this method
should be reduced by about 50% if instantaneous reversal is
required without loss of synchronism. If the Fast input lead was
detached, reconnect it and arrange to run the motor continuously at
the Fast speed. If this is not possible, set up the indexer to perform
a large number of steps. When the motor has run up to speed,
slowly rotate the Fast speed preset RV3 clockwise until the motor
stalls. Turn the control back by not less than 1 turn to give a working
margin.
Now arrange to index the motor through a whole number of
revolutions by generating say 4000 steps, giving 10 revolutions in the
400 step/rev. mode. Ensure that the indexer initiates deceleration
(by removing the Fast input) well before the finish of the index. Start
with the pointer aligned with the reference mark, index the motor and
check that the pointer is once again aligned when the motor stops.
Repeat the indexing operation and slowly rotate the Acceleration
Rate preset RV4 anticlockwise until the motor stalls on acceleration.
When this happens the motor will usually stop, but under exceptional
circumstances it may result only in missed steps which will be
indicated by the pointer stopping short when the motor comes to
rest. Turn RV4 back about 1 turn from the point where stalling
occurs. Continue to index the motor and slowly rotate the
Deceleration Rate preset RV5 anticlockwise until the motor stalls on
deceleration. This will be shown by the pointer over-shooting when
the motor comes to rest. Turn RV5 back about 1 turn from this point.
Artisan Scientific - Quality Instrumentation ... Guaranteed | (888) 88-SOURCE | www.artisan-scientific.com