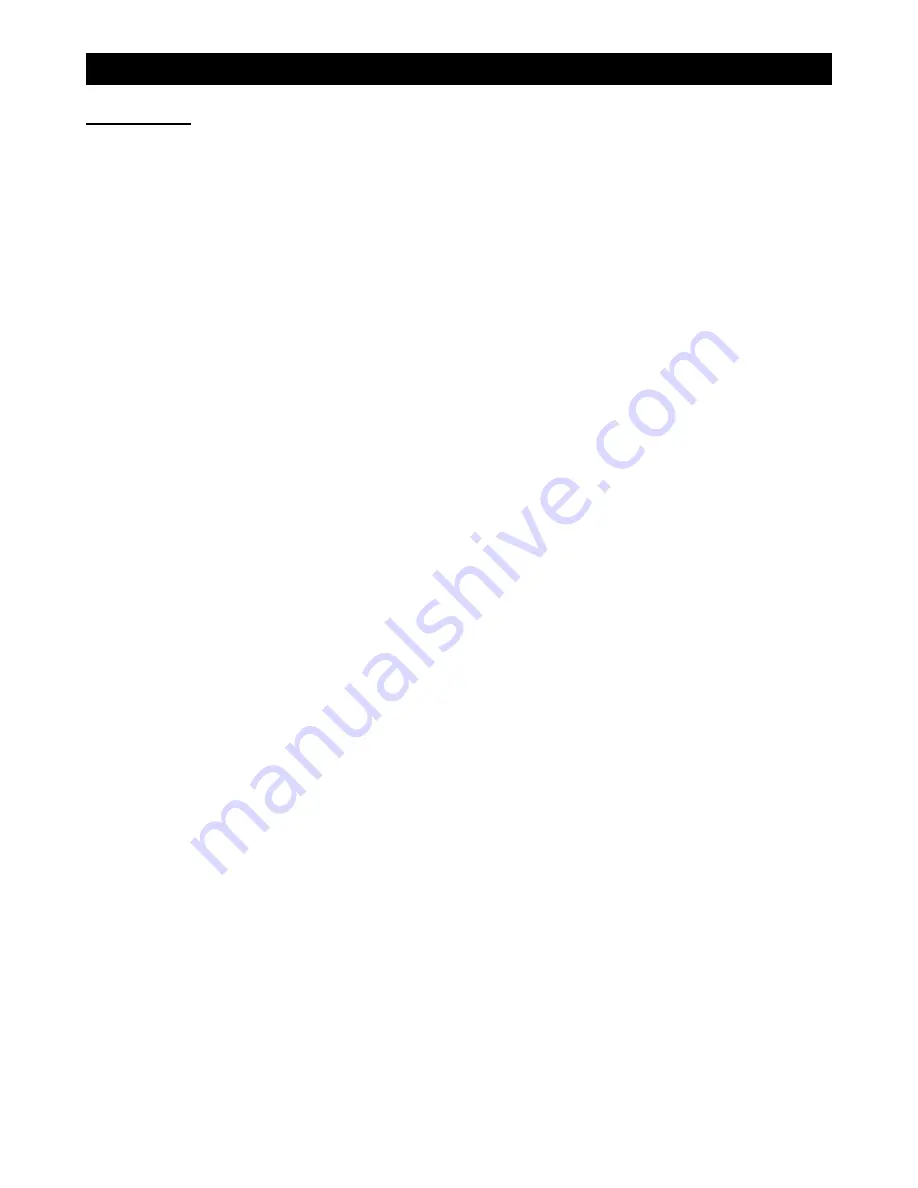
INTRODUCTION
Introduction
Welcome to the Diamond Products family and thank you for choosing Diamond Products equipment.
At Diamond Products we are driven to ensure you are completely satisfied with your product and
continually strive to improve our product line so that we can offer you the best possible equipment in
the industry.
This operator’s manual is a critical document that provides pertinent information regarding the safety,
operation, maintenance, and care of your new equipment. Keep this manual available at all times.
Operate the equipment and all of its components according to this manual. Failure to comply with and
understand the following safety, operation and maintenance instructions can result in serious injuries
and/or death. All operators must be properly trained or supervised by experienced personnel prior to
using this floor grinder and should understand the risks and hazards involved. Diamond Products
discourages improper or unintended equipment usage and cannot be held liable for any resulting
damages.
Equipment modifications should be made by Diamond Products to ensure safety and design. Any
modifications made by the owner(s) are not the responsibility of Diamond Products and void all
equipment warranties if a problem arises as a result of the modification.
Refer to the Diamond Products Parts List for additional information and part diagrams. Refer to the
motor/engine manufacturer as the primary source for all safety, operations, and maintenance
instructions regarding the motor/engine. Prior to operating, record the floor grinder’s serial number,
and the motor/engine model and serial numbers in Appendix D.
5