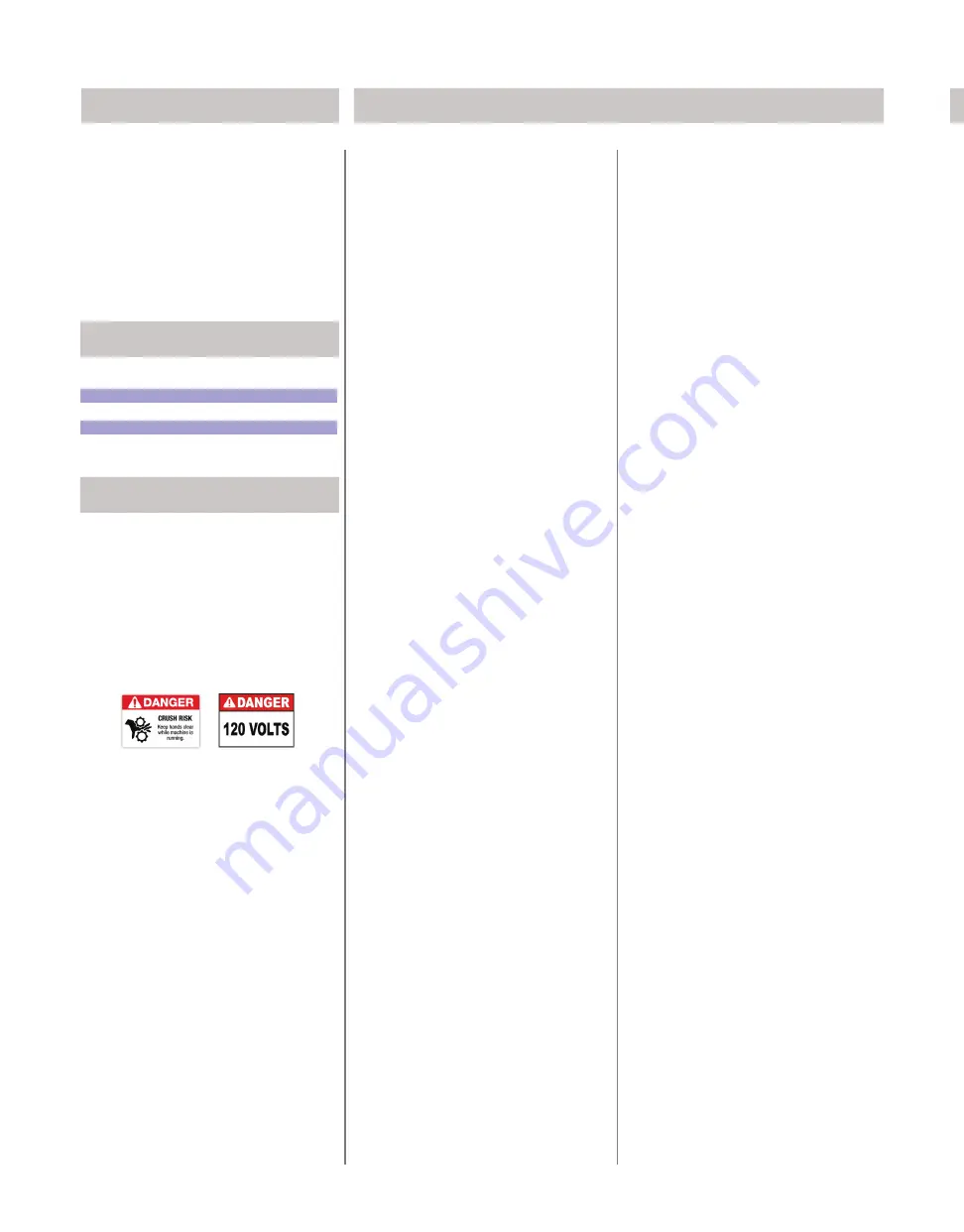
INTRODUCTION
This manual outlines the maintenance and
operation of the Dual Component Polymer
Pump.
This is a professional tool and is intended
for use by trained and experienced opera-
tors.
To get maximum benefi t from your tool and
to ensure maximum safety, be sure to read
this manualthoroughly. You should also
periodically review safety instructions.
Operators and maintenance personnel
must always comply with the following
safety precautions. These precautions are
given here for your safety. Review them
carefully before operating the tool and
before performing general maintenance
repairs on the tool. Supervising personnel
should develop additional precautions
relating to the specifi c work area and local
safety regulations.
SAFETY PRECAUTIONS
• Read, understand, and follow all safety,
transportation, and storage recom-
mendations on the Material Safety and
Data Sheets of the material that will be
dispensed.
• Keep hands, fi ngers, and clothing free
from all moving parts including gears,
chains, and other moving parts while
operating the pump.
• Never run the pump without the gear/
chain guard in place.
• Disconnect power supply before servicing
the gear/chain or changing gears.
• Disconnect power supply before opening
or servicing the electrical components.
• Make sure there is adequate ventilation if
a gas powered generator is being used
to supply power.
• Secure the pump before transporting.
• Always use the same tanks (A or B) for
the same material to minimize risk of ma-
terial hardening inside of the tank, pump,
hoses, and other parts.
Key Elements:
1. Clean tanks, pumps, lines, and manifold
2. No cross contamination
3. Proper mixing ratio = proper material
cure
Prior to use:
1. Inspect tanks for evidence of loose parti-
cles or debris.
2. Inspect manifold (located at the end of
the dispensing wand where both hoses
attach. The static mixing element attach-
es to the manifold with a 7/8” static mixer
nut) - Inspection should be performed at
the start of each day’s work and consists
of the following:
a. Remove hoses connected to manifold
and remove 90 degree fi tting.
b. Inspect for and remove any debris or
contamination that might clog the exit
hole. A 1/4” drill bit can generally be used
to clean the exit hole.
c. Reconnect lines to manifold.
3. If hydraulic fl uid remains in the tank
(used for fl ushing and pump storage and
should be left at least a couple inches
deep in the tanks when not in use) plug
in power supply and trigger applicator
gun to dispense fl uid.
a. Watch fl uid fl ow out of manifold and
inspect for clog or uneven fl ow.
b. Using graduated measuring cups, dis-
pense fl uid into containers to check for
proper ratio.
4. After confi rming ratio is correct and that
no contamination remains in the lines
or in the manifold, dispense remaining
hydraulic fl uid to empty the tanks.
5. The unit is now ready for use.
Dispensing Filler:
1. Prior to fi ling tanks, premix the Part A
Polyol (gray component).
2. Ensure that Part A material is placed in
Part A tank and Part B material is placed
in Part B tank. DO NOT CROSS CON-
TAMINATE. It is advised to keep the lid
on the tank that is not being fi lled.
3. After fi lling tanks, dispense polyurea
through manifold assembly watching
fl ow. An errant stream out of one or
both sides of the manifold will generally
indicate that there is a restriction in the
manifold and disassembly and cleaning
should be performed.
4. If fl ow is even and equal, attach static
mixing tip to end of manifold.
5. Dispense a small amount of material
through the tip into waste container to
ensure thorough mixing in the tip. Then
dispense small amount of material onto
cardboard or other disposable sheet
to monitor cure. Allow to set for 10-15
minutes or until signifi cant cure has been
achieved prior to commencing. This will
ensure proper ratio and cure of future
material.
6. While waiting on test material to cure,
remove static mixing tip and discard.
7. Pump grease (white lithium supplied with
pump) into fi ttings on manifold to prevent
cross contamination.
8. Upon confi rmation of test sample cure,
install new static mixing tip.
9. Install fi ller into joint of crack per product
installation guidelines.
Work Interruption:
1. If work is stopped for short term (5 min-
utes or so, to move pump, etc.) periodi-
cally trigger applicator wand to dispense
material every 30-45 seconds to ensure
material in static mixing tip does not set.
2. If dispensing is stopped for longer term
(lunch break, etc.) remove static mixing
tip and discard. Pump Grease into fi ttings
on the manifold as described above.
Upon commencement, re-install a new
static mixing tip.
End of Day:
1. If possible, stop material placement
when tanks are “nearly” empty (material
is down to within a couple of inches of
the tank bottom). DO NOT RUN tanks
dry of polyurea or improper ratio and
cure may result if one tank empties
slightly ahead of the other.
2. In case material is run to the bottom of
the tank, remove static mixing tip and
dispense remaining material into a waste
container until tanks are empty and line
sputters at the static tip.
a. Fill both tanks with hydraulic fl uid to ap-
proximately 3 inches from the bottom.
b. Dispense hydraulic fl uid to purge the
pumps and lines. Ensure some fl uid
remains in the tanks once complete.
c. Grease the fi ttings on the manifold and
secure for next use.
3. In case several inches of polyurea
remains in the tank at day’s end AND,
pump will be used to place additional
joint fi ller the following day, it can be pos-
sible to leave the material in the machine
overnight using the following procedure.
NOTE: Do not leave polyurea in the
tanks or within the system (tanks, pumps,
lines, manifold) if material placement will
not be performed the following day.
SET-UP AND OPERATION
SPECIFICATIONS
SAFETY
Part No. DP-PUMP10GAL
Capacity:
2-6.5 Gallon Tanks
Electrical Requirements:
120V
Motor:
1/2 HP
Weight:
220 lbs
SET-UP (cont.)