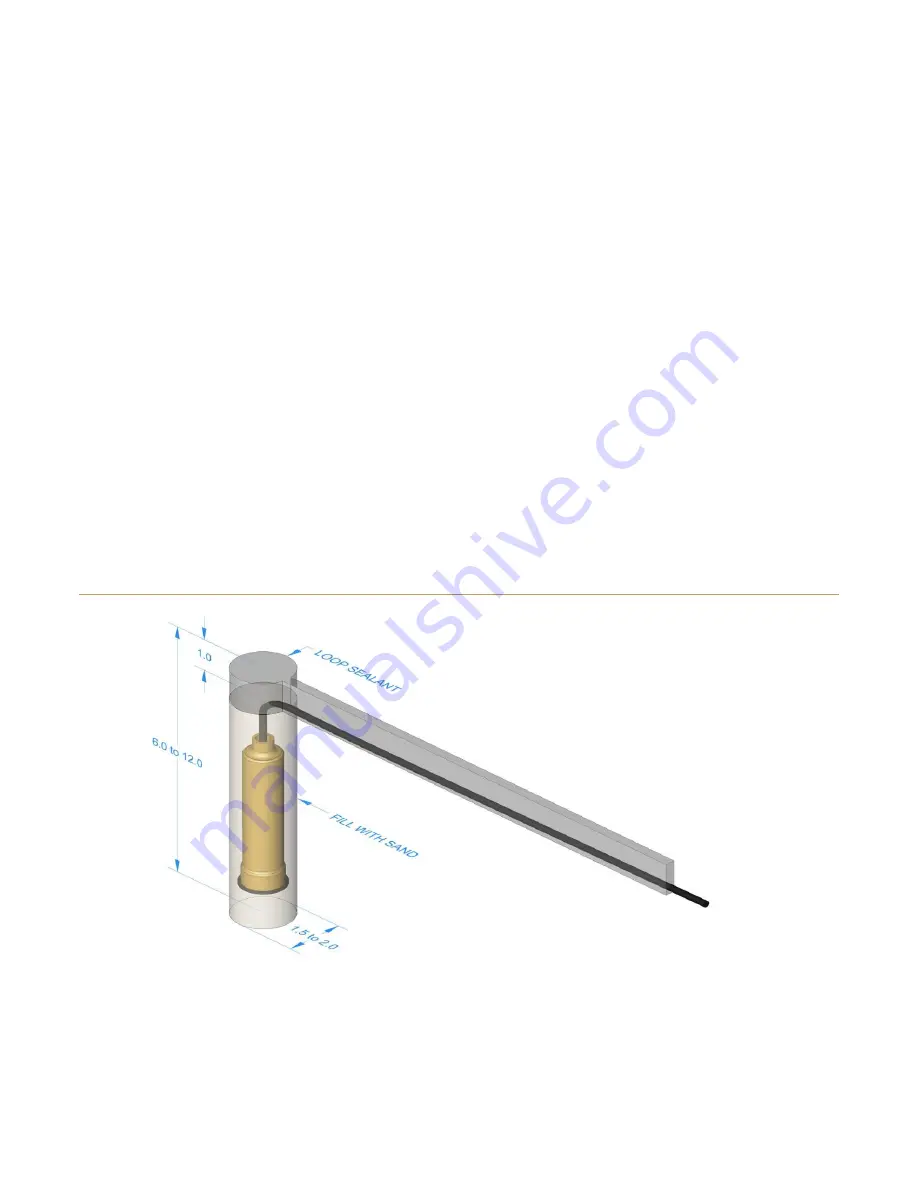
DSP-22-1 User Manual
Page 17 of 22
DSP-22-1_MAN_D
The loop wire should be installed as a continuous piece of wire from the detector to the loop, all of the turns in
the loop, and back to the detector. Remember to make allowance for shrinkage in the wire length when the
portion of the wire not in the roadway surface is twisted. The twisting is important for dealing with electrical
noise. A splice of the loop wire should never be made in the roadway. If the loop wire needs to be spliced to
another cable to get to the detector, the splice should be done in a junction box and the connections should be
soldered and weatherproofed. Wire nuts should never be used at any point in the loop circuit.
In order to keep the loop wire at the bottom of the saw slot, 1” to 2” pieces of backer rod should be placed in th
e
saw slot every 1 to 2 feet. The backer rod should be sized such that it fits snugly in the saw slot. Use a blunt object
(not a screwdriver) to press the backer rod pieces down into the saw slot as far as they will go. Keeping the loop
wire at the bottom of the saw slot allows the loop sealant to provide the maximum amount of protection possible
from foreign object penetration. Never use a continuous piece of backer rod over the loop, as this would prevent
the loop sealant from encapsulating the loop wire.
The loop sealant used should be appropriate for the roadway surface that was cut. Generally, epoxy or polyester
based sealants are used for concrete surfaces and polyester or polyurethane based sealants are used for asphalt
surfaces. However, these are not hard guidelines and specific circumstances will determine which type of sealant
should be used.
Once the loop wire leaves the saw slot it should be twisted at least three times per foot. More is better. The
twists should be kept tight to be most effective in reducing the effects of electrical interference.
Free-exit probe Installation
Figure 5 Typical Free-exit probe Installation