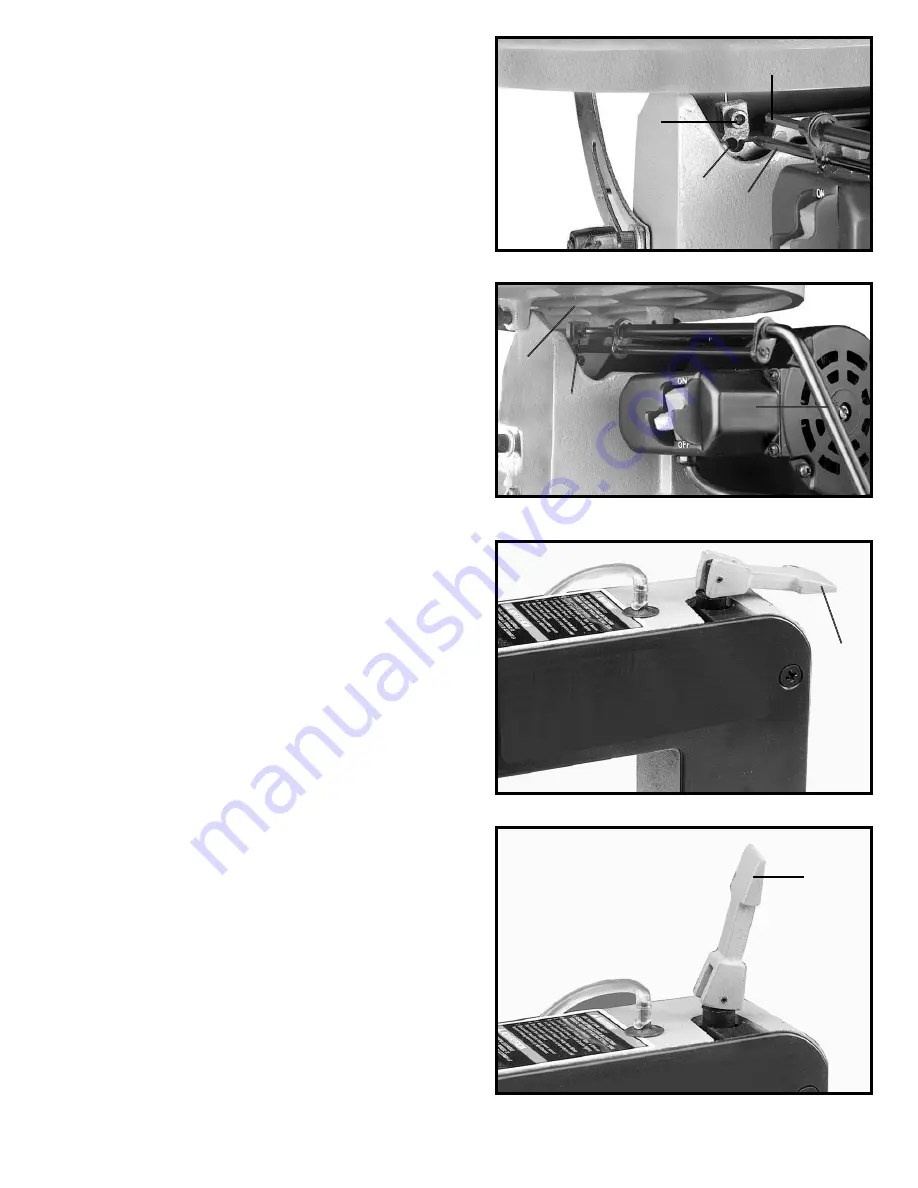
9
6.
Insert long end (A) Fig. 16, of quickset blade
changing wrench into hole (G) in lower blade holder. This
will help align wrench (C) with blade holder screw (H).
7.
Turn wrench (E) Fig. 17, counterclockwise to loosen
screw (H) and remove blade (F) from lower blade holder.
8.
Insert new blade into the lower and upper blade
holders in the same manner, making certain the blade
teeth are pointing down toward the table. Tighten screws
in both the upper and lower blade holders. Replace table
insert.
9.
Apply blade tension by referring to the section
“ADJUSTING BLADE TENSION”.
H
G
A
C
Fig. 16
Fig. 17
F
H
E
ADJUSTING
BLADE TENSION
Tension is applied to the blade when the blade tension
lever (A) Fig. 18, has been adjusted and is in the
horizontal position as shown. When the blade tension
lever (A) is moved to the vertical position, as shown in
Fig. 19, blade tension is released.
To adjust blade tension, position lever (A) in the vertical
position, as shown in Fig. 19. To increase tension, turn
lever (A) clockwise and to decrease tension turn lever (A)
counterclockwise. When adjusting tension, turn lever
one-quarter of a turn at a time.
NOTE:
It is necessary to
adjust the blade tension only when the blade is removed
from both the upper and lower blade holders and a new
or different type of blade is assembled to the holders. It
is not necessary to adjust blade tension when the blade
is removed and replaced in only the upper blade holder
as in performing inside cutting operations. After desired
tension is obtained, position tension lever (A) in the
horizontal position, as shown in Fig. 18.
Adjusting the blade for proper tension is usually
accomplished by trial and error. One method is to pull
back on the blade tension lever (A) Fig. 19, the blade
should start to have tension (resistance) when the blade
tension lever is half way between open Fig. 19, and
closed Fig. 18. Finer blades require more tensioning
while thicker blades require less tension.
A
Fig. 18
Fig. 19
A