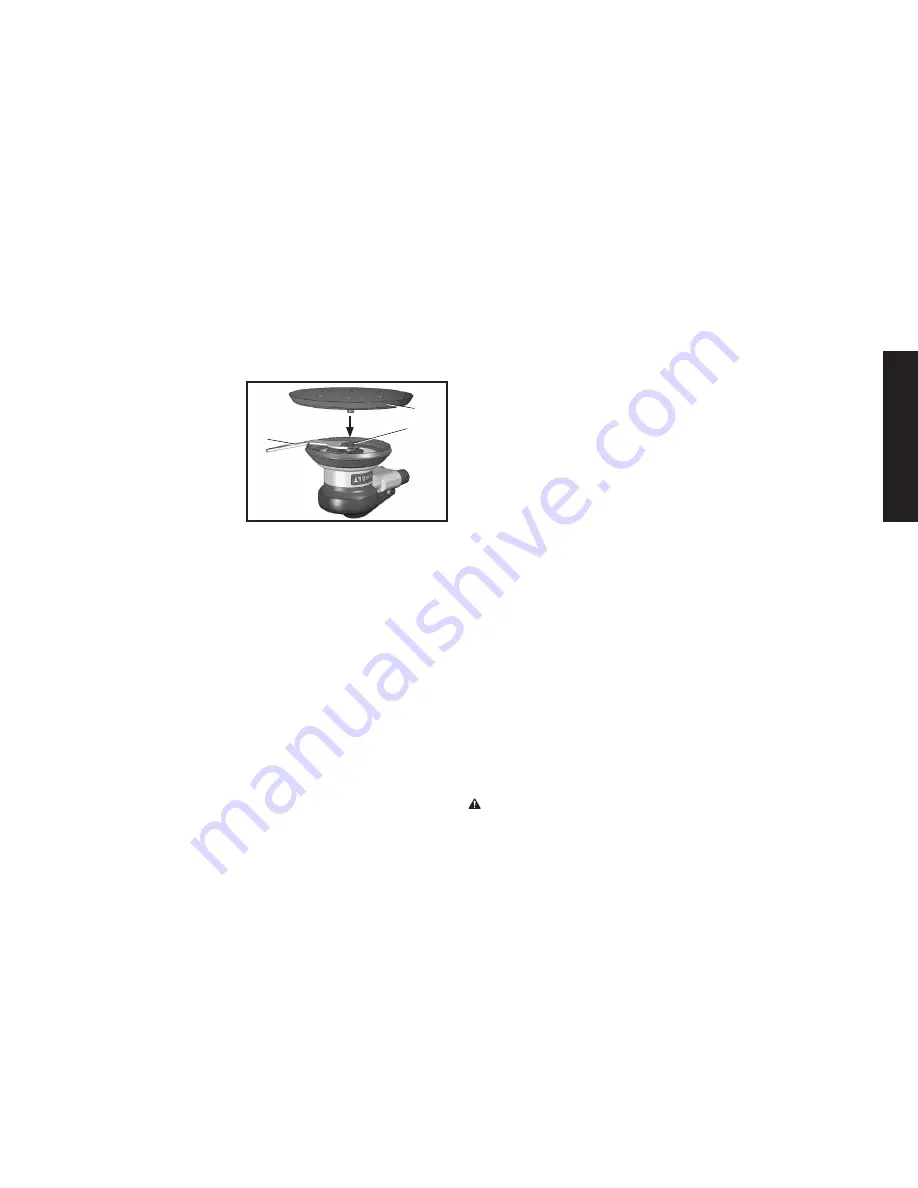
13
English
SANDER PAD ASSEMBLY CONTINUED
• To assemble the
sanding
pad (B), place the supplied
wrench onto the
balance
shaft nut (H).
• Hold the wrench firmly and
insert the threaded post on
the
sander pad (B) into the
balance shaft nut (H).
Tighten by turning the
sander pad (B) clockwise.
OPERATING PROCEDURES
START-UP (FIG. 1, PG. 2)
• Turn on the air compressor and allow the air tank to be filled.
• Set the air compressor regulator to 90 PSI. This air
tool operates at a maximum of 90 PSI air pressure.
• Depress the trigger to start operating the tool.
SHUT-DOWN (FIG. 1, PG. 2)
• Release the trigger to stop the tool.
• Always disconnect air supply when changing sandpaper pads.
• When job is completed, turn off the air compressor and store
the air tool after lubrication.
Tips
• Begin sanding with an abrasive grit sandpaper coarse
enough to remove the high spots. Progress to a finer grit
sandpaper until the desired finish is obtained.
• Never change from coarse grit sandpaper to a very fine grit
sandpaper, always progress gradually to the finer grit.
OPERATING INSTRUCTIONS
• Select a suitable abrasive disc and make sure that it is fixed
securely to the tool.
• Connect to suitable air supply as recommended.
• Apply the sander lightly to the work and allow the abrasive
disc to cut. Take great care when sanding around sharp
edges and surfaces to avoid the disc snagging i.e. the disc
may be brought to an abrupt stop or considerably slowed,
causing the tool to kick in the hands.
NOTE: Use of safety glasses and a breathing mask is
recommended. Sanding certain materials may create
hazardous dust which may require special breathing
equipment. Check before using the tool. Although the tool has
a low noise level, the actual sanding process may cause a
noise level such that ear protectors will be required. Safety
gloves are recommended.
Do not continue to use abrasive discs that are worn or clogged.
Do not use undersized or oversized sanding discs. The disc
should be no more than 1/4” larger in diameter than the pad,
and not smaller than the pad.
MAINTENANCE
Lubrication
Air tools require lubrication throughout the lifetime of the tools.
The air motor and bearing uses compressed air to power the tool.
The compressed air contains moisture that will rust the air motor
and other parts in side of the tools, therefore lubrication is required
daily. Failure to lubricate the air tool properly will dramatically
shorten the life of the tool and will void the warranty
CAUTION: This air tool requires lubrication BEFORE initial use,
also before and after each additional use.
WRENCH
B
H