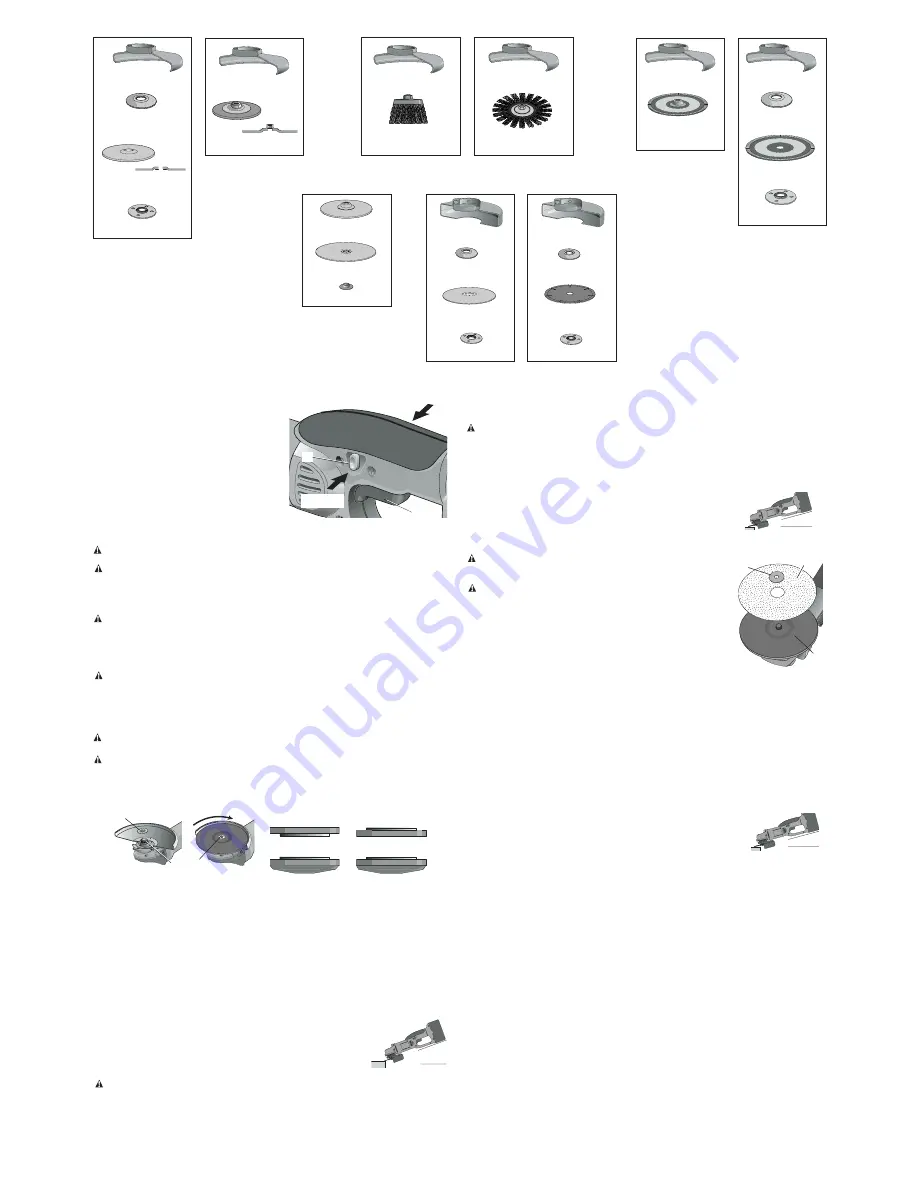
OPERATION
Switch (Fig. 4)
LOCK-OFF BUTTON AND TRIGGER SWITCH
Your cut-off tool is equipped with a lock-off button (B).
To lock the trigger switch,
press the lock-off button as shown
in Figure 3. When the lock-off button is depressed to the lock
icon, the unit is locked.
Always lock the trigger switch when carrying or storing the tool
to eliminate unintentional starting.
To unlock the trigger switch,
press the lock-off button. When
the lock-off button is depressed to the unlock icon, the unit is
unlocked. The lock-off button is colored red to indicate when
the switch is in its unlocked position.
Pull the trigger switch (A) to turn the motor ON. Releasing the
trigger switch turns the motor OFF.
NOTE:
This tool has no provision to lock the switch in the ON position, and should never be locked ON by any other
means.
CAUTION:
Hold the side handle and body of the tool firmly to maintain control of the tool at start up and during use and
until the wheel or accessory stops rotating. Make sure the wheel has come to a complete stop before laying the tool down.
CAUTION:
Allow the tool to reach full speed before touching tool to the work surface. Lift the tool from the work sur-
face before turning the tool off.
SPINDLE LOCK
The spindle lock pin is provided to prevent the spindle from rotating when installing or removing wheels. Operate the
spindle lock pin only when the tool is turned off, the battery is removed, and the wheel has come to a complete stop.
CAUTION:
Do not engage the spindle lock while the tool is operating. Damage to the tool will result and attached acces-
sory may spin off possibly resulting in injury.
To engage the lock,
depress the spindle lock button and rotate the spindle until you are unable to rotate the spindle further.
Mounting and Using Depressed Center Grinding Wheels and Sanding Flap Discs
MOUNTING AND REMOVING HUBBED WHEELS
CAUTION:
Turn off tool and remove battery before making any adjustments or removing or installing attachments or
accessories.
Hubbed wheels install directly on the 14mm x 2 (5/8"-11) threaded spindle.
1. Thread the wheel on the spindle by hand.
2. Depress the spindle lock button and use a wrench to tighten the hub of the wheel.
3. Reverse the above procedure to remove the wheel.
CAUTION:
Failure to properly seat the wheel before turning the tool on may result in damage to the tool or the wheel.
MOUNTING NON-HUBBED WHEELS
CAUTION:
Turn off tool and remove battery before making any adjustments or removing or installing attachments or
accessories.
Depressed center Type 27 grinding wheels must be used with included flanges. See 2 of this manual for more infor-
mation.
1. Install the unthreaded backing flange (G) on spindle (D) with the raised section (pilot) against the wheel.
2. Place wheel against the backing flange, centering the wheel on the raised section (pilot) of the backing flange.
3. While depressing the spindle lock button, thread the clamp nut (H) on spindle. If the wheel you are installing is more
than 3.31mm (1/8") thick, place the threaded clamp nut on the spindle so that the raised section (pilot) fits into the
center of the wheel. If the wheel you are installing is 3.31mm (1/8") thick or less, place the threaded clamp nut on
the spindle so that the raised section (pilot) is not against the wheel.
4. While depressing the spindle lock button, tighten the clamp nut with a wrench.
5. To remove the wheel, depress the spindle lock button and loosen the threaded clamp nut with a wrench.
NOTE:
If the wheel spins after the clamp nut is tightened, check the orientation of the threaded clamp nut. If a thin wheel is
installed with the pilot on the clamp nut against the wheel, it will spin because the height of the pilot prevents the clamp nut
from holding the wheel.
Surface Grinding with Grinding Wheels
1. Allow the tool to reach full speed before touching the tool to the work surface.
2. Apply minimum pressure to the work surface, allowing the tool to operate at high speed. Grinding rate is greatest
when the tool operates at high speed.
3. Maintain a 20˚ to 30˚ angle between the tool and work surface.
4. Continuously move the tool in a forward and back motion to avoid creating gouges in the
work surface.
5. Remove the tool from work surface before turning tool off. Allow the tool to stop rotating
before laying it down.
Edge Grinding with Grinding Wheels
CAUTION:
Wheels used for cutting and edge grinding may break or kick back if they bend or twist while the tool is
being used to do cut-off work or deep grinding. To reduce the risk of serious injury, limit the use of these wheels with a
standard Type 27 guard to shallow cutting and notching [less than 12.7mm (1/2") in depth]. The open side of the guard
must be positioned away from the operator. For deeper cutting with a Type 1 cut-off wheel, use a closed Type 1 guard.
See page 3 for more information.
1. Allow the tool to reach full speed before touching the tool to the work surface.
2. Apply minimum pressure to the work surface, allowing the tool to operate at high speed. Grinding rate is greatest
when the tool operates at high speed.
3. Position yourself so that the open-underside of the wheel is facing away from you.
20˚-30˚
3.31mm (1/8") wheels
Backing Flange
Clamp Nut
6.35MM (1/4") WHEELS
Backing Flange
Clamp Nut
H
G
D
FIG. 4
LOCKED
UNLOCKED
B
A
4. Once a cut is begun and a notch is established in the workpiece, do not change the angle of the cut. Changing the
angle will cause the wheel to bend and may cause wheel breakage. Edge grinding wheels are not designed to with-
stand side pressures caused by bending.
5. Remove the tool from the work surface before turning the tool off. Allow the tool to stop rotating before laying it
down.
WARNING:
Do not use edge grinding/cutting wheels for surface grinding applications because these wheels are not
designed for side pressures encountered with surface grinding. Wheel breakage and injury may result.
Surface Finishing with Sanding Flap Discs
1. Allow the tool to reach full speed before touching the tool to the work surface.
2. Apply minimum pressure to work surface, allowing the tool to operate at high speed. Sanding rate is greatest when
the tool operates at high speed.
3. Maintain a 5˚ to 10˚ angle between the tool and work surface.
4. Continuously move the tool in a forward and back motion to avoid creating gouges in
the work surface.
5. Remove the tool from work surface before turning tool off. Allow the tool to stop rotating
before laying it down.
Mounting Sanding Backing Pads
CAUTION:
Turn off tool and remove battery before making any adjustments or
removing or installing attachments or accessories.
NOTE: Guard may be removed when using sanding backing pads
CAUTION:
Proper guard must be reinstalled for grinding wheel, sanding flap disc, wire
brush or wire wheel applications after sanding applications are complete.
1. Place or appropriately thread backing pad (N) on the spindle.
2. Place the sanding disc (O) on the backing pad (N).
3. While depressing spindle lock, thread clamp nut (P) on spindle, piloting the raised
hub on the clamp nut into the center of sanding disc and backing pad.
4. Tighten the clamp nut by hand. Then depress the spindle lock button while turning
the sanding disc until the sanding disc and clamp nut are snug.
5. To remove the wheel, grasp and turn the backing pad and sanding pad while
depressing the spindle lock button.
Using Sanding Backing pads
Choose the proper grit sanding discs for your application. Sanding discs are available in various grits. Coarse grits yield
faster material removal rates and a rougher finish. Finer grits yield slower material removal and a smoother finish.
Begin with coarse grit discs for fast, rough material removal. Move to a medium grit paper and finish with a fine grit
disc for optimal finish.
Coarse ......................16 - 30 grit
Medium ....................36 - 80 grit
Fine Finishing ............100 - 120 grit
Very Fine Finishing ....150 - 180 grit
1. Allow the tool to reach full speed before touching tool to the work surface.
2. Apply minimum pressure to work surface, allowing the tool to operate at high speed. Sanding rate is greatest when
the tool operates at high speed.
3. Maintain a 5˚ to 15˚ angle between the tool and work surface. The sanding disc should
contact approximately one inch of work surface.
4. Move the tool constantly in a straight line to prevent burning and swirling of work surface.
Allowing the tool to rest on the work surface without moving, or moving the tool in a cir-
cular motion causes burning and swirling marks on the work surface.
5. Remove the tool from work surface before turning tool off. Allow the tool to stop rotating before laying it down.
Precautions To Take When Sanding Paint
1. Sanding of lead based paint is NOT RECOMMENDED due to the difficulty of controlling the contaminated dust. The
greatest danger of lead poisoning is to children and pregnant women.
2. Since it is difficult to identify whether or not a paint contains lead without a chemical analysis, we recommend the fol-
lowing precautions when sanding any paint:
PERSONAL SAFETY
1. No children or pregnant women should enter the work area where the paint sanding is being done until all clean up
is completed.
2. A dust mask or respirator should be worn by all persons entering the work area. The filter should be replaced daily or
whenever the wearer has difficulty breathing.
NOTE:
Only those dust masks suitable for working with lead paint dust and fumes should be used. Ordinary paint-
ing masks do not offer this protection. See your local hardware dealer for the proper N.I.O.S.H. approved mask.
3. NO EATING, DRINKING or SMOKING should be done in the work area to prevent ingesting contaminated paint parti-
cles. Workers should wash and clean up BEFORE eating, drinking or smoking. Articles of food, drink, or smoking
should not be left in the work area where dust would settle on them.
ENVIRONMENTAL SAFETY
1. Paint should be removed in such a manner as to minimize the amount of dust generated.
2. Areas where paint removal is occurring should be sealed with plastic sheeting of 4 mils thickness.
3. Sanding should be done in a manner to reduce tracking of paint dust outside the work area.
CLEANING AND DISPOSAL
1. All surfaces in the work area should be vacuumed and thoroughly cleaned daily for the duration of the sanding pro-
ject. Vacuum filter bags should be changed frequently.
2. Plastic drop cloths should be gathered up and disposed of along with any dust chips or other removal debris. They
should be placed in sealed refuse receptacles and disposed of through regular trash pick-up procedures.
During clean up, children and pregnant women should be kept away from the immediate work area.
3. All toys, washable furniture and utensils used by children should be washed thoroughly before being used again.
Mounting and Using Wire Brushes and Wire Wheels
Wire cup brushes or wire wheels screw directly on the grinder spindle without the use of flanges. Use only wire
brushes or wheels provided with a 14mm x 2 (5/8" -11) threaded hub. A Type 27 guard is required when using wire
brushes and wheels.
5˚-15˚
P
N
O
5˚-10˚
Type 27 guard
115mm (4 1/2") GRINDING WHEELS
unthreaded backing
flange
threaded clamp nut
Type 27 hubbed wheel
Type 27 guard
Type 27 depressed center
wheel
WIRE WHEELS
75mm (3")
wire cup brush
100mm (4")
wire wheel
Type 27 guard
Type 27 guard
115mm (4-1/2") SANDING FLAP DISCS
hubbed sanding flap
disc
unthreaded backing
flange
non-hubbed sanding flap
disc
threaded clamp nut
rubber backing pad
sanding disc
threaded clamp nut
SANDING DISCS
115mm (4-1/2") CUTTING WHEELS
Type 1 guard
backing flange
abrasive cutting wheel
clamp nut
Type 1 guard
backing flange
diamond cutting wheel
clamp nut
Type 27 guard
Type 27 guard