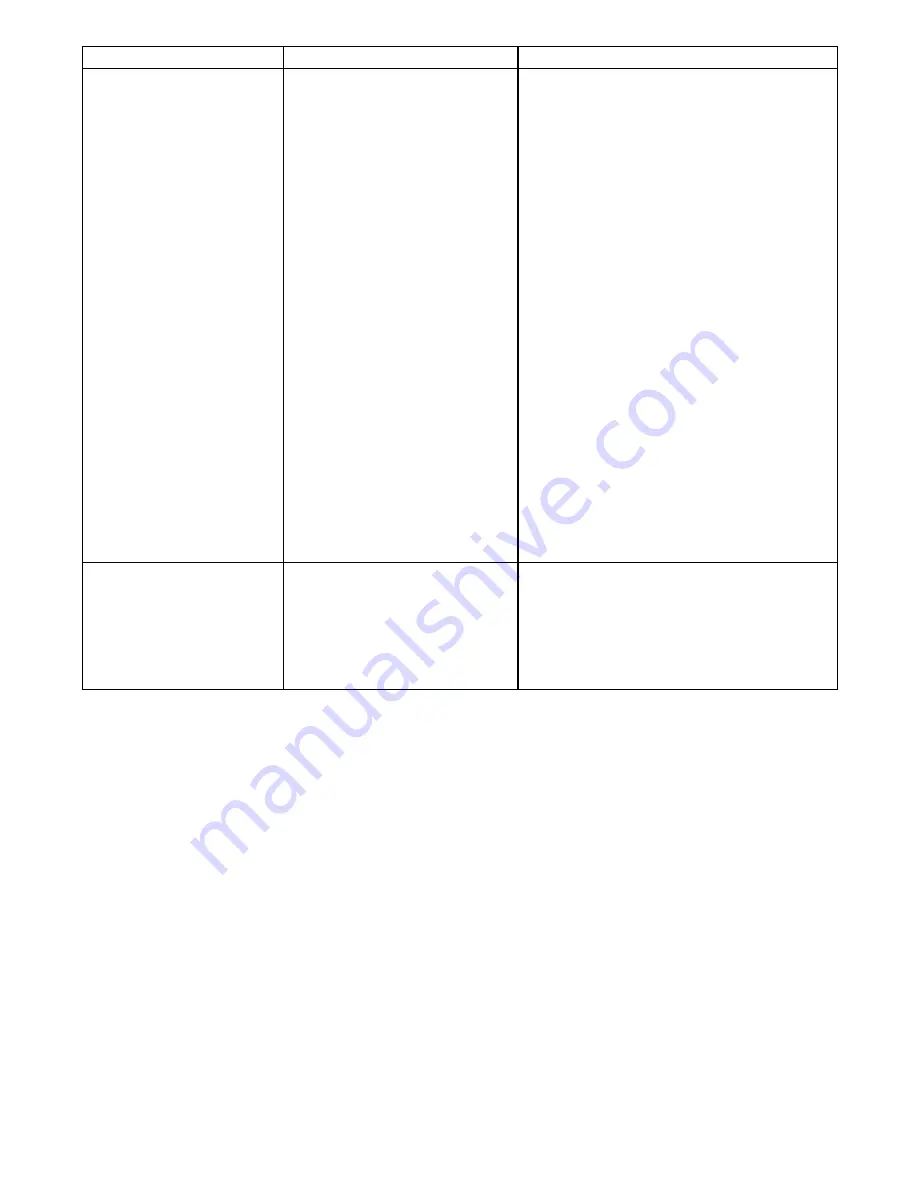
13 — ENG
PROBLEM
CAUSE
CORRECTION
Motor overload protection switch has
tripped.
Tank pressure exceeds pressure switch
“cut-in” pressure.
Wrong gauge wire or length of exten-
sion cord.
Check valve stuck open.
Loose electrical connections.
Possible defective motor or capacitor.
Paint spray on internal motor parts.
Fuse blown, circuit breaker tripped.
Pressure release valve on pressure
switch has not unloaded head pres-
sure.
Damaged regulator.
Let motor cool off and overload switch will automati-
cally reset.
Motor will start automatically when tank pressure
drops below “cut-in” pressure of pressure switch.
Check for proper gauge wire and cord length.
Remove and clean, or replace.
Check wiring connection inside pressure switch and
terminal box area.
Contact an Authorized Warranty Service Center for
inspection or replacement, if necessary.
Have checked by an Authorized Warranty Service
Center. Do not operate the compressor in the paint
spray area. See flammable vapor warning.
1.
Check fuse box for blown fuse and replace, if
necessary. Reset circuit breaker. Do not use a
fuse or circuit breaker with higher rating than that
specified for your particular branch circuit.
2.
Check for proper fuse; only “Fusetron” type T
fuses are acceptable.
3.
Check for low voltage conditions and/or proper
extension cord.
4.
Disconnect the other electrical appliances from
circuit or operate the compressor on its own
branch circuit.
Bleed the line by pushing the lever on the pressure
switch to the “off” position; if the valve does not open,
replace it.
Replace regulator.
Motor will not run or restart.
Regulator knob has continuous
air leak. Regulator will not shut
off air outlet.