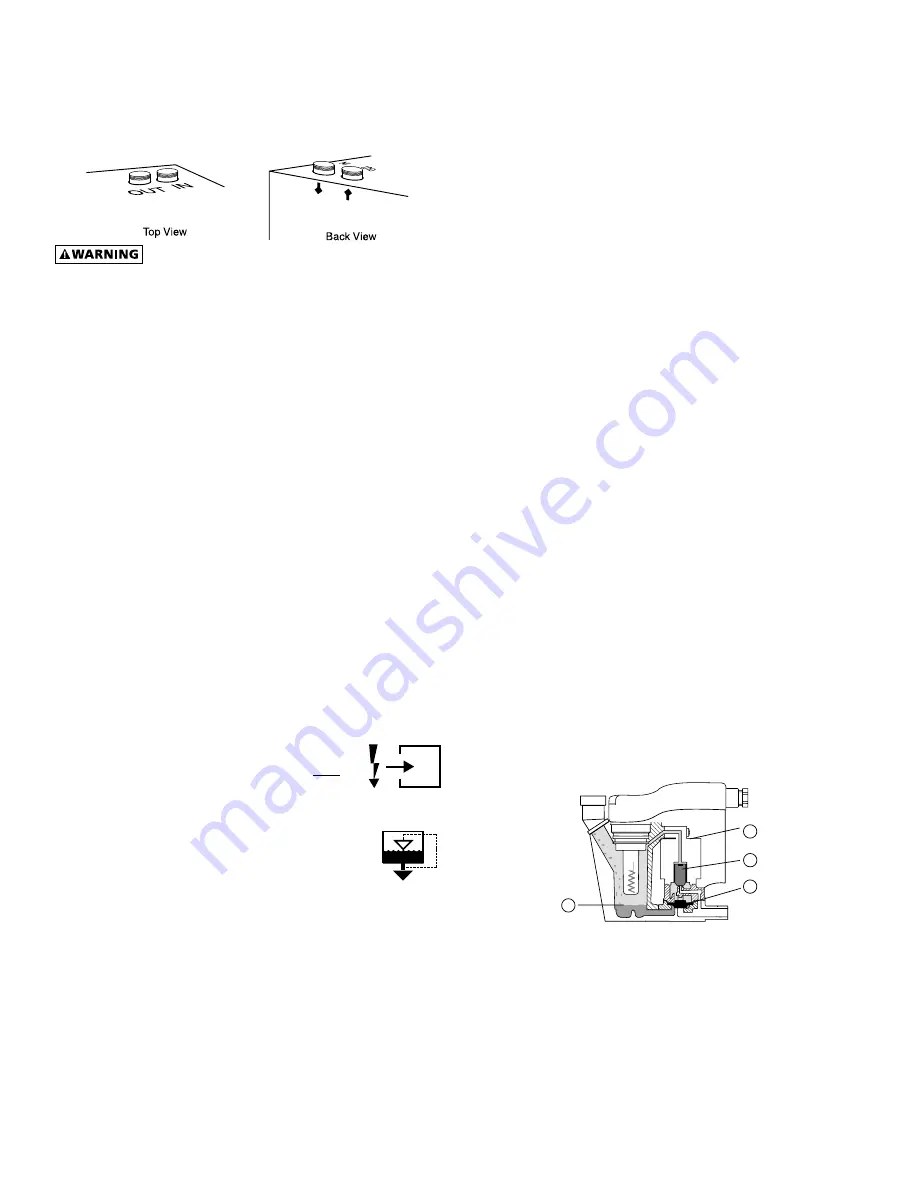
4
1.6 Electronic Demand Drain
Installation
1.
Remove Service Panel by removing two shipping
screws and turning (2) Quick Release Locks.
2.
Reach inside and remove screws on Separator/filter
shipping support bracket and remove bracket.
3.
Reach behind filter and cut plastic shipping strap
holding Energy Saving Demand Drain.
4.
Insert Demand Drain into brass quick disconnect on
bottom of Separator/filter.
5.
Remove manual petcock from drain hose and mount
into manual outlet drain connection on outside of side
panel.
Operation
A. Verify that isolation valves are open. If the drain fails to
discharge after the valve is energized, the electronic
control circuit will repeatedly energize the valve in an
attempt to clear the discharge port. If, after 60 sec-
onds, the drain still fails to discharge, the control circuit
then switches to the alarm mode. In this mode the
valve is de-energized and the red alarm light is activated
on the drain and the dryer controller. The valve is then
automatically energized every 4 minutes for 5 seconds.
Check the drain operation. Push drain (push-to-test)
button on the emm Energy Management Monitor
control board to energize drain. A flow of condensate
and/or air should be present at the drain outlet. The
alarm mode automatically clears after the drain returns
to normal operation.
B. Condensate enters the reservoir
(1)
through the inlet
port. When the condensate level in the reservoir covers
the capacitance sensor, an electronic signal is sent to
the solid state countdown processor. The processor
delays the opening of the solenoid valve for a given
period of time. Once the time has elapsed, the solid
state processor transmits information to energize the
coil in the solenoid valve
(2)
.The magnetic force of the
coil causes the solenoid core
(3)
to move, closing the
pilot air supply line and opening the pilot air exhaust
line. After the pilot air above the diaphragm
(4)
is
vented, pressure in the reservoir opens the discharge
port and forces the condensate through the discharge
port and outlet piping.
1.2 Mounting
Mount on floor or shelf free from vibration.
1.3 Piping connections
A.
Air Inlet—Connect compressed air line from air
source to air inlet.
Refer to Serial Number Tag for maximum
working pressure. Do not exceed dryer’s Maximum
Working Pressure.
NOTE: Install dryer in air system at highest pressure
possible (e.g. before pressure reducing valves).
NOTE: Install dryer at coolest compressed air temperature
possible. Maximum inlet compressed air temperature:
120
°
F (49
°
C). If inlet air exceeds this temperature, precool
the air with an aftercooler.
B.
Air Outlet—Connect air outlet to downstream air lines.
C.
By-pass piping—If servicing the dryer without
interrupting the air supply is desired, piping should
include inlet and outlet valves and an air by-pass valve.
D.
Water cooled models—cooling water inlet and outlet
1.
Connect cooling water supply to cooling
water inlet.
2.
Connect cooling water return line to cooling
water outlet connection.
NOTE: Strainer and water regulating valve are supplied on
water cooled models.
1.4 Electrical connections
IMPORTANT: Use copper supply wires only.
A.
Dryer is designed to operate on the voltage, phase,
and frequency listed on the serial number tag.
B.
Connect power source to terminal strip in electrical
enclosure.
NOTE: Refrigeration condensing unit is de-
signed to run continuously and should NOT be
wired to cycle on/off with the air compressor.
1.5 Moisture separator
A.
An automatic electric demand drain (EDD)
discharges condensate removed by the
separator. It may be desirable to pipe the
condensate from the EDD outlet to a
suitable drain.
B.
For manual draining, convenient dryer depressuriza-
tion, and EDD service, a three-way valve at the bottom
of the moisture separator and before the EDD is
installed. For manual draining, turn the valve handle
so it is in a horizontal position. Open the petcock on
the side of the dryer base pan to discharge the
condensate or to depressurize the dryer if it has been
by-passed. The petcock can be left in a throttled
(partially opened) position should there be a problem
with EDD.
NOTE: Discharge is at system pressure. Drain line should
be anchored.
NOTE: Condensate may contain oil. Comply with applicable
laws concerning proper disposal.
2.0 OPERATION
2.1 Minimum/Maximum operating conditions
A.
Maximum inlet air pressure: refer to dryer serial
number tag
B.
Minimum inlet air pressure: 30 psig (2.1 kgf/cm
2
)
C.
Maximum inlet air temperature: 120
°
F (49
°
C)
D.
Maximum ambient temperature:
Air-cooled models: 110
°
F (43
°
C)
Water-cooled models: 130
°
F (54
°
C)
E.
Minimum ambient temperature: 45
°
F (7
°
C)
1
2
3
4
For Sales & Service Call: 705-722-5747 Ext.1