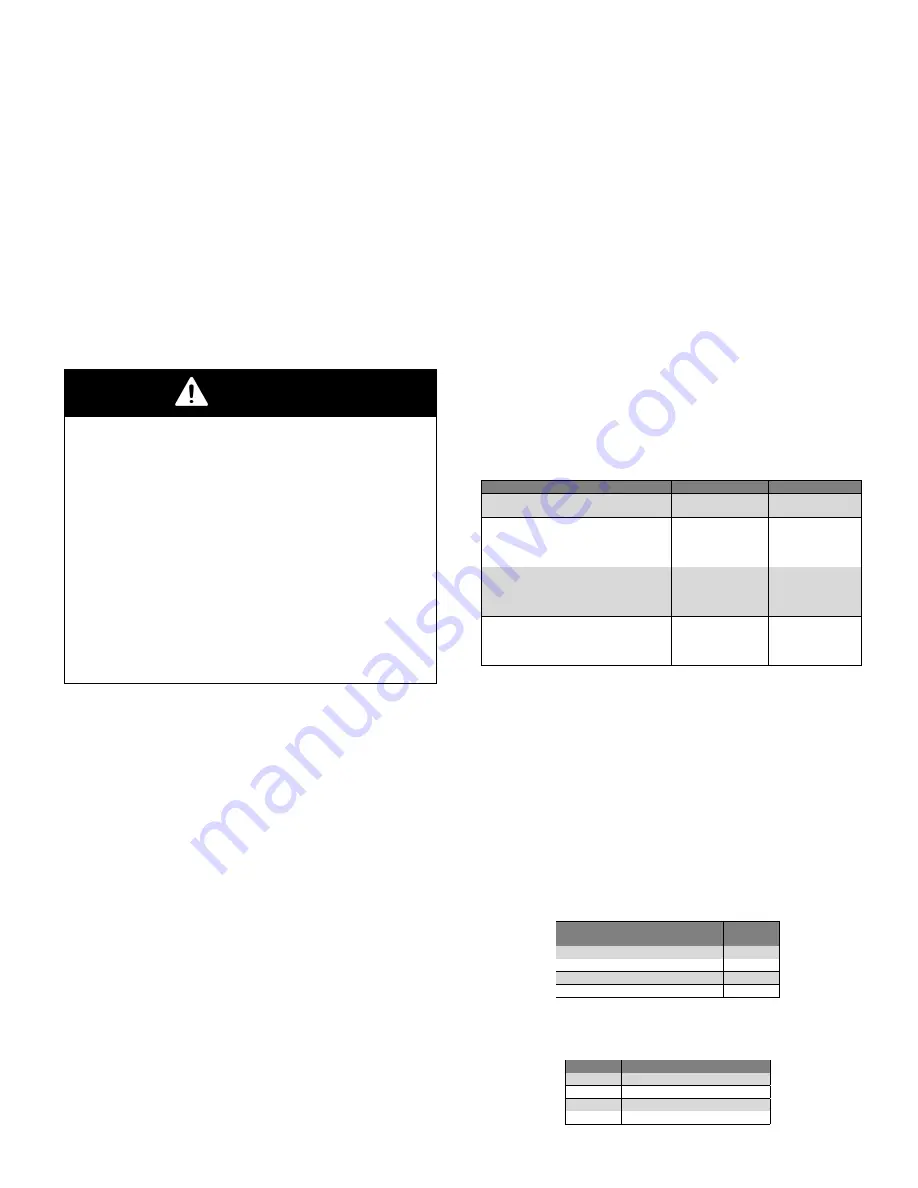
components (e.g. a condenser) on the network. This
L.E.D. will blink randomly any time a message is received
by the furnace control.
If no blinking is seen within
five minutes, it can be assumed that there is not valid
communications established. Check wiring to make sure
that all points are connected properly.
Further, if this L.E.D. is on continuously, it is an indication
that mis-wiring has occurred.
“STAT” (STATUS) (Red)
L.E.D.
– This L.E.D. blinks twice slowly (¼ second ON, ¾
second OFF) upon power-up.
Pressing the learn button for two seconds will cause the
green “RX” L.E.D. to blink rapidly (for a short period) to
indicate an attempt at communications. If the L.E.D. does
not blink, communications cannot be established.
9.11
MEMORY CARD
WARNING
Do not replace the furnace control or memory card
of the furnace with a furnace control or memory
card of another furnace or another component
(e.g.
a memory card from a condenser or air
handler). The wrong furnace control or memory
card may specify parameters which will make
the furnace run at undesired conditions including
(but not limited to) reduced airflow during heating
causing excessive undesired operation of the
main limit control.
Further, the memory card
is specific to the model number and BTU input
rating for a specific furnace and this information
should not be transported from one furnace (or
component) to another.
Furnace shared data is defined as data specific to a given
furnace that is critical for proper furnace operation. More
specifically, it is data which defines the operation of the
furnace and is unique to a given furnace platform and
model. The most critical of these data are the coefficients
that control the blower operation (i.e. define the blower
speed-torque operation). Because of this, each furnace
control is programmed with furnace shared data for that
model furnace only. The furnace shared data from any
given furnace can NOT be transferred to another furnace
for any reason. Doing so can adversely affect operation
of the furnace.
Further, if no furnace shared data is
present, the furnace will not operate in any mode and
a fault will be displayed.
9.12
REPLACING FURNACE
CONTROL
In the event that the furnace control must be replaced, the
memory card must be detached from the original furnace
control and retained with the furnace. Failure to save and
connect the memory card properly to the replacement
control may result in no operation or undesired operation
of the furnace.
When replacing the furnace control, be sure to match
the DIP switch settings of the original control on the
replacement.
9.13
DIP SWITCH
The integrated furnace control MAY not recognize switch
setting changes while energized.
DIP switches are ignored on communicating system,
except for test mode. When using the communicating
thermostat R02P032, configuration will be done throught
it. Please refer to the thermostat manual.
9.13.1
CFM Heat adjust
DIP switch bank S1 is used to fine-tune the airflow in
the heating mode.
The switches of bank S1 can be
set to adjust either the minimum heat rate airflow or the
maximum heat rate airflow or both. Also, every firing rate
in between these points will be adjusted accordingly.
NOTE:
All DIP switches on S1 will be shipped in the “OFF”
position. See Table 12.
Table 12 – Heating Airflow Adjustment - S1
S1-1
S1-2
S1-3
S1-4
DESCRIPTION
DEFAULT
OFF
OFF
OFF
OFF
NO
ADJUSTMENT
LOW FIRE
ADJUSTEMENT
(40%)
OFF
ON
OFF
OFF
-7.5%
OFF
ON
OFF
ON
-15%
OFF
ON
OFF
ON
+7.5%
OFF
ON
OFF
ON
+15%
HIGH FIRE
ADJUSTEMENT
(100%)
ON
OFF
OFF
OFF
-7.5%
ON
OFF
OFF
ON
-15%
ON
OFF
ON
OFF
+7.5%
ON
OFF
ON
ON
+15%
BOTH INPUT
ADJUSTEMENT
ON
ON
OFF
OFF
-7.5%
ON
ON
OFF
ON
-15%
ON
ON
ON
OFF
+7.5%
ON
ON
ON
ON
+15%
9.13.2
Cooling airflow select
These DIP switches are used to select the appropriate
cooling airflow based on the amount required. The switch
settings do not affect cooling airflow when installed in
fully communicating system. In that case, the condenser
supplies the information for cooling airflow which is pre-
set at the factory and not adjustable.
See tables 13 and 14 for target CFM and CFM adjust.
Table 13 – Cooling Airflow Adjustement
S3-1
S3-2
CFM
Cooling
capacity
OFF
OFF
600
1.5 T.
ON
OFF
400
1.0 T.
OFF
ON
300
0.75 T.
ON
ON
200
0.5T.
Table 14 – Cooling Airflow % Adjustement
S3-3
S3-4
DESCRIPTION
OFF
OFF
0%
ON
OFF
+10%
OFF
ON
-10%
ON
ON
0%
27
Summary of Contents for CC15-M-V
Page 18: ...Figure 17 Wiring Diagram 18...
Page 23: ...Figure 25 Direct vent clearance 23...
Page 24: ...Figure 26 Other than Direct vent clearance 24...
Page 34: ...12 PART LIST Figure 27 Exploded view...
Page 35: ...Figure 28 Exploded view continued...
Page 36: ...Table 19 Part list Chinook Compact...
Page 37: ...Table 20 Part list continued...
Page 38: ...13 NOTES 38...
Page 39: ...39...
Page 40: ...40...