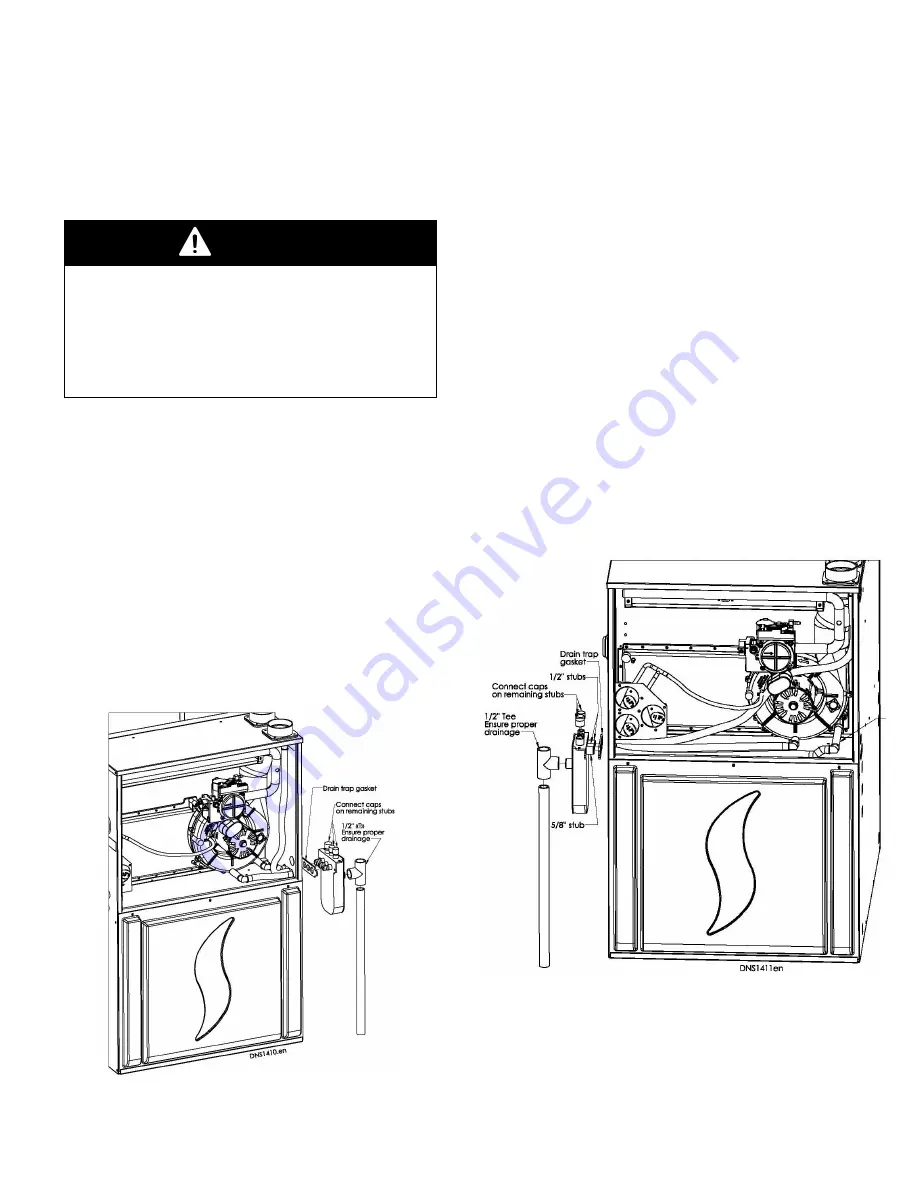
3
INSTALLATION
To ensure proper drainage of the condensate when
installed in position other than upflow, the furnace MUST
be tilted. Refer to figures corresponding to the position of
the furnace in the following sections.
CAUTION
PROPERTY DAMAGE HAZARD
Failure to follow this caution may result in water spillage
and/or property damage.
For any position other than upflow, the multiposition
pressure switch must be connected pneumatically to
the condensate box and electrically to the control to
allow the furnace to stop in the event of drain blockage.
3.1
UPFLOW
The furnace is factory built for upflow position. In this position,
the drain trap can be installed on the right or left side depending
on air return duct. When installing the furnace in the upflow
position, make sure it is leveled or tilted foward.
In the upflow orientation, the drain trap can be installed to the
right or to the left of the furnace. The location of the drain
trap is dependent of the return duct connection. The furnace
must be perfectly leveled or slightly leaned forward to help drain
condensate.
3.1.1
Right side condensate drain trap
connection
Figure 1 – Right side connection
See figure 1 and read the following instructions:
1. Remove the oblong knock-out from the right side of the
casing.
2. Place the drain trap gasket on drain trap.
3. Install the drain trap on the right side. See figure 1.
4. Screw in place the drain trap with two head tapping
screws on the right side of the furnace.
5. Connect the three stubs to the condensate tubings
already in place in the furnace.
6. Connect the outlet drain from the drain trap to an
additional condensate tubing using a ½” tee for an
adequate drainage of the condensate.
DO NOT vent
using the remaining 3 outlet stubs.
7. Prime the drain trap with water.
This will ensure
proper furnace drainage at startup and will avoid any
recirculation of flue gas.
8. On the remaining 3 outlet stub, connect caps (1x5/8” and
2x1/2”). Those caps are furnished in the parts bag.
9. If a condensate pump needs to be use, make sure it is
suited for acidic condensate.
3.1.2
Left side condensate drain trap
connection
See figure 2 and read the following instructions:
Figure 2 – Left side connection
1. Remove the oblong knock-out from the left side of the
casing.
2. Place the drain trap gasket on the drain trap.
3. Install the drain trap on the left side, the three outlet stub
of the drain trap toward the interior of the furnace.
4. Connect each condensate tubing to a stub.
Use the
furnished ½” and 5/8” tubing to cut the appropriate length
9
Summary of Contents for C105-2-V
Page 24: ...Figure 29 Direct vent clearance 23 ...
Page 25: ...Figure 30 Other than Direct vent clearance 24 ...
Page 32: ...Figure 31 Dimensions 31 ...
Page 33: ...Figure 32 Two Stage ECM Wiring diagram 32 ...
Page 36: ...Figure 33 Exploded view Cxx 2 V part 1 35 ...