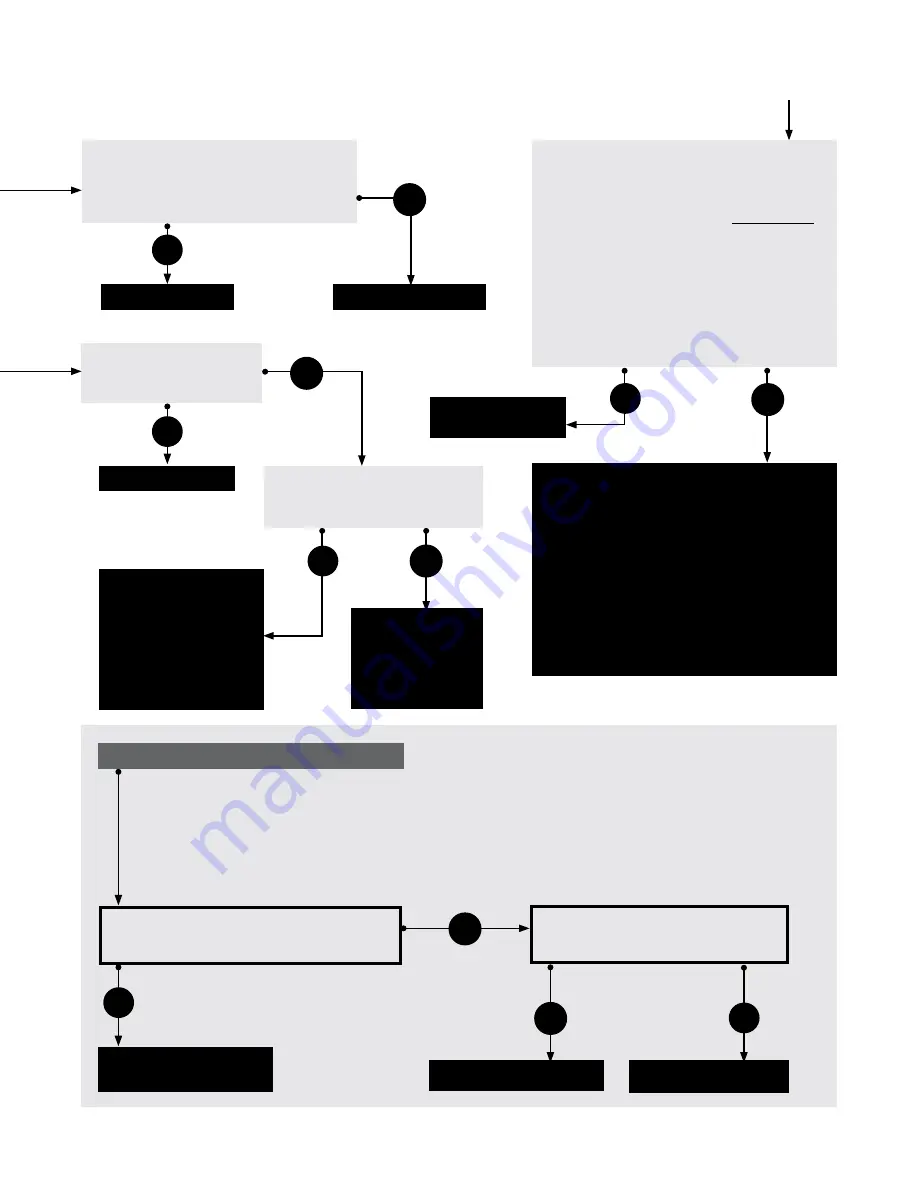
53
LD3
Series
5.0
Maintenance
•
Troubleshooting Guide
Check to make sure gas pressure is
within minimum and maximum inputs, as
indicated on the heater’s rating plate.
Is the gas pressure OK?
Is the heater properly
grounded? Is the heater’s
polarity correct?
Replace gas valve.
Correct problem.
No
Correct problem.
No
On the outside of the control box, is there
24 V across the ‘W2’ and ‘C’ connectors on
the terminal strip?
Repair or replace faulty
wiring or thermostat.
Replace relay board.
No
If heater does not go into high fire mode:
Measure voltage across the ‘HI’ and
the ‘C’ connectors on the gas valve.
Is it 24 V?
Yes
No
Yes
Replace gas valve.
NOTE
: To confirm that the heater is not in high fire mode, check manifold pressure.
If manifold pressure is 3.3” to 3.5” for natural gas or 9” to 10” for propane, the light is faulty and should
be replaced.
When the heater is in low fire mode, manifold pressure is approximately 2.0” to 2.5” for natural gas or
5.0” to 6.5” for propane. If this is the case, the following troubleshooting steps should be followed:
Yes
Replace the appropriate pressure switch
after verifying:
• There is continuity across the thermal fuse.
• Heater, fan blowers ,squirrel cage, intake
and exhaust are clean and free from dirt and
obstructions.
• The 4” air intake pipe does not exceed 20 ft.
and/or 2 elbows.
• There is not a negative pressure experienced
at the area of air intake (e.g.; high winds, attic
space, tightly sealed building).
Continued from page 51
The heater is equipped with two safety
pressure switches. The burner switch is a
normally open switch and the exhaust switch
is a normally closed switch.
Temporarily
place jumpers across the terminals of the
exhaust switch (reinstall control box cover).
Does the igniter glow red?
NOTE
: If normal operation does not continue
after bypassing the exhaust switch, consult
factory to troubleshoot the burner switch prior
to continuing.
Yes
No
With a microampmeter, check
DC amperage at flame rod. Is it
greater than .07 microamps?
Check to make
sure flame sensor
wire is OK and
then replace
circuit board.
Sensing rod is faulty or
flame is weak. Check
to make sure heater is
operating at proper gas
pressure as indicated on
heater’s rating plate and
then, if needed, replace
sensing rod.
Yes
Yes
No
Replace circuit
board.