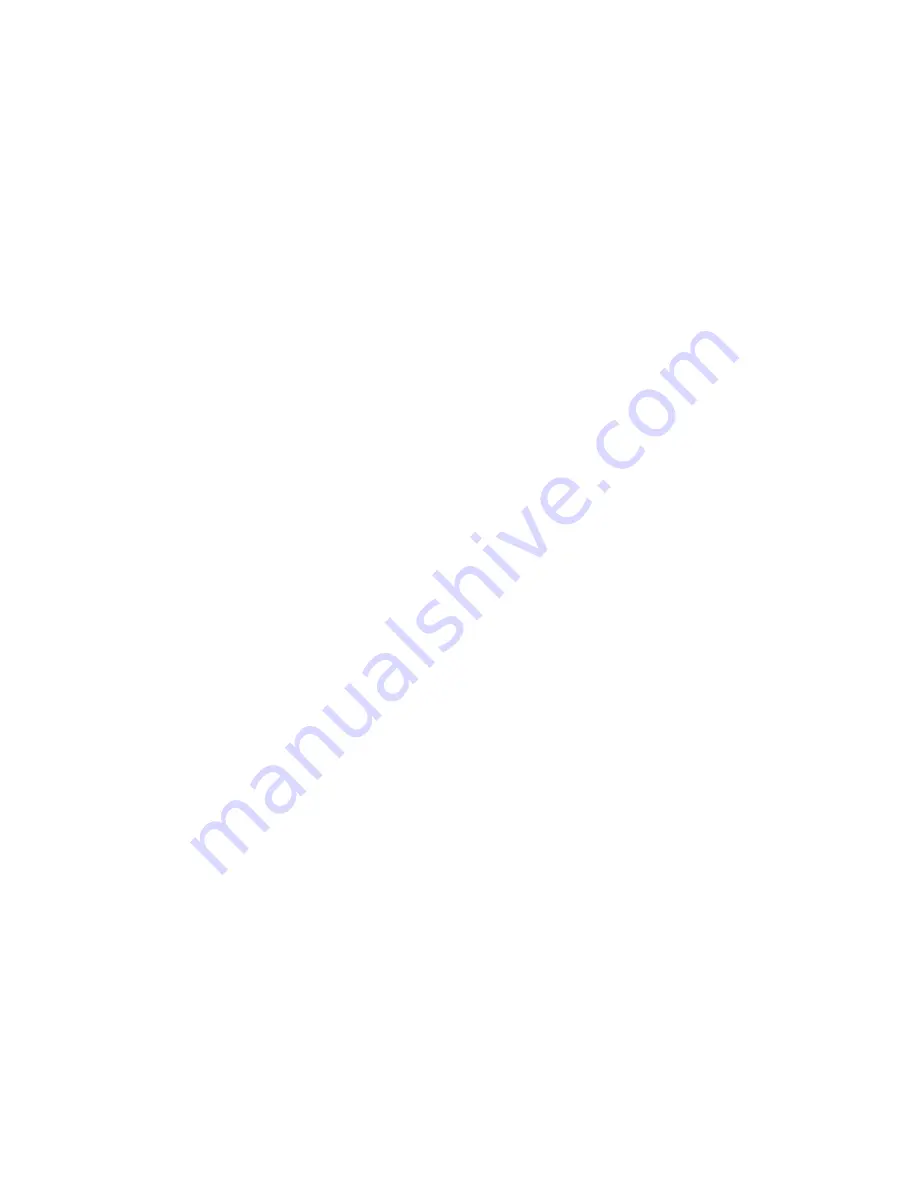
59
CL3
Series
5.0
Maintenance
•
Routine Inspection
• Vent pipe system
: Check the outside termination and the connections at the heater. Inspect the
vent exhausts for leakage, damage, fatigue, corrosion, and obstructions. If dirt becomes a problem,
installation of outside air intake ducts for combustion is recommended.
• Combustion air intake system
(when applicable): Check for blockage and/or leakage. Check the
outside termination and the connection at the heater.
• Heat exchangers
: Check the integrity of the heat exchangers. Replace if there are signs of
structural failure. Check for corrosion and/or buildup within the tube exchanger passageways.
• Burner
: Check for proper ignition, burner flame, and flame sense. Flame should extend directly
outward from burner without floating or lifting.
• Wiring:
Check electrical connections for tightness and/or corrosion. Check wires for damage.
• Gas Connection:
Inspect the integrity of the gas connection to the heater. Check for leaks,
damage, fatigue, or corrosion. Do not operate if repairs are necessary and turn off gas supply to the
heater. Contact service personnel.
•
Reflectors
: To maintain effective infrared heating, always keep both sides of the reflector clean.
Maintenance can vary significantly depending on the environment. Dirt and dust can be vacuumed
or wiped with a soap and water solution. Use metal polish if the reflectors are severely dirty.
Contact service personnel if repairs are necessary. Do not operate unit.