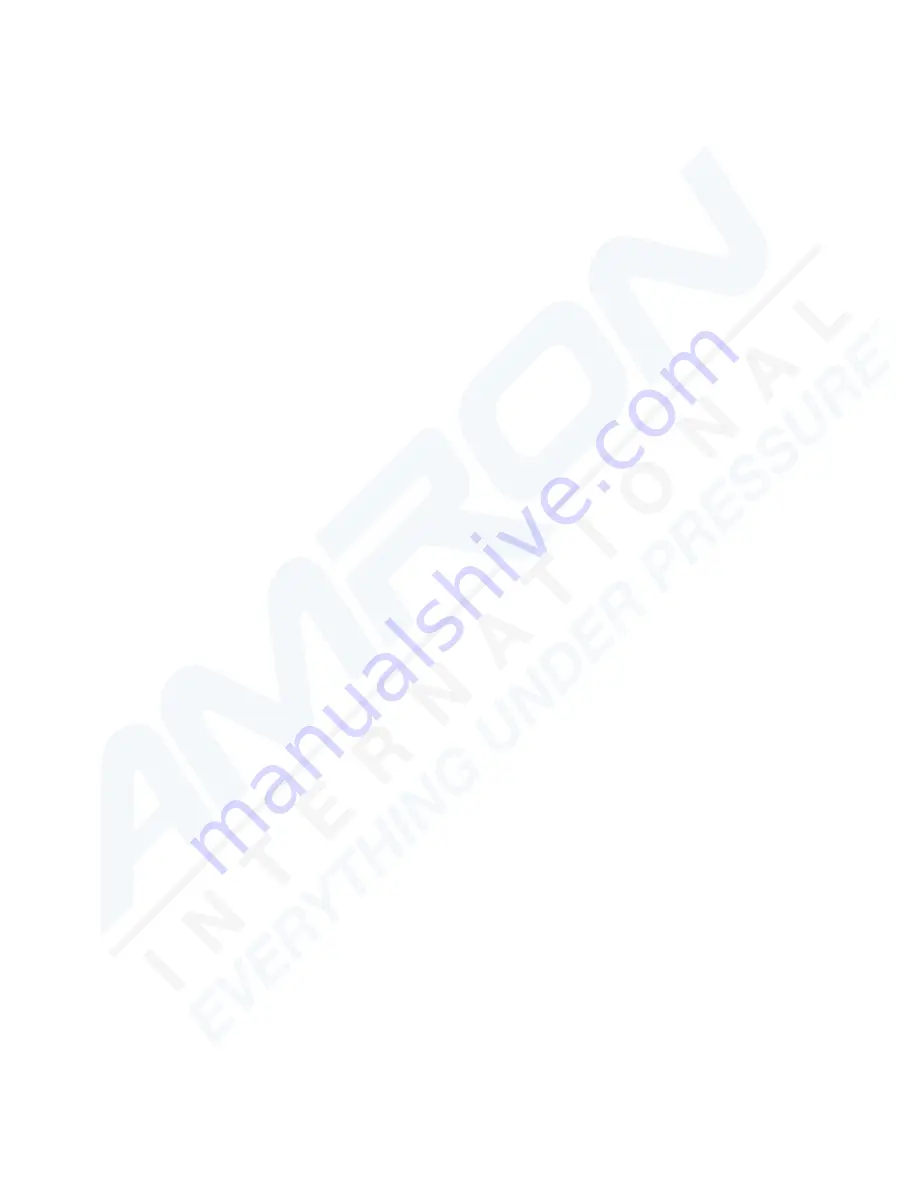
Section 3. Inspection of Air Hat Parts
Insert Ring Assembly
O-ring:
Wash the O-ring in soap and warm water to remove all dirt and contaminates. Do a careful inspection
for cuts, nicks, or gouges. Look closely at the glue seam for any evidence of potential failure.
Neckdam:
When examining for holes pay particular attention to the area where the Neckdam wraps back
around to pass under the O-ring. Slightly stretching the material aids in locating holes. Check for wear and
stretching at the lower end of the Neckdam where it contacts with the diver’s neck.
Shim:
Where the shim has been removed intact from the insert ring check for deterioration of the shim material.
Insert Ring:
Carefully inspect the insert ring for dents and nicks. Remove any burrs with very fine sandpaper.
Check the ring for evidence of damage, which may have put it out of round.
Window Assembly
Window:
Check the window carefully for cracks, scratches, or chips along the edges. Inspect the windows
gasket-sealing surface for dirt or gasket material adhering to it.
Gasket:
Wash the gasket and window with soap and warm water. Carefully inspect the gasket for cuts,
cracking, or nicks, and check that the gasket is not gotten hard or soft.
Window Screws:
Check for excessive corrosion or if the screw is bent. Look for cracking where the threads
meet the head.
Exhaust Valve Assembly
Single Exhaust Valve
: Generally look over the unit for contamination or damage. Inspect the solder joint
where the adjuster cap meets the cover. Look for corrosion or cracking. Check the movement of the plunger in
the cover assembly and the action of the spring. Work the adjuster cap as a check for the condition of the cap
threads. Excessive play in the operation of the adjuster would warrant further disassembly down to the
component parts. Check the condition of the four cover retaining screws.
Double Exhaust Valve
: Generally look over the unit for contamination or damage. Inspect the solder joint
where the adjuster cap meets the top section. Look for corrosion or cracking. Check the movement of the
plunger in the top section assembly and the action of the spring. Inspect the threads on the top section adjuster
assembly. Work the adjuster cap as a check for the condition of the cap threads. Excessive play in the operation
of the adjuster would warrant further disassembly down to the component parts. Check the condition of the
plunger in the top section and the flapper guard in the mid section. Look for signs that the flapper valve(s) may
be sticking to them.
O-ring:
Wash the O-ring on soap and warm water. Carefully inspect for cuts and nicks.
Flapper Valve(s):
Check for wear and cracking in the material. Look for signs of physical deterioration of the
material such as hardening or softening. Look for signs that the flapper valve may be sticking to the plunger or
flapper guard.
Body Sections:
Look for signs of damage or corrosion. Look for plating flaking or cracking. Check the flapper
valve sealing surface on the mid body for wear or damage. Check the threads in the mid body for dirt or
corrosion.
7
Summary of Contents for 61000
Page 13: ...11 ...