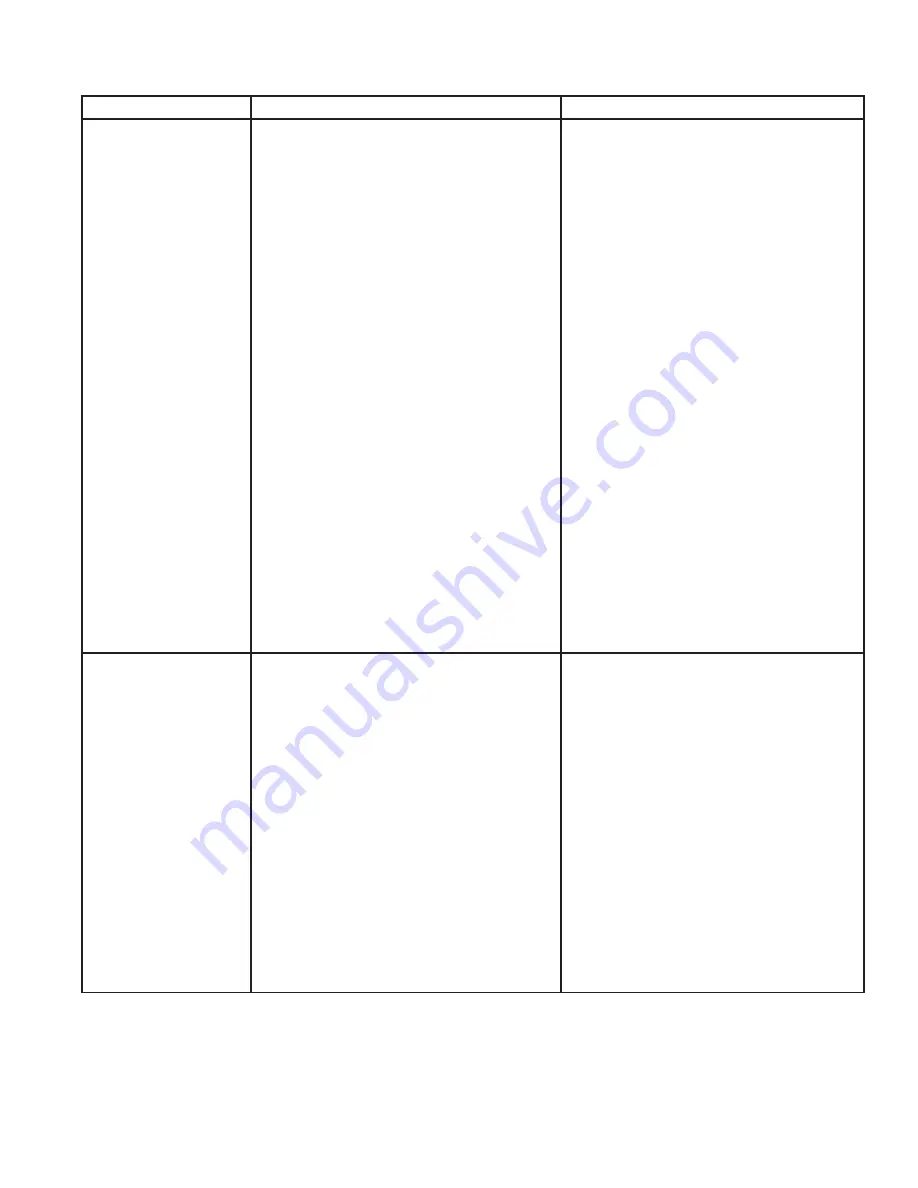
11
VII. Trouble Shooting
PROBLEM
CAUSE
REMEDY
Pump does not achieve
or maintain prime
Air trapped in suction line
Foot valve contaminated or improperly
installed
Excessive lift
Suction fittings not properly tightened
Worn or contaminated check valves
Split or pinch in suction tube
Low chemical level
Straighten suction line so as to eliminate
high spots.
Inspect foot valve screen and assure that
foot valve is in a vertical position below
fluid level.
Maximum suction lift is 5 feet with water or
fluids of similar specific gravity; less with
heavier liquids such as acids. Mount pump
in a lower position relative to the chemical
container.
Check fittings. Over-tightening may cause
restriction. Conversely, if
any
leakage occurs,
pump will suck air and fail to prime.
Inspect check valves in fluid end for cleanliness.
Clean or replace as necessary.
Inspect suction tube through its full length
to assure that there are no splits at the
connections or other restrictions. Move
any objects or equipment which impinges
upon suction tube or reroute as required to
assure a smooth transition from foot valve
to pump.
Check fluid level in chemical supply tank.
Insufficient fluid
Stroke adjustment set too low
Worn or contaminated check valves
Obstruction in suction line
Clogged foot valve screen
Output (system) pressure too high
Diaphragm worn or torn
Electronic failure
Check operation of stroke limiter knob.
If pump delivers too low adjustable rate,
check settings. Readjust as required.
Inspect, clean or replace as necessary.
Check suction line for obstructions, clogging,
kinks or pinch points.
Clean or replace foot valve screen.
Relocate the injector to a lower pressure part
of the system.
Replace diaphragm, making sure that it is
screwed on fully to shoulder of shaft.
Consult dealer or factory.