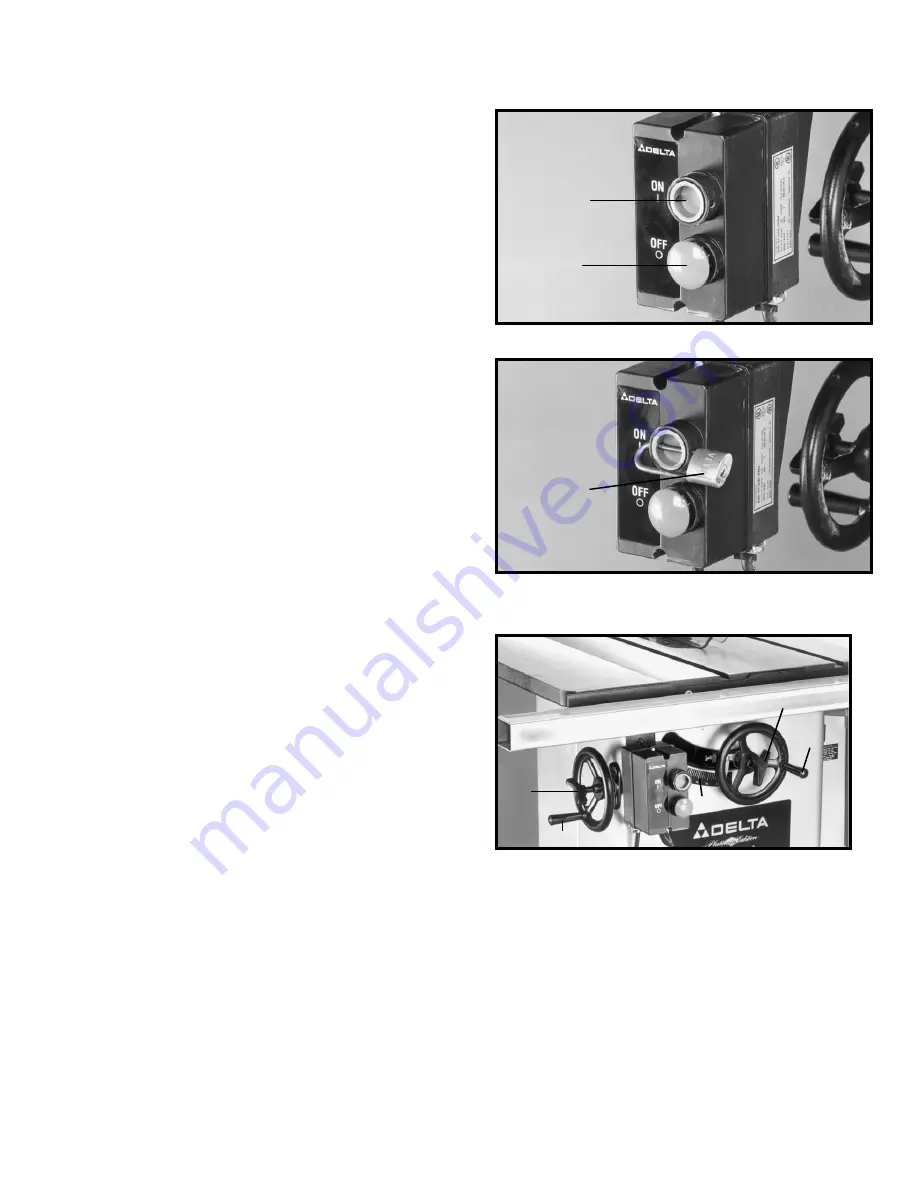
29
OPERATING CONTROLS
AND UNISAW ADJUSTMENTS
STARTING AND STOPPING
THE SAW
To apply power to the machine, push “ON” button (A) Fig.
106. To stop the machine, push “OFF” button (B).
Fig. 106
A
B
LOCKING SWITCH
IN THE “OFF” POSITION
IMPORTANT:
When the tool is not in use, the switch
should be locked in the OFF position using a padlock (A)
Fig. 107, with a 3/16" diameter shackle to prevent
unauthorized use.
Fig. 107
A
BLADE RAISING
MECHANISM
The saw blade is raised and lowered with the front
handwheel (A) Fig. 108. With the exception of hollow
ground blades, the blade should be raised 1/8" to 1/4"
above the top surface of the material being cut. With
hollow ground blades, the blade should be raised the
maximum to provide greater clearance. To raise the saw
blade, loosen lock knob (B) Fig. 108, and turn the
handwheel (A), clockwise. To lower the saw blade, turn
handwheel (A) counterclockwise.
The saw blade is locked at any height by turning the lock
knob (B) Fig. 108, clockwise. Due to the wedge action of
this locking device, only a small amount of force is
required to lock the blade raising mechanism securely.
Any added force merely puts unnecessary strain on the
locking device. Limit stops for raising or lowering are
permanently built into the mechanism and need no
further adjustment.
Fig. 108
D
C
B
A
E
BLADE TILTING MECHANISM
The blade tilting mechanism allows the blade to be tilted
up to 45 degrees to the right.
To tilt the saw blade to the desired angle, loosen lock
knob (D) Fig. 108, and turn handwheel (C). A pointer
indicates the angle of tilt on scale (E), which is marked in
one-degree increments. To lock the saw blade in the
desired angle of tilt, tighten lock knob (D).
IMPORTANT: ALWAYS LOCK THE BLADE IN
POSITION BEFORE APPLYING POWER TO THE SAW.
OVERLOAD PROTECTION
Your saw is supplied with overload protection. If the
motor shuts off or fails to start due to overloading
(cutting stock too fast, using a dull blade, using the saw
beyond its capacity, etc.) or low voltage, let the motor
cool three to five minutes. The overload will
automatically reset itself and the machine can then be
started again by pressing the “ON” button.
IMPORTANT:
If the motor continually shuts off due to
overloading, the cause of overloading must be
corrected. If this happens, it is recommended that you
contact a qualified electrician.