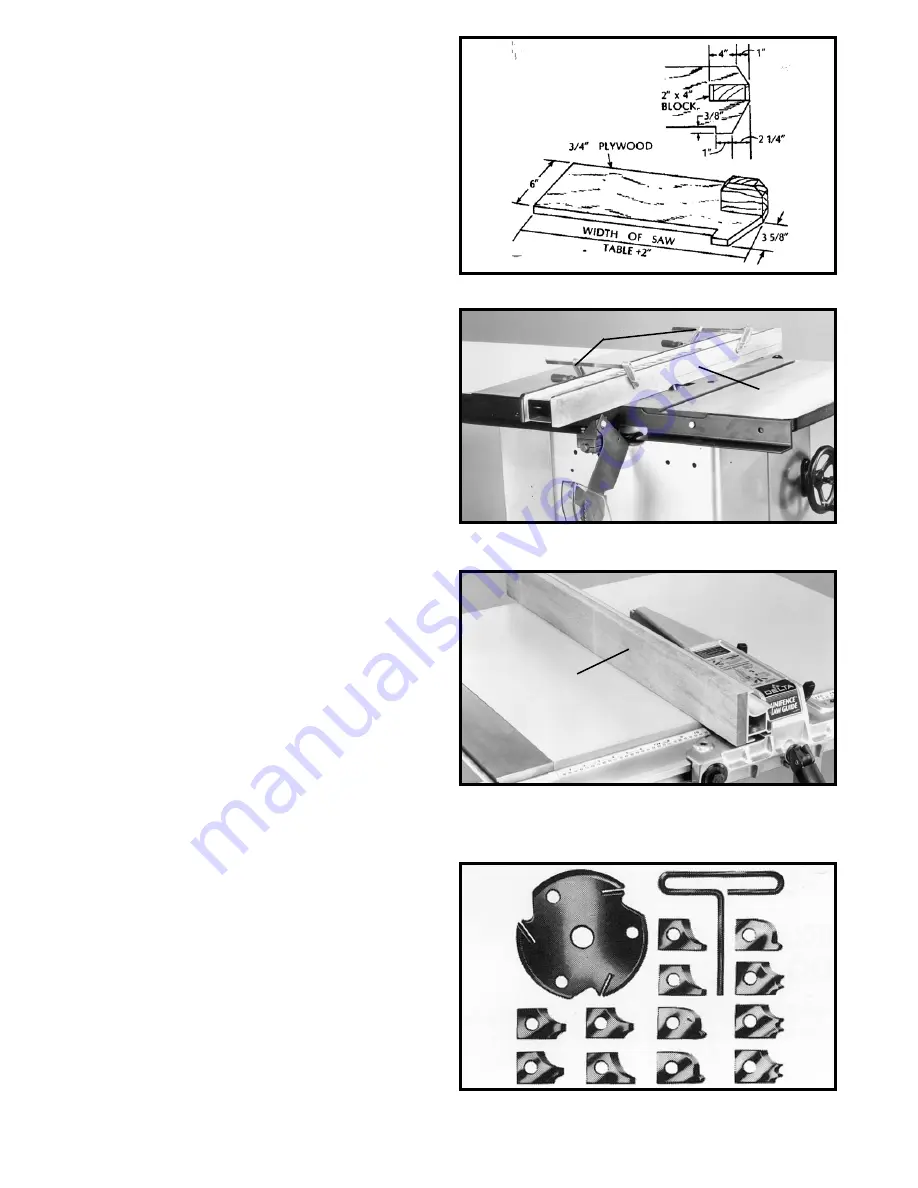
20
Fig. 61
USING AUXILIARY WOOD
FACING ON BIESEMEYER
RIP FENCE
It is necessary when performing special operations such
as moulding to add wood facing (A) Fig. 62, to one or
both sides of the rip fence, as shown. The wood facing is
attached to the fence with two clamps (B). 3/4 inch stock
is suitable for most work although an occasional job may
require 1 inch facing.
A wood facing should be used when ripping thin material
such as paneling to prevent the material from catching
between the bottom of the rip fence and the saw table
surface.
Fig. 62
B
A
Fig. 64
USING ACCESSORY
MOULDING CUTTERHEAD
Moulding is cutting a shape on the edge or face of the
work. Cutting mouldings with a moulding cutterhead in
the circular saw is a fast, safe and clean operation. The
many different knife shapes available make it possible for
the operator to produce almost any kind of mouldings,
such as various styles of corner moulds, picture frames,
table edges, etc.
The moulding head consists of a cutterhead in which can
be mounted various shapes of steel knives, as shown in
Fig. 64. Each of the three knives in a set is fitted into a
groove in the cutterhead and securely clamped with a
screw. The knife grooves should be kept free of sawdust,
which would prevent the cutter from seating properly.
USING AUXILIARY WOOD
FACING ON THE UNIFENCE
Fig. 63
It is necessary when performing special operations such
as when using the moulding cutterhead to add wood
facing (A) Fig. 63, to one side of the rip fence as shown.
The wood facing is attached to the fence with wood
screws through holes you drill in the fence. A suitable
stock size for most work is 3/4", although an occasional
job may require one inch facing.
A
When ripping boards longer than three feet, it is
recommended that a work support be used at the rear of
the saw to keep the workpiece from falling off the saw
table.
If the ripped work is less than 4 inches wide, a push stick
should always be used to complete the feed, as shown in
Fig. 60. The push stick can easily be made from scrap
material as explained in the section
“CONSTRUCTING A
PUSH STICK.”
When ripping material under 2 inches in
width, a flat pushboard is a valuable accessory since
ordinary type sticks may interfere with the blade guard.
That flat pushboard can be made as shown in Fig. 61.
Summary of Contents for UNISAW 34-801
Page 27: ...27 NOTES...