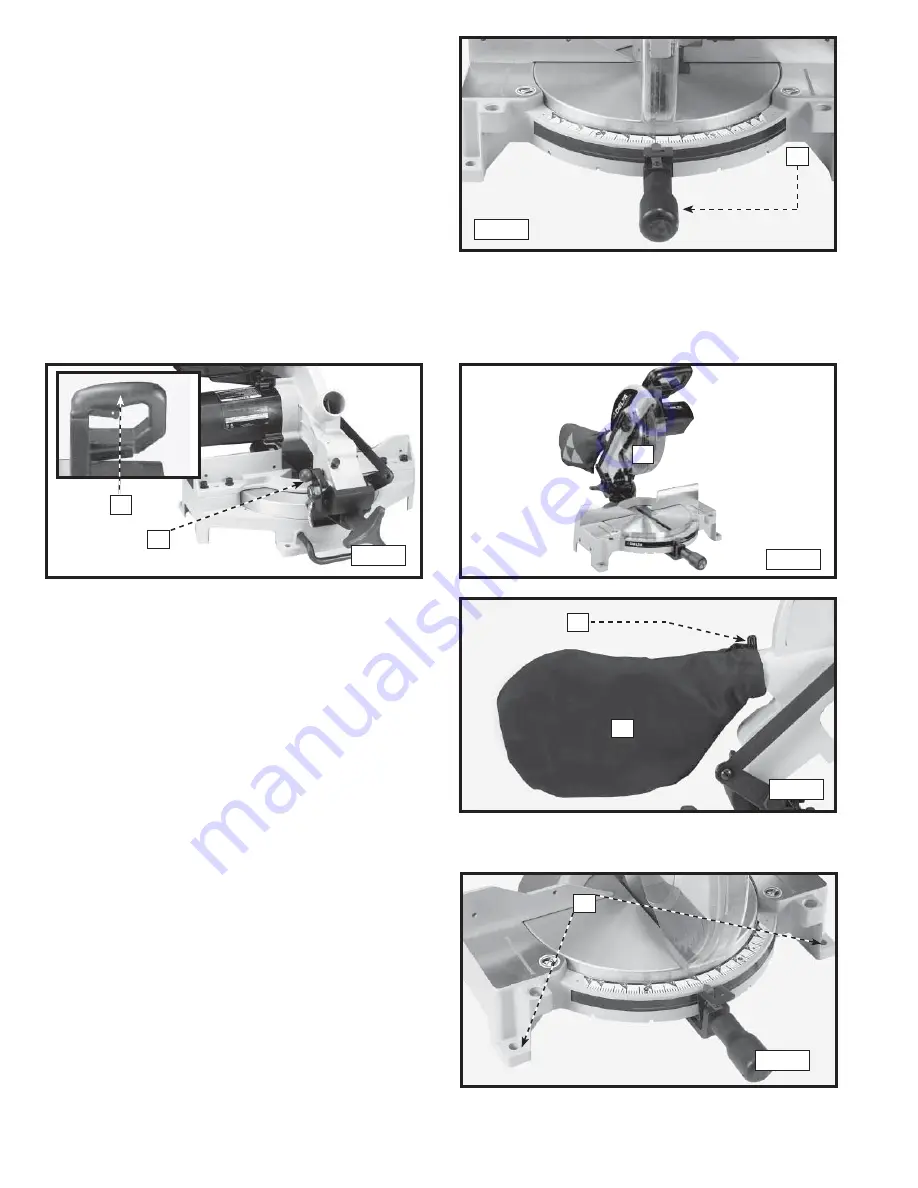
10
FASTENING THE MACHINE TO A SUPPORTING SURFACE
Before operating your compound miter saw, make sure that it
is firmly mounted to a sturdy workbench or other supporting
surface. Four holes are provided, two of which are shown at
(A) Fig. 10.
When frequently moving the saw from place to place, mount
the saw on a 3/4" piece of plywood, and clamp the plywood
to a supporting surface with “C” clamps.
2. Rotate the table to the left until the index stop engages
with the 90° positive stop (Fig. 6). Tighten the table lock
handle (A).
1. Push down on handle (A), Inset, Fig. 7. Pull out the cuttinghead lock knob (B).
2. Move the cuttinghead (C) to the up position (Fig. 8).
ATTACHING THE DUST BAG
Squeeze the spring clips (A) Fig. 9 of the dust bag (B) and clip
the dust bag (B) over the ribs of the dust chute.
MOVING CUTTINGHEAD TO THE UP POSITION
Fig. 6
A
Fig. 7
Fig. 8
A
B
C
Fig. 9
A
B
A
Fig. 10