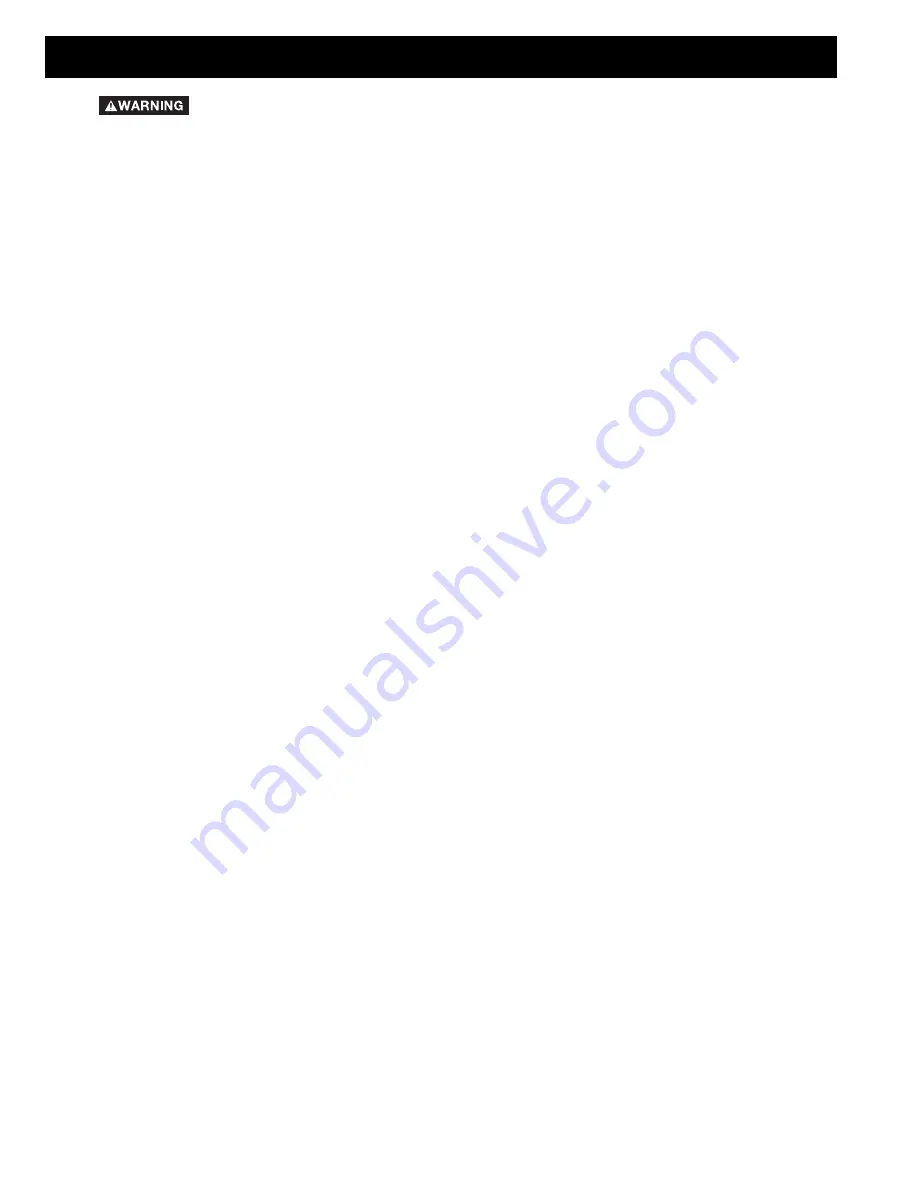
4
ADDITIONAL SAFETY RULES FOR FOR DRILL PRESSES
1.
DO NOT OPERATE THIS MACHINE
until it is
completely assembled and installed according to
the instructions. A machine incorrectly assembled can
cause serious injury.
2.
OBTAIN ADVICE
from your supervisor, instructor,
or another qualified person if you are not
thoroughly familiar with the operation of this
machine. Knowledge is safety.
3.
FOLLOW ALL WIRING CODES
and recommended
electrical connections to prevent shock or electrocution.
4.
SECURE THE MACHINE TO A SUPPORTING SUR-
FACE.
Vibration can cause the machine to slide, walk,
or tip over.
5.
NEVER START THE MACHINE BEFORE
CLEARING THE TABLE OF ALL OBJECTS
(tools,
scrap pieces, etc.). Debris can be thrown at high
speed.
6
.
NEVER START THE MACHINE
with the drill bit,
cutting tool, or sanding drum against the
workpiece. Loss of control of the workpiece can
cause serious injury.
7.
PROPERLY LOCK THE DRILL BIT, CUTTING TOOL,
OR SANDING DRUM IN THE CHUCK
before
operating this machine.
8.
REMOVE THE CHUCK KEY BEFORE STARTING
THE MACHINE.
The chuck key can be thrown out
at a high speed.
9.
TIGHTEN ALL LOCK HANDLES
before starting the
machine
.
Loss of control of the workpiece can
cause serious injury.
10.
USE ONLY DRILL BITS, CUTTING TOOLS,
SANDING DRUMS, OR OTHER ACCESSORIES
with shank size recommended in your instruction
manual. The wrong size accessory can cause
damage to the machine and/or serious injury.
11.
USE ONLY DRILL BITS, CUTTING TOOLS, OR
SANDING DRUMS
that are not damaged.
Damaged items can cause malfunctions that lead
to injuries.
12
.
USE RECOMMENDED SPEEDS
for all operations.
Other speeds may cause the machine to
malfunction causing damage to the machine
and/or serious injury.
13.
AVOID AWKWARD OPERATIONS AND HAND
POSITIONS.
A sudden slip could cause a hand to
move into the bit.
14
.
KEEP ARMS, HANDS, AND FINGERS
away from
the bit. Serious injury to the hand can occur.
15.
HOLD THE WORKPIECE FIRMLY AGAINST THE
TABLE.
Do not attempt to drill a workpiece that
does not have a flat surface against the table, or
that is not secured by a vise. Prevent the
workpiece from rotating by clamping it to the table
or by securing it against the drill press column.
Loss of control of the workpiece can cause serious
injury.
16.
TURN THE MACHINE “OFF” AND WAIT FOR THE
DRILL BIT, CUTTING TOOL, OR SANDING DRUM
TO STOP TURNING
prior to cleaning the work area,
removing debris, removing or securing work-piece,
or changing the angle of the table. A moving drill
bit, cutting tool, or sanding drum can cause
serious injury.
17.
PROPERLY SUPPORT LONG OR WIDE
work-
pieces. Loss of control of the workpiece can cause
severe injury.
18.
NEVER PERFORM LAYOUT, ASSEMBLY OR
SET-UP WORK
on the table/work area when the
machine is running. Serious injury can result.
19.
TURN THE MACHINE “OFF”,
disconnect the
machine from the power source, and clean the
table/work area before leaving the machine.
LOCK
THE SWITCH IN THE “OFF” POSITION
to
prevent unauthorized use. Someone else might
accidentally start the machine and cause serious
injury to themselves.
20.
ADDITIONAL INFORMATION
regarding the safe
and proper operation of power tools (i.e. a safety
video) is available from the Power Tool Institute,
1300 Sumner Avenue, Cleveland, OH 44115-2851
(www.powertoolinstitute.com). Information is also
available from the National Safety Council, 1121
Spring Lake Drive, Itasca, IL 60143-3201. Please
refer to the American National Standards Institute
ANSI 01.1 Safety Requirements for Woodworking
Machines and the U.S. Department of Labor OSHA
1910.213 Regulations.
SAVE THESE INSTRUCTIONS
.
Refer to them often
and use them to instruct others
.
FAILURE TO FOLLOW THESE RULES MAY RESULT IN SERIOUS INJURY.
Summary of Contents for ShopMaster DP400
Page 19: ...19 NOTES...