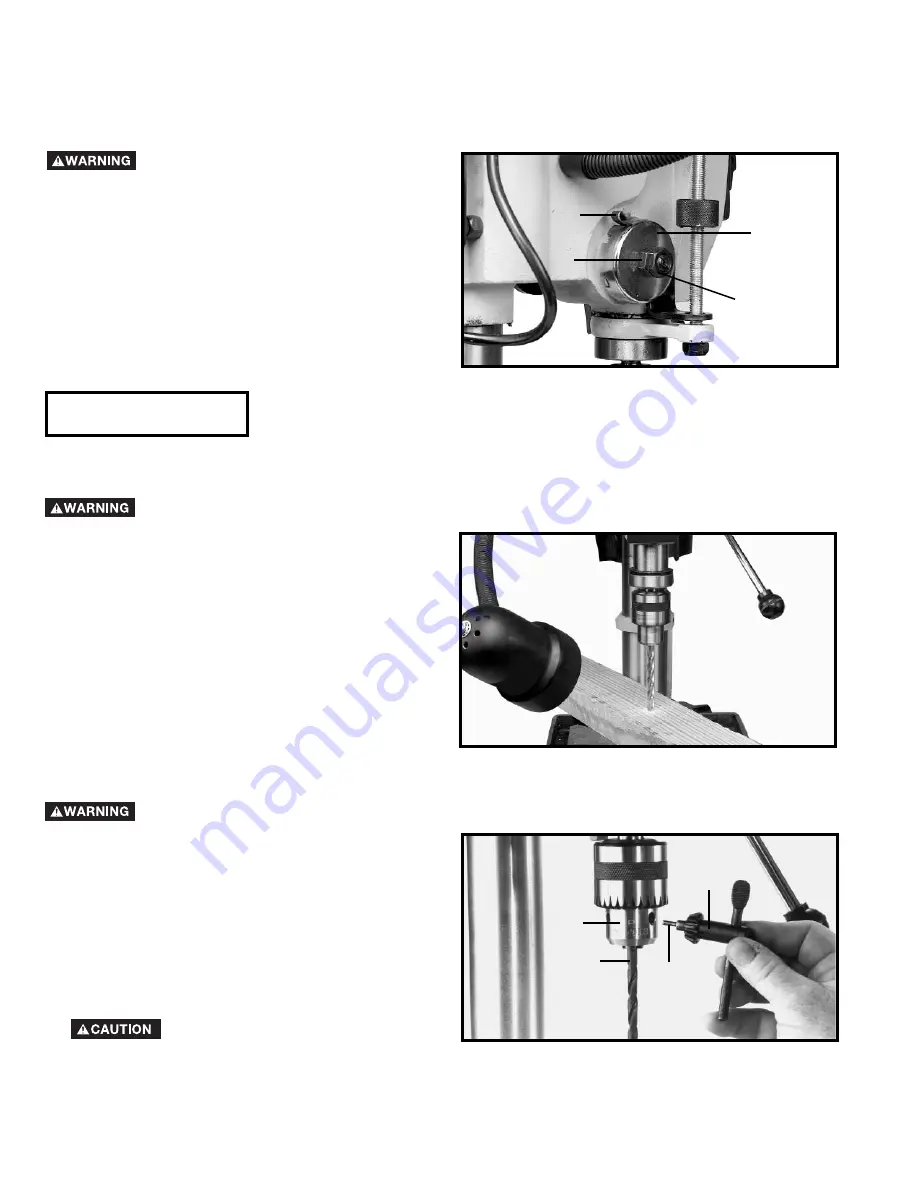
14
INSTALLING AND REMOVING DRILL
BITS
DISCONNECT MACHINE FROM POWER
SOURCE.
1.
Insert smooth end of drill bit (A) Fig. 29, into chuck
(B), as far as it will go, and then back the bit out 1/16",
or up to the flutes for small bits.
2.
Make certain that the drill bit (A) Fig. 29, is centered
in the chuck (B) before tightening the chuck with the key
(C).
3.
Turn the chuck key (C) Fig. 29, clockwise to tighten
and counterclockwise to loosen the chuck jaws.
4.
Tighten all three chuck jaws to secure the drill bit
sufficiently so that it does not slip while drilling.
5.
MAKE SURE
chuck key (C) Fig. 29, is
removed from chuck before starting drill press. Your
chuck key (C) is equipped with a self-ejecting pin (D)
which helps minimize the hazard of the key being left in
the chuck.
Fig. 29
A
B
C
D
ADJUSTING SPINDLE RETURN SPRING
The spindle is automatically returned to its upper most position when the handle is released. It is recommended that
the handle be allowed to slowly return to the top position after each hole has been drilled in the material. This spring
has been properly adjusted at the factory and should not be disturbed unless absolutely necessary. To adjust the return
spring:
DISCONNECT MACHINE FROM POWER
SOURCE.
1.
Loosen nuts (B) and (E) Fig. 27. Make sure spring
housing (A) stays engaged with head casting.
2.
While
FIRMLY HOLDING
spring housing (A) Fig. 27
pull out housing and rotate it until boss (D) is engaged
with the next notch on the housing. Turn the housing
counterclockwise to increase or clockwise to decrease
spring tension. Turn nut (E) until it contacts spring
housing (A), then back nut (E) out a 1/4 turn from spring
housing (A). Tighten nut (B) against nut (E), to hold the
housing in place.
IMPORTANT: Inside nut (E) should
not contact spring housing (A) when tightened.
Fig. 27
Your drill press is to be used with drill bits with a shank of 1/2" or less in diameter. The following will give the inexperienced
operator a start on common drill press operations. Use scrap material for practice to get a feel of the machine before
attempting regular work.
The use of accessories and attachments not recommended by Delta may result in risk of injury.
IMPORTANT:
When the workpiece is long enough it
should always be positioned on the table with one end
against the left side of the column, as shown in Fig. 28.
This prevents the workpiece from rotating with the drill
bit or cutting tool, causing damage to the workpiece or
personal injury to the operator. If it is not possible to
support the workpiece against the column, the
workpiece should always be fastened to the table using
clamps or a vise.
Fig. 28
A
D
E
B
MACHINE USE