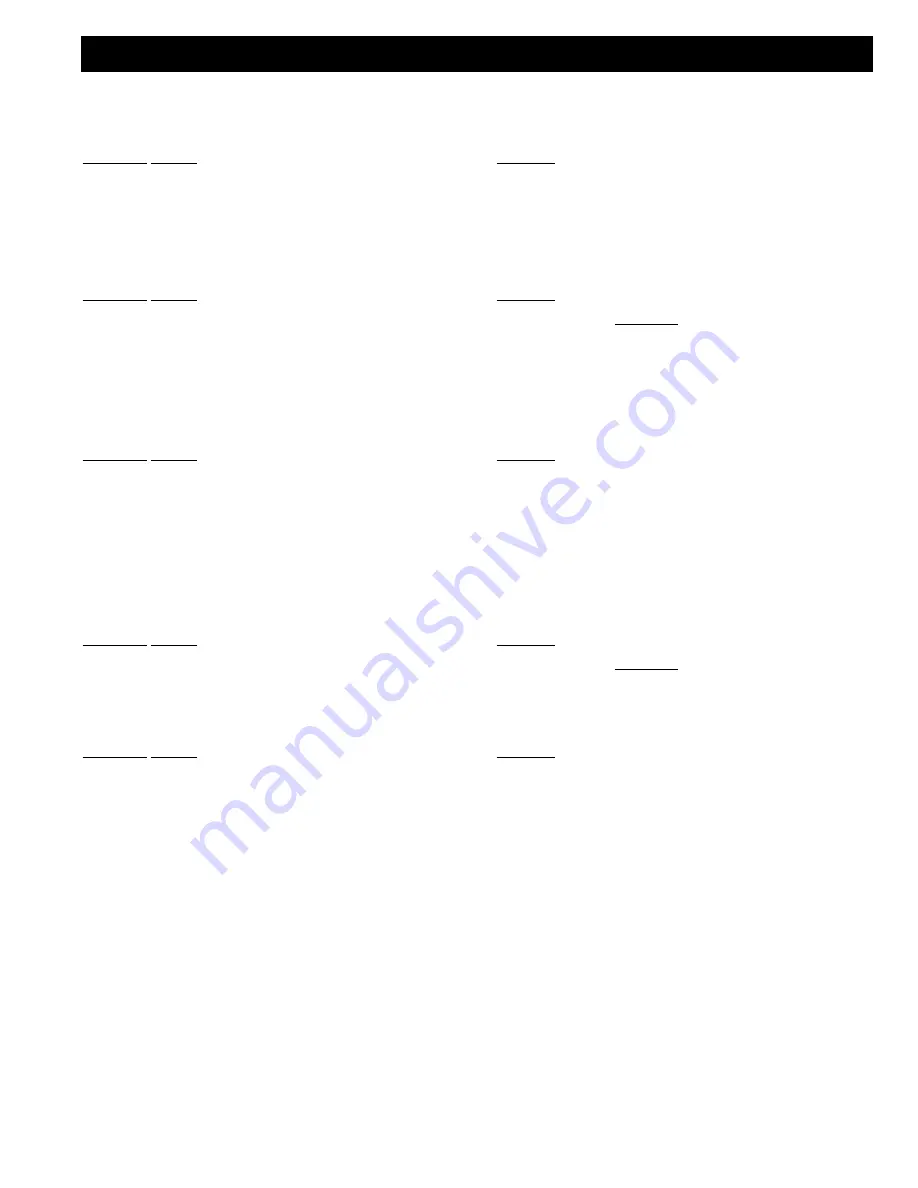
19
In spite of how well a band saw is maintained, problems can occur. The following troubleshooting
guide will help you solve the more common problems:
Trouble:
SAW WILL NOT START.
Probable Cause
Remedy
1. Saw not plugged in.
1. Plug in saw.
2. Fuse blown or circuit breaker tripped.
2. Replace fuse or reset circuit breaker.
3. Cord damaged.
3. Have cord replaced.
Trouble:
BREAKER KICKS OUT FREQUENTLY.
Probable Cause
Remedy
1. Extension cord too light or too long.
1. Replace with adequate size cord.
2. Feeding stock too fast.
2. Feed stock more slowly.
3. Blade in poor condition (dull, warped, gummed).
3. Clean or replace blade.
4. Low voltage supply.
4. Contact your electric company.
Trouble:
BAND SAW VIBRATES EXCESSIVELY.
Probable Cause
Remedy
1. Machine not mounted securely to workbench.
1. Tighten all mounting hardware.
2. Bench on uneven surface.
2. Reposition on flat level surface.
3. Worn belt.
3. Replace belt.
4. Belt not tensioned correctly.
4. Adjust belt tension by moving motor.
5. Motor not fastened securely.
5. Tighten all mounting hardware.
Trouble:
BAND SAW DOES NOT COME UP TO SPEED.
Probable Cause
Remedy
1. Low voltage due to improper extension cord size.
1. Replace with adequate size cord.
2. Low voltage.
2. Contact your electric company.
Trouble:
BLADES BREAK.
Probable Cause
Remedy
1. Blade not tensioned properly.
1. Adjust blade tension.
2. Blade guides improperly adjusted.
2. Check and adjust blade guides.
3. Blade support bearing improperly adjusted.
3. Adjust blade support bearing.
4. Blade wheel tracking adjustment improperly set.
4. Check and adjust blade tracking.
5. Bad weld on blade.
5. Replace the blade.
6. Worn tires.
6. Replace tires.
7. Forcing wide blade around short radius.
7. Change to a narrower blade.
8. Dull blade or insufficient set.
8. Replace blade.
9. Upper blade guide set too high.
9. Set upper blade guide within 1/8" of workpiece.
10. Continuous running of machine when not actually
10. Turn off machine when not performing cutting
cutting.
operation.
(continued on next page)
TROUBLESHOOTING GUIDE
Summary of Contents for ShopMaster BS100
Page 22: ...22 NOTES...
Page 23: ...23 NOTES...