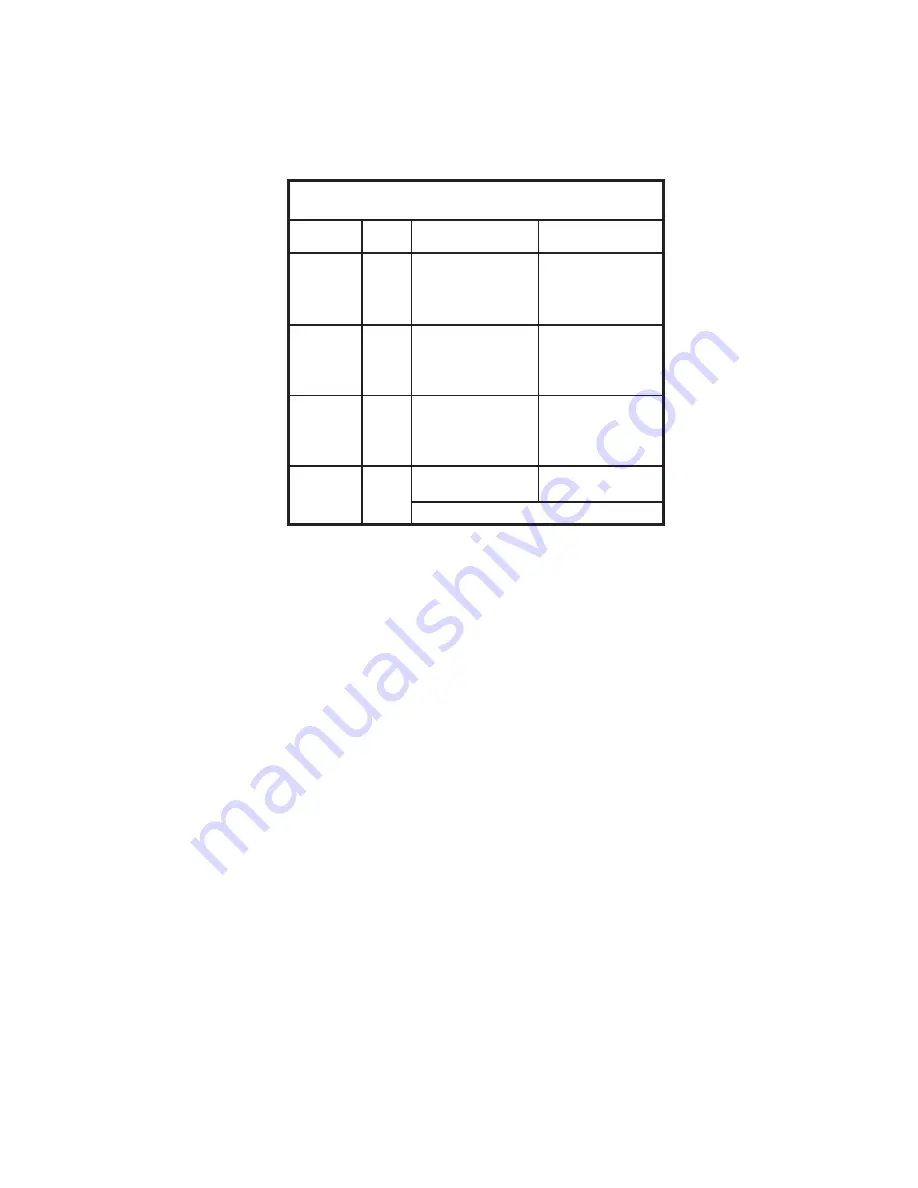
Use proper extension cords. Make sure your extension cord is in good condition and is a 3-wire extension cord which
has a 3-prong grounding type plug and matching receptacle which will accept the machine’s plug. When using an
extension cord, be sure to use one heavy enough to carry the current of the machine. An undersized cord will cause
a drop in line voltage, resulting in loss of power and overheating. Fig. D, shows the correct gauge to use depending
on the cord length. If in doubt, use the next heavier gauge. The smaller the gauge number, the heavier the cord.
EXTENSION CORDS
OPERATING INSTRUCTIONS
FOREWORD
The Delta ShopMaster Model SA350 has a large 18" diameter cast-iron table, to support large workpieces. The
machine has a heavy-duty motor assembly, which features a 1/4 H.P. induction motor with direct drive for quiet, and
smooth operation.
UNPACKING AND CLEANING
Carefully unpack the machine and all loose items from the shipping container(s). Remove the protective coating from
all unpainted surfaces. This coating may be removed with a soft cloth moistened with kerosene (do not use acetone,
gasoline or lacquer thinner for this purpose). After cleaning, cover the unpainted surfaces with a good quality household
floor paste wax.
NOTICE: THE MANUAL COVER PHOTO ILLUSTRATES THE CURRENT
PRODUCTION MODEL. ALL OTHER ILLUSTRATIONS ARE REPRESENTATIVE
ONLY AND MAY NOT DEPICT THE ACTUAL COLOR, LABELING OR
ACCESSORIES AND MAY BE INTENDED TO ILLUSTRATE TECHNIQUE ONLY.
5
Fig. D
MINIMUM GAUGE EXTENSION CORD
RECOMMENDED SIZES FOR USE WITH STATIONARY ELECTRIC MACHINES
Ampere
Total Length
Gauge of
Rating
Volts
of Cord in Feet
Extension Cord
0-6
120
up to 25
18 AWG
0-6
120
25-50
16 AWG
0-6
120
50-100
16 AWG
0-6
120
100-150
14 AWG
6-10
120
up to 25
18 AWG
6-10
120
25-50
16 AWG
6-10
120
50-100
14 AWG
6-10
120
100-150
12 AWG
10-12
120
up to 25
16 AWG
10-12
120
25-50
16 AWG
10-12
120
50-100
14 AWG
10-12
120
100-150
12 AWG
12-16
120
up to 25
14 AWG
12-16
120
25-50
12 AWG
12-16
120
GREATER THAN 50 FEET NOT RECOMMENDED