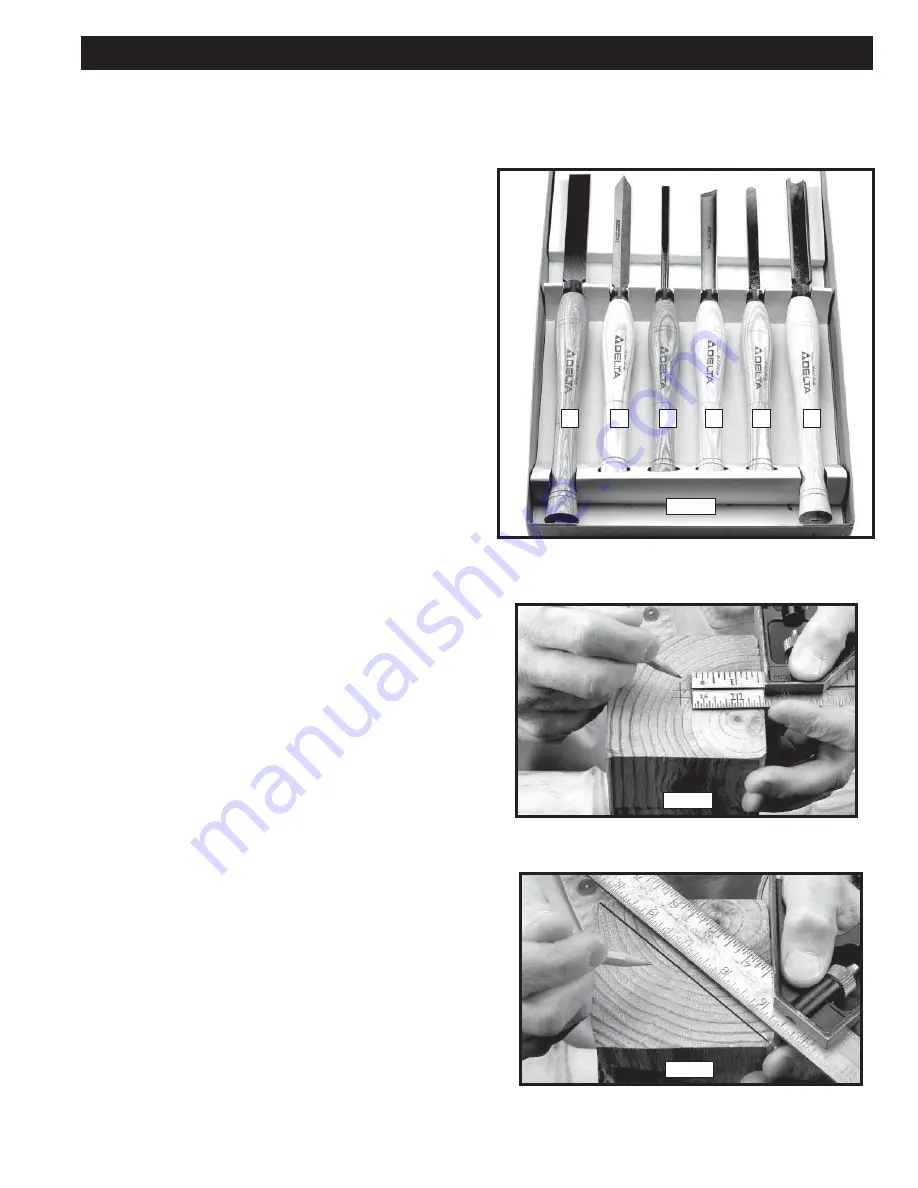
13
LATHE TOOLS
Standard wood turning tools come in several different
configurations (Fig. 26). The majority of turnings will
require the gouge tool (A) Fig. 26. This round nosed
hollow chisel is used for roughing cuts, cove cuts and
other operations. The skew chisel (B) is a double-ground
flat chisel, with an angled end. This tool is used for
smoothing cylinders, for cutting shoulders, beads, vee-
grooves, etc. The parting tool (C) is a double-ground
chisel, used for cutting-off, or for making straight
incisions or sizing cuts to any required diameter. The
round nose scraper (D) is used for mostly hollowing
work, while the square-end scraper is mainly used for
the outside of bowls.
The following directions will give the inexperienced operator a beginning point for common lathe operations. Practice
on scrap material before attempting serious work.
HOW TO TURN SPINDLES
Working with any material that is attached to the lathe
centers is called a spindle turning. This is the principal
type of wood turning (chair and table legs, lamp stems,
etc.) The turning of spindles can be done with either a
scraping or cutting technique. The cutting technique, by
virtue of faster wood removal and a cleaner surface, is the
preferred method.
CENTERING THE WORK
Wood stock for any spindle turning should be approx-
imately square, and the ends should be square with the
sides. Two common methods of determining the center
are shown in Figs. 27 and 28. In Fig. 27, a distance a
little more or a little less than one-half the width of the
stock is set off from each of the four sides. The small
square set off in the center can then be used in marking
the true center. The diagonal method, Fig. 28, consists
of drawing lines from corner to corner, with the intersec-
tion marking the center of the work.
OPERATION
Fig. 26
Fig. 27
Fig. 28
A
B
D
A
C
E