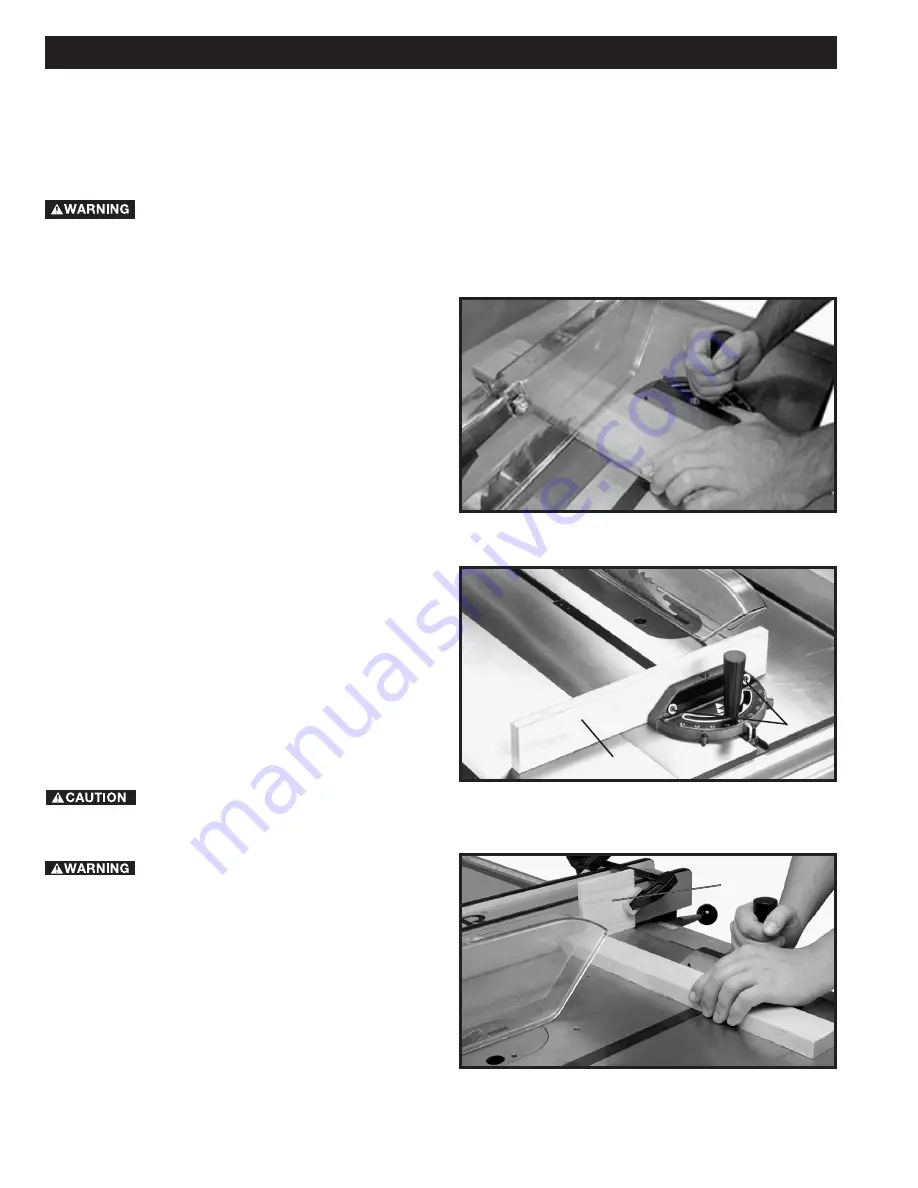
18
OPERATIONS
Common sawing operations include ripping and crosscutting plus a few other standard operations of a fundamental
nature. As with all power machines, there is a certain amount of hazard involved with the operation and use of the
machine. Using the machine with the respect and caution demanded as far as safety precautions are concerned, will
considerably lessen the possibility of personal injury. However, if normal safety precautions are overlooked or completely
ignored, personal injury to the operator can result. The following information describes the safe and proper method for
performing the most common sawing operations.
THE USE OF ATTACHMENTS AND ACCESSORIES NOT RECOMMENDED BY DELTA MAY RESULT
IN THE RISK OF INJURY TO PERSONS.
CROSS-CUTTING
Cross-cutting requires the use of the miter gage to posi-
tion and guide the work. Place the work against the miter
gage and advance both the gage and work toward the
saw blade, as shown in Fig. 50. The miter gage may be
used in either table slot. When bevel cutting (blade tilted),
use the right miter gage slot so that the blade tilts away
from the miter gage and your hands.
Start the cut slowly and hold the work firmly against the
miter gage and the table. One of the rules in running a
saw is that you never hang onto or touch a free piece of
work. Hold the supported piece, not the free piece that is
cut off. The feed in cross-cutting continues until the work
is cut in two, and the miter gage and work are pulled back
to the starting point. Before pulling the work back, it is
good practice to give the work a little sideways shift to
move the work slightly away from the saw blade. Never
pick up any short length of free work from the table while
the saw is running. Never touch a cutoff piece unless it is
at least a foot long.
For added safety and convenience the miter gage can be
fitted with an auxiliary wood-facing (C), as shown in Fig.
51, that should be at least 1 inch higher than the
maximum depth of cut, and should extend out 12 inches
or more to one side or the other depending on which
miter gage slot is being used. This auxiliary wood-facing
(C) can be fastened to the front of the miter gage by using
two wood screws (A) through the holes provided in the
miter gage body and into the wood-facing.
When using the block (B) Fig. 52, as a cut-
off gage, it is very important that the rear end of the block
be positioned so the work piece is clear of the block
before it enters the blade.
NEVER USE THE FENCE AS A CUT-OFF
GAGE WHEN CROSS-CUTTING.
When cross-cutting a number of pieces to the same
length, a block of wood (B), can be clamped to the fence
and used as a cut-off gage as shown in Fig. 52. It is
important that this block of wood always be positioned in
front of the saw blade as shown. Once the cut-off length
is determined, secure the fence and use the miter gage to
feed the work into the cut.
This block of wood allows the cut-off piece to move freely
along the table surface without binding between the
fence and the saw blade, thereby lessening the possibility
of kickback and injury to the operator.
Fig. 50
Fig. 51
Fig. 52
C
A
B