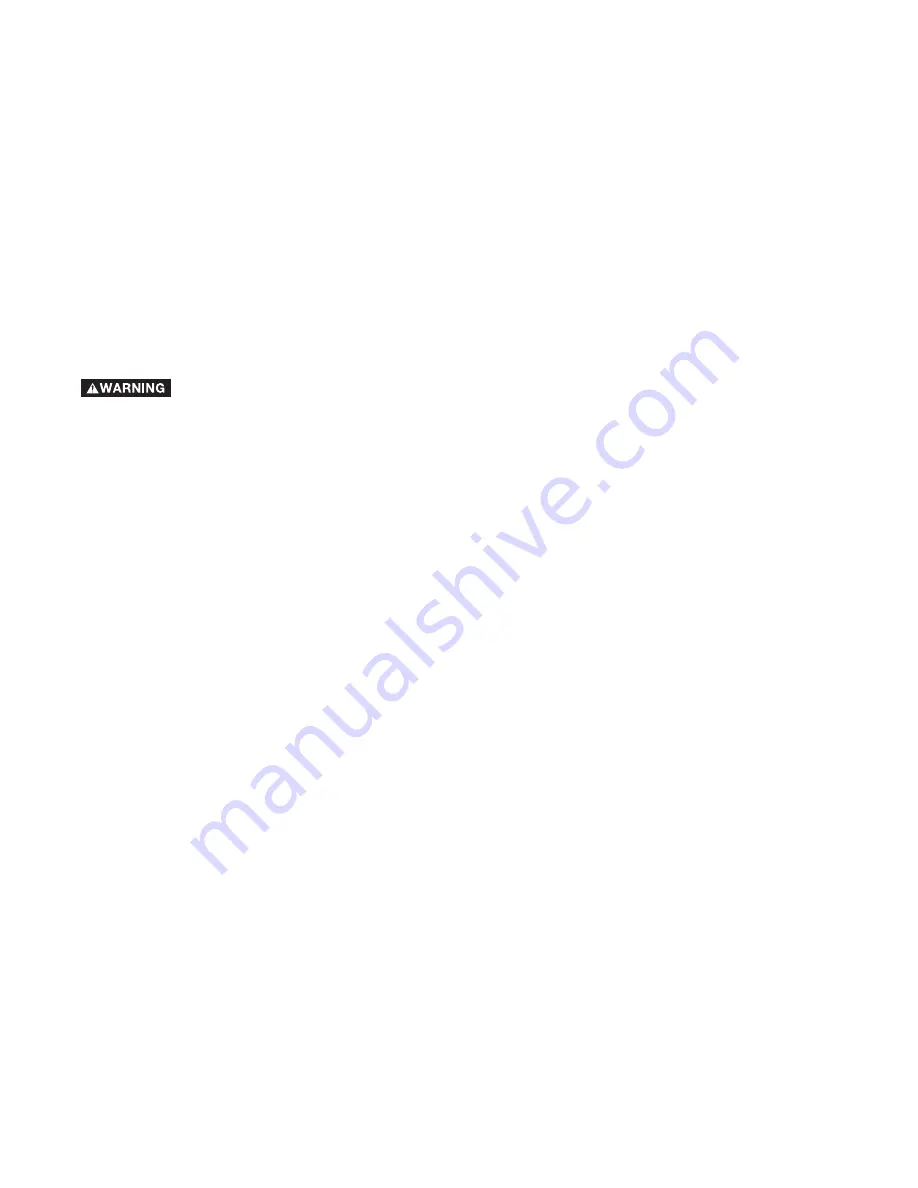
3
17.
REDUCE THE RISK OF UNINTENTIONAL STARTING
.
Make sure switch is in “OFF” position before plugging in
power cord. In the event of a power failure, move switch
to the “OFF” position.
18.
NEVER STAND ON TOOL
. Serious injury could occur
if the tool is tipped or if the cutting tool is accidentally
contacted.
19.
CHECK DAMAGED PARTS
. Before further use of the
tool, a guard or other part that is damaged should be
carefully checked to ensure that it will operate properly and
perform its intended function – check for alignment of
moving parts, binding of moving parts, breakage of parts,
mounting, and any other conditions that may affect its
operation. A guard or other part that is damaged should be
properly repaired or replaced.
20.
DIRECTION OF FEED
. Feed work into a blade or
cutter against the direction of rotation of the blade or cutter
only.
21.
NEVER LEAVE TOOL RUNNING UNATTENDED.
TURN POWER OFF
. Don’t leave tool until it comes to a
complete stop.
22.
STAY ALERT, WATCH WHAT YOU ARE DOING, AND
USE COMMON SENSE WHEN OPERATING A POWER
TOOL. DO NOT USE TOOL WHILE TIRED OR UNDER
THE INFLUENCE OF DRUGS, ALCOHOL, OR
MEDICATION.
A moment of inattention while operating
power tools may result in serious personal injury.
23.
MAKE SURE TOOL IS DISCONNECTED FROM
P O W E R S U P P LY
w h i l e m o t o r i s b e i n g m o u n t e d ,
connected or reconnected.
24.
THE DUST GENERATED
by certain woods and wood
products can be injurious to your health. Always operate
machinery in well ventilated areas and provide for proper
dust removal. Use wood dust collection systems whenever
possible.
ADDITIONAL SAFETY RULES FOR
TABLE SAWS
FAILURE TO FOLLOW THESE RULES MAY RESULT IN SERIOUS PERSONAL INJURY.
1.
DO NOT OPERATE THIS MACHINE
until it is
assembled
and
installed
according to the
instructions.
2.
OBTAIN ADVICE FROM YOUR SUPERVISOR,
instructor, or another qualified person
if you are
not familiar with the operation of this machine.
3.
FOLLOW ALL WIRING CODES
and recommended
electrical connections.
4.
USE THE GUARDS WHENEVER POSSIBLE.
Check to see that they are in place, secured, and
working correctly.
5.
AVOID KICKBACK by:
A. keeping blade sharp and free of rust and pitch.
B. keeping rip fence parallel to the saw blade.
C. using saw blade guard and spreader for every
possible operation, including all through
sawing.
D. pushing the workpiece past the saw blade prior
to release.
E. never ripping a workpiece that is twisted or
warped, or does not have a straight edge to
guide along the fence.
F.
using featherboards when the anti-kickback
device cannot be used.
G. never sawing a large workpiece that cannot be
controlled.
H. never using the fence as a guide when
crosscutting.
I.
never sawing a workpiece with loose knots or
other flaws.
6.
ALWAYS USE GUARDS, SPLITTER, AND ANTI-
KICKBACK FINGERS
except when otherwise
directed in the manual.
7.
REMOVE CUT-OFF PIECES AND SCRAPS
from
the table before starting the saw. The vibration of the
machine may cause them to move into the saw
blade and be thrown out. After cutting, turn the
machine off. When the blade has
come to a
complete stop, remove all debris.
8.
NEVER START THE MACHINE
with the workpiece
against the blade.
9.
HOLD THE WORKPIECE FIRMLY
against the miter
gauge or fence.
10.
NEVER
run the workpiece between the fence and a
moulding cutterhead.
11.
NEVER
perform “free-hand” operations. Use either
the fence or miter gauge to position and guide the
workpiece.
12.
USE PUSH STICK(S)
for ripping a narrow
workpiece.
13.
AVOID AWKWARD OPERATIONS AND HAND
POSITIONS
where a sudden slip could cause a
hand to move into the blade.
14.
KEEP ARMS, HANDS, AND FINGERS
away from
the blade.
15.
NEVER
have any part of your body in line with the
path of the saw blade.
16.
NEVER REACH AROUND
or over the saw blade.
17.
NEVER
attempt to free a stalled saw blade without
first turning the machine “OFF”.
18.
PROPERLY SUPPORT LONG OR WIDE
workpieces.
19.
NEVER PERFORM LAYOUT,
assembly or set-up
work on the table/work area when the machine is
running.
20.
TURN THE MACHINE “OFF” AND DISCONNECT
THE MACHINE
from the power source before
installing or removing accessories, before adjusting
or changing set-ups, or when making repairs.
21.
TURN THE MACHINE “OFF”,
disconnect the
machine from the power source, and clean the
table/work area before leaving the machine. LOCK
THE SWITCH IN THE “OFF” POSITION to prevent
unauthorized use.
22.
ADDITIONAL INFORMATION
regarding the safe
and proper operation of this tool is available from
the Power Tool Institute, 1300 Summer Avenue,
Cleveland, OH 44115-2851. Information is also
available from the National Safety Council, 1121
Spring Lake Drive, Itasca, IL 60143-3201. Please
refer to the American National Standards Institute
ANSI 01.1 Safety Requirements for Woodworking
Machines and the U.S. Department of Labor OSHA
1910.213 Regulations.
SAVE THESE INSTRUCTIONS.
Refer to them often and use them to instruct others.
Summary of Contents for 36-650
Page 31: ...NOTES 31...