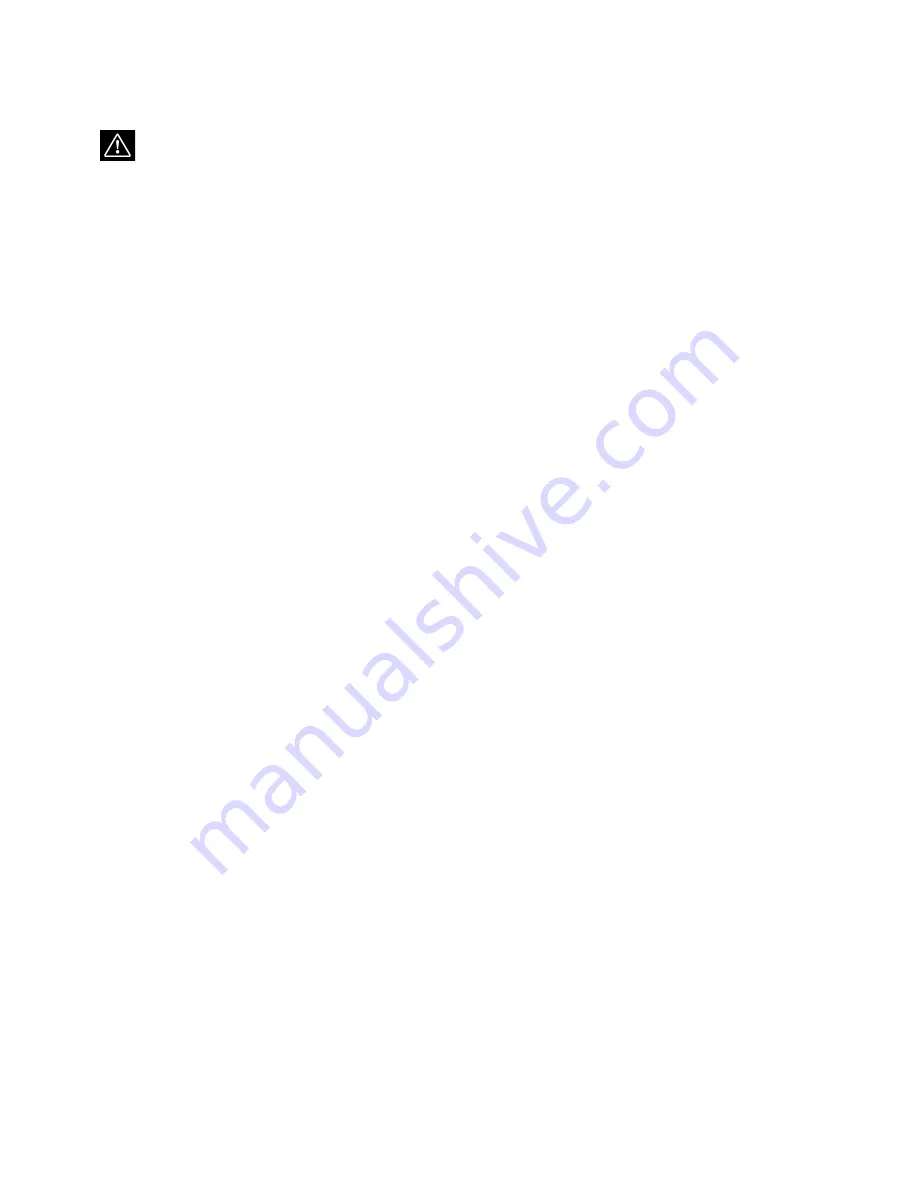
3
ADDITIONAL SAFETY RULES FOR
TABLE SAWS
WARNING: FAILURE TO FOLLOW THESE RULES MAY RESULT IN SERIOUS PERSONAL INJURY.
SAVE THESE INSTRUCTIONS.
Refer to them often
and use them to instruct others.
1
.
DO NOT OPERATE THIS MACHINE
until
it is
assembled
and
installed
according to the
instructions.
2.
OBTAIN ADVICE FROM YOUR SUPERVISOR,
instructor, or another qualified person
if you are not
familiar with the operation of this machine.
3.
FOLLOW ALL WIRING CODES
and recommended
electrical connections.
4.
USE THE GUARDS WHENEVER POSSIBLE.
Check
to see that they are in place, secured, and working
correctly.
5.
AVOID KICKBACK by:
A. keeping blade sharp and free of rust and pitch.
B. keeping rip fence parallel to the saw blade.
C. using saw blade guard and spreader for every
possible operation, including all through sawing.
D. pushing the workpiece past the saw blade prior to
release.
E.
never ripping a workpiece that is twisted or
warped, or does not have a straight edge to guide
along the fence.
F.
using featherboards when the anti-kickback device
cannot be used.
G. never sawing a large workpiece that cannot be
controlled.
H. never using the fence as a guide when
crosscutting.
I.
never sawing a workpiece with loose knots or other
flaws.
6.
ALWAYS USE GUARDS, SPLITTER, AND ANTI-
KICKBACK FINGERS
except when otherwise directed
in the manual.
7.
REMOVE CUT-OFF PIECES AND SCRAPS
from the
table before starting the saw. The vibration of the
machine may cause them to move into the saw blade
and be thrown out. After cutting, turn the machine off.
When the blade has
come to a complete stop,
remove all debris.
8.
NEVER START THE MACHINE
with the workpiece
against the blade.
9.
HOLD THE WORKPIECE FIRMLY
against the miter
gauge or fence.
10.
NEVER
run the workpiece between the fence and a
moulding cutterhead.
11.
NEVER
perform “free-hand” operations. Use either the
fence or miter gauge to position and guide the
workpiece.
12.
USE PUSH STICK(S)
for ripping a narrow workpiece.
13.
AVOID AWKWARD OPERATIONS
AND HAND
POSITIONS
where a sudden slip could cause a hand
to move into the blade.
14.
KEEP ARMS, HANDS, AND FINGERS
away from the
blade.
15.
NEVER
have any part of your body in line with the path
of the saw blade.
16.
NEVER REACH AROUND
or over the saw blade.
17.
NEVER
attempt to free a stalled saw blade without first
turning the machine “OFF”.
18.
PROPERLY SUPPORT LONG OR WIDE
workpieces.
19.
NEVER PERFORM LAYOUT,
assembly or set-up work
on the table/work area when the machine is running.
20.
TURN THE MACHINE “OFF” AND DISCONNECT
THE MACHINE
from the power source before
installing or removing accessories, before adjusting or
changing set-ups, or when making repairs.
21.
TURN THE MACHINE “OFF”,
disconnect the machine
from the power source, and clean the table/work area
before leaving the machine. LOCK THE SWITCH IN
THE “OFF” POSITION to prevent unauthorized use.
22.
ADDITIONAL INFORMATION
regarding the safe and
proper operation of this tool is available from the Power
Tool Institute, 1300 Summer Avenue, Cleveland, OH
44115-2851. Information is also available from the
National Safety Council, 1121 Spring Lake Drive,
Itasca, IL 60143-3201. Please refer to the American
National Standards Institute ANSI 01.1 Safety
Requirements for Woodworking Machines and the U.S.
Department of Labor OSHA 1910.213 Regulations.