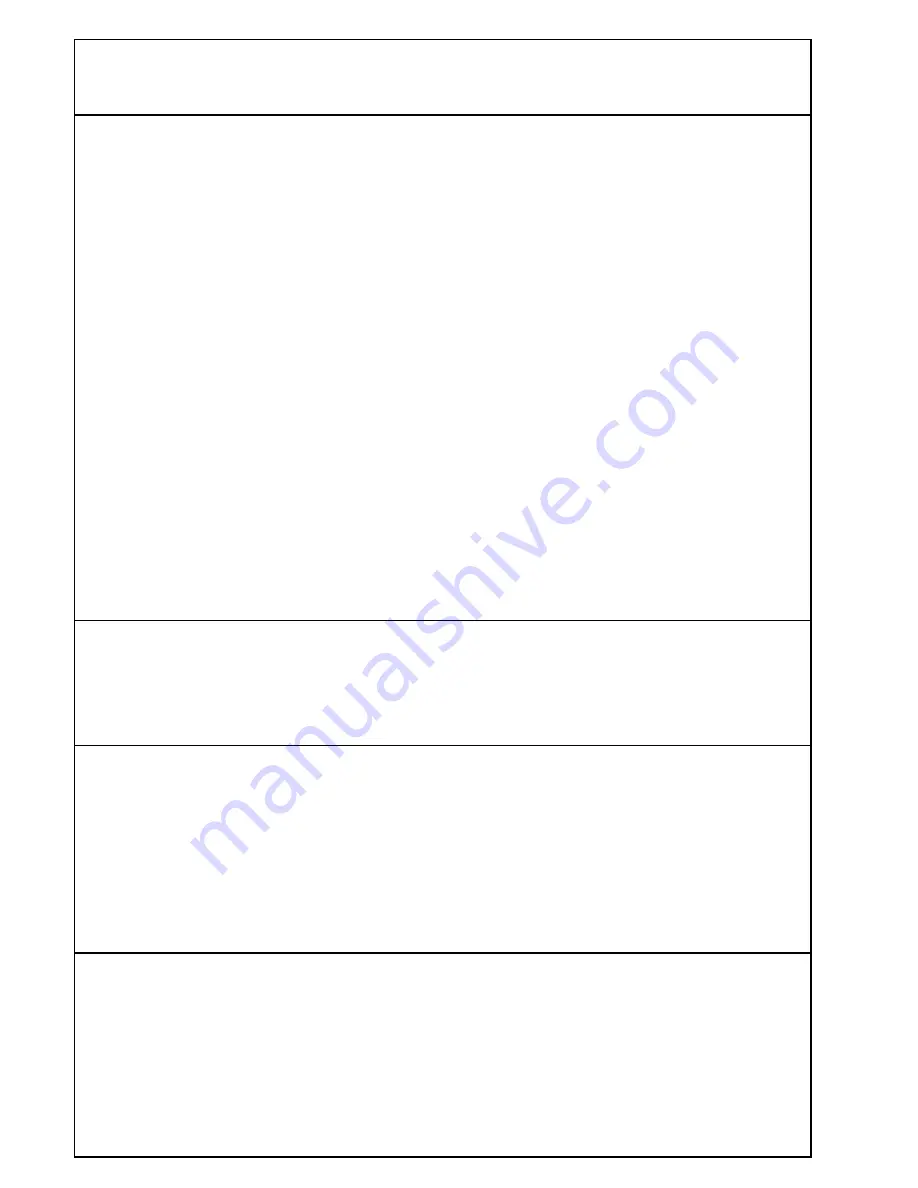
The following are trademarks of PORTER-CABLE
•
DELTA (Las siguientes son marcas registradas de PORTER-CABLE
•
DELTA S.A.) (Les marques
suivantes sont des marques de fabriquant de la PORTER-CABLE
•
DELTA): Auto-Set
®
, BAMMER
®
, B.O.S.S.
®
, Builder’s Saw
®
, Contractor’s Saw
®
,
Contractor’s Saw II™, Delta
®
, DELTACRAFT
®
, DELTAGRAM™, Delta Series 2000™, DURATRONIC™, Emc²™, FLEX
®
, Flying Chips™, FRAME SAW
®
,
Grip Vac™, Homecraft
®
, INNOVATION THAT WORKS
®
, Jet-Lock
®
, JETSTREAM
®
, ‘kickstand
®
, LASERLOC
®
, MICRO-SET
®
, Micro-Set
®
, MIDI LATHE
®
,
MORTEN™, NETWORK™, OMNIJIG
®
, POCKET CUTTER
®
, PORTA-BAND
®
, PORTA-PLANE
®
, PORTER-CABLE
®
&(design), PORTER-
CABLE
®
PROFESSIONAL POWER TOOLS, PORTER-CABLE REDEFINING PERFORMANCE™, Posi-Matic
®
, Q-3
®
&(design), QUICKSAND
®
&(design),
QUICKSET™, QUICKSET II
®
, QUICKSET PLUS™, RIPTIDE™&(design), SAFE GUARD II
®
, SAFE-LOC
®
, Sanding Center
®
, SANDTRAP
®
&(design), SAW
BOSS
®
, Sawbuck™, Sidekick
®
, SPEED-BLOC
®
, SPEEDMATIC
®
, SPEEDTRONIC
®
, STAIR EASE
®
, The American Woodshop
®
&(design), The Lumber
Company
®
&(design), THE PROFESSIONAL EDGE
®
, THE PROFESSIONAL SELECT
®
, THIN-LINE™, TIGER
®
, TIGER CUB
®
, TIGER SAW
®
,
TORQBUSTER
®
, TORQ-BUSTER
®
, TRU-MATCH™, TWIN-LITE
®
, UNIGUARD
®
, Unifence
®
, UNIFEEDER™, Unihead
®
, Uniplane™, Unirip
®
, Unisaw
®
,
Univise
®
, Versa-Feeder
®
, VERSA-PLANE
®
, WHISPER SERIES
®
, WOODWORKER’S CHOICE™.
Trademarks noted with ™ and ® are registered in the United States Patent and Trademark Office and may also be registered in other countries. Las
Marcas Registradas con el signo de ™ y ® son registradas por la Oficina de Registros y Patentes de los Estados Unidos y también pueden estar
registradas en otros países.
PORTER-CABLE
•
DELTA SERVICE CENTERS
(CENTROS DE SERVICIO DE PORTER-CABLE
•
DELTA)
Parts and Repair Service for Porter-Cable
•
Delta Machinery are Available at These Locations
(Obtenga Refaccion de Partes o Servicio para su Herramienta en los Siguientes Centros de Porter-Cable
•
Delta)
Authorized Service Stations are located in many large cities. Telephone
800-438-2486
or
731-541-6042
for assistance locating one.
Parts and accessories for Porter-Cable
·
Delta products should be obtained by contacting any Porter-Cable
·
Delta Distributor, Authorized
Service Center, or Porter-Cable
·
Delta Factory Service Center. If you do not have access to any of these, call
800-223-7278
and you will
be directed to the nearest Porter-Cable
·
Delta Factory Service Center. Las Estaciones de Servicio Autorizadas están ubicadas en muchas
grandes ciudades. Llame al
800-438-2486
ó al
731-541-6042
para obtener asistencia a fin de localizar una. Las piezas y los accesorios
para los productos Porter-Cable
·
Delta deben obtenerse poniéndose en contacto con cualquier distribuidor Porter-Cable
·
Delta, Centro
de Servicio Autorizado o Centro de Servicio de Fábrica Porter-Cable
·
Delta. Si no tiene acceso a ninguna de estas opciones, llame al
800-223-7278
y le dirigirán al Centro de Servicio de Fábrica Porter-Cable
·
Delta más cercano.
ARIZONA
Tempe 85282 (Phoenix)
2400 West Southern Avenue
Suite 105
Phone: (602) 437-1200
Fax: (602) 437-2200
CALIFORNIA
Ontario 91761 (Los Angeles)
3949A East Guasti Road
Phone: (909) 390-5555
Fax: (909) 390-5554
San Diego 92111
7638 Clairemnot Blvd.
Phone: (858) 277-9595
Fax: (858) 277-9696
San Leandro 94577 (Oakland)
3039 Teagarden Street
Phone: (510) 357-9762
Fax: (510) 357-7939
COLORADO
Arvada 80003 (Denver)
8175 Sheridan Blvd., Unit S
Phone: (303) 487-1809
Fax: (303) 487-1868
FLORIDA
Davie 33314 (Miami)
4343 South State Rd. 7 (441)
Unit #107
Phone: (954) 321-6635
Fax: (954) 321-6638
Tampa 33609
4538 W. Kennedy Boulevard
Phone: (813) 877-9585
Fax: (813) 289-7948
GEORGIA
Forest Park 30297 (Atlanta)
5442 Frontage Road,
Suite 112
Phone: (404) 608-0006
Fax: (404) 608-1123
ILLINOIS
Addison 60101 (Chicago)
400 South Rohlwing Rd.
Phone: (630) 424-8805
Fax: (630) 424-8895
Woodridge 60517 (Chicago)
2033 West 75th Street
Phone: (630) 910-9200
Fax: (630) 910-0360
MARYLAND
Elkridge 21075 (Baltimore)
7397-102 Washington Blvd.
Phone: (410) 799-9394
Fax: (410) 799-9398
MASSACHUSETTS
Franklin 02038 (Boston)
Franklin Industrial Park
101E Constitution Blvd.
Phone: (508) 520-8802
Fax: (508) 528-8089
MICHIGAN
Madison Heights 48071 (Detroit)
30475 Stephenson Highway
Phone: (248) 597-5000
Fax: (248) 597-5004
MINNESOTA
Minneapolis 55429
5522 Lakeland Avenue North
Phone: (763) 561-9080
Fax: (763) 561-0653
MISSOURI
North Kansas City 64116
1141 Swift Avenue
Phone: (816) 221-2070
Fax: (816) 221-2897
St. Louis 63119
7574 Watson Road
Phone: (314) 968-8950
Fax: (314) 968-2790
NEW YORK
Flushing 11365-1595 (N.Y.C.)
175-25 Horace Harding Expwy.
Phone: (718) 225-2040
Fax: (718) 423-9619
NORTH CAROLINA
Charlotte 28270
9129 Monroe Road, Suite 115
Phone: (704) 841-1176
Fax: (704) 708-4625
OHIO
Columbus 43214
4560 Indianola Avenue
Phone: (614) 263-0929
Fax: (614) 263-1238
Cleveland 44125
8001 Sweet Valley Drive
Unit #19
Phone: (216) 447-9030
Fax: (216) 447-3097
OREGON
Portland 97230
4916 NE 122 nd Ave.
Phone: (503) 252-0107
Fax: (503) 252-2123
PENNSYLVANIA
Willow Grove 19090
(Philadelphia)
520 North York Road
Phone: (215) 658-1430
Fax: (215) 658-1433
TEXAS
Carrollton 75006 (Dallas)
1300 Interstate 35 N, Suite 112
Phone: (972) 446-2996
Fax: (972) 446-8157
Houston 77043
4321 Sam Houston Parkway,
West
Suite 180
Phone: (713) 983-9910
Fax: (713) 983-6645
WASHINGTON
Auburn 98001(Seattle)
3320 West Valley HWY, North
Building D, Suite 111
Phone: (253) 333-8353
Fax: (253) 333-9613
Printed in U.S.A. PC-0104-149
CANADIAN PORTER-CABLE
•
DELTA SERVICE CENTERS
ALBERTA
Bay 6, 2520-23rd St. N.E.
Calgary, Alberta
T2E 8L2
Phone: (403) 735-6166
Fax: (403) 735-6144
BRITISH COLUMBIA
8520 Baxter Place
Burnaby, B.C.
V5A 4T8
Phone: (604) 420-0102
Fax: (604) 420-3522
MANITOBA
1699 Dublin Avenue
Winnipeg, Manitoba
R3H 0H2
Phone: (204) 633-9259
Fax: (204) 632-1976
ONTARIO
505 Southgate Drive
Guelph, Ontario
N1H 6M7
Phone: (519) 767-4132
Fax: (519) 767-4131
QUÉBEC
1515 ave.
St-Jean Baptiste, Suite 160
Québec, Québec
G2E 5E2
Phone: (418) 877-7112
Fax: (418) 877-7123
1447, Begin
St-Laurent, (Montréal),
Québec
H4R 1V8
Phone: (514) 336-8772
Fax: (514) 336-3505