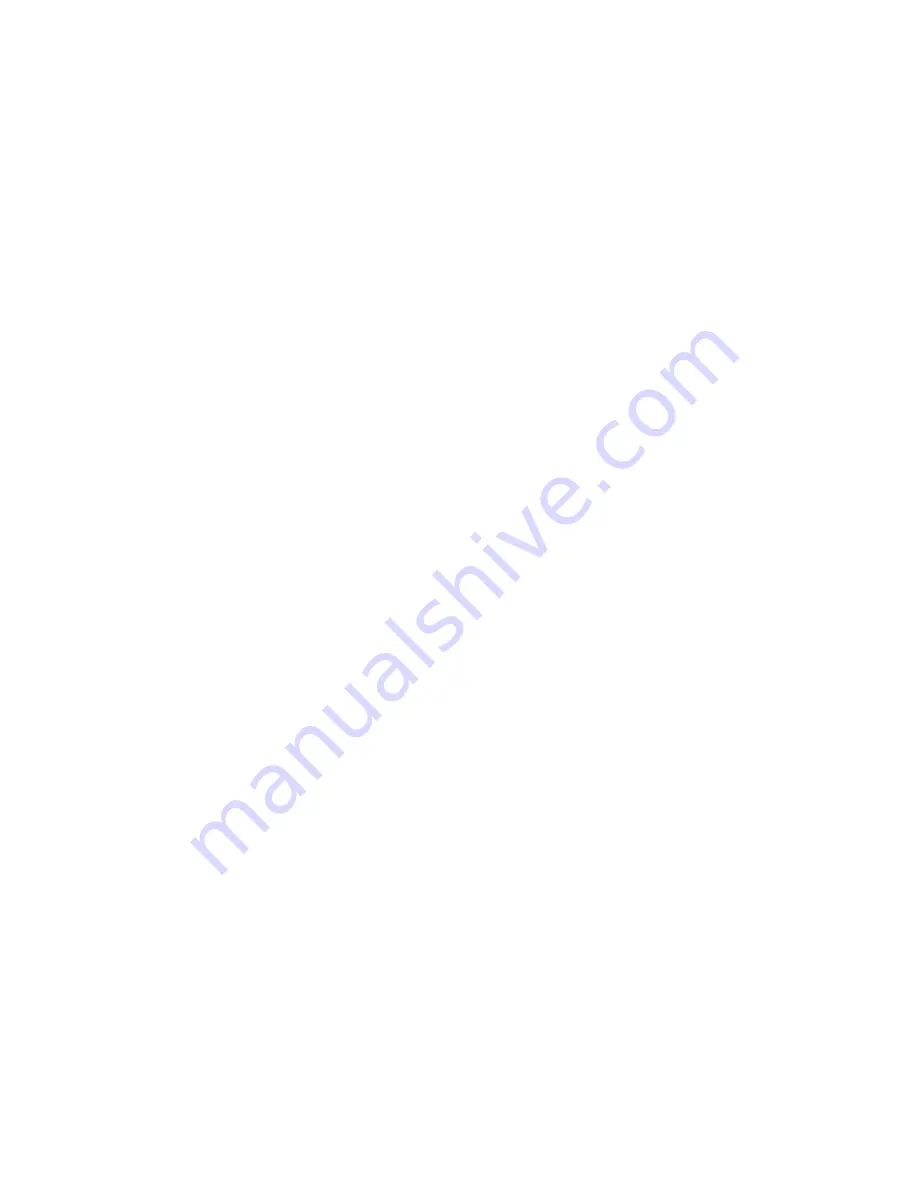
3
ADDITIONAL SAFETY RULES
FOR TABLE SAWS
1.
DO NOT OPERATE YOUR TOOL
until it is
completely assembled and installed according to the
instructions.
2.
IF YOU ARE NOT
thoroughly familiar with the opera-
tion of circular saws, obtain advice from your supervisor,
instructor, or other qualified person.
3.
ALWAYS
use guard, splitter and anti-kickback fingers
on all “thru-sawing” operations. Thru-sawing operations
are those when the blade cuts completely through the
workpiece as in ripping or cross-cutting.
4.
ALWAYS
hold the work firmly against the miter gage
or fence.
5.
NEVER
use the fence as a cut-off gage when cross-
cutting.
6.
MOVE
the rip fence out of the way when cross-
cutting.
7.
NEVER
perform any operation “free-hand” which
means using your hands to support or guide the
workpiece. Always use either the fence or miter gage to
position and guide the work.
8.
ALWAYS
use a push stick for ripping narrow stock.
Refer to ripping applications in instruction manual where
the push stick is covered in detail.
9.
AVOID
kickbacks (work thrown back toward you) by:
A. Keeping blade sharp.
B. Keeping rip fence parallel to the saw blade.
C. Keeping splitter and anti-kickback fingers and
guard in place and operating.
D. Not releasing the work before it is pushed all the
way past the saw blade.
E. Not ripping work that is twisted or warped or
does not have a straight edge to guide along
the fence.
10.
AVOID
awkward operations and hand positions
where a sudden slip could cause your hand to move into
the cutting tool.
11.
ALWAYS
keep hands and fingers away from the
cutting tool.
12.
NEVER
stand or have any part of your body in line
with the path of the saw blade.
13.
NEVER
reach behind or over the cutting tool with
either hand for any reason.
14.
DIRECTION OF FEED
. Feed work into cutting tool
against the direction or rotation of the cutting tool only.
15.
DO NOT
feed the material too fast while cutting.
Feed the material only fast enough so that the blade will
cut.
16.
NEVER
attempt to free a stalled saw blade without
first turning the saw “OFF.”
17.
NEVER
start the saw with the workpiece pressed
against the blade.
18.
NEVER
turn the saw “ON” before clearing the table
of all objects (tools, scraps of wood, etc.).
19.
ALWAYS STOP
the saw before removing scrap
pieces from the table.
20.
NEVER
perform layout, assembly or set-up work on
the table while the saw is operating.
21.
PROVIDE
adequate support to the rear and sides of
the saw table for wide or long workpieces.
22.
WHEN
cutting mouldings,
NEVER
run the stock
between the fence and the moulding cutterhead.
23.
NEVER
use solvents to clean plastic parts. Solvents
could possibly dissolve or otherwise damage the material.
Only a soft damp cloth should be used to clean plastic
parts.
24.
SHOULD
any part of your tool be missing, damaged,
or fail in any way, or any electrical components fail to
perform properly, shut off tool and remove plug from
power supply outlet. Replace missing, damaged or failed
parts before resuming operation.
25.
IMPORTANT: When the tool is not in use, the
switch should be locked in the “OFF” position to
prevent unauthorized use.
26.
ADDITIONAL INFORMATION
regarding the safe
and proper operation of this product is available from the
National Safety Council, 1121 Spring Lake Drive, Itasca,
IL 60143-3201, in the Accident Prevention Manual for
Industrial Operations and also in the Safety Data Sheets
provided by the NSC. Please also refer to the American
National Standards Institute ANSI 01.1 Safety
Requirements for Woodworking Machinery and the U.S.
Department of Labor OSHA 1910.213 Regulations.
Summary of Contents for 36-325C
Page 28: ...28 NOTES...