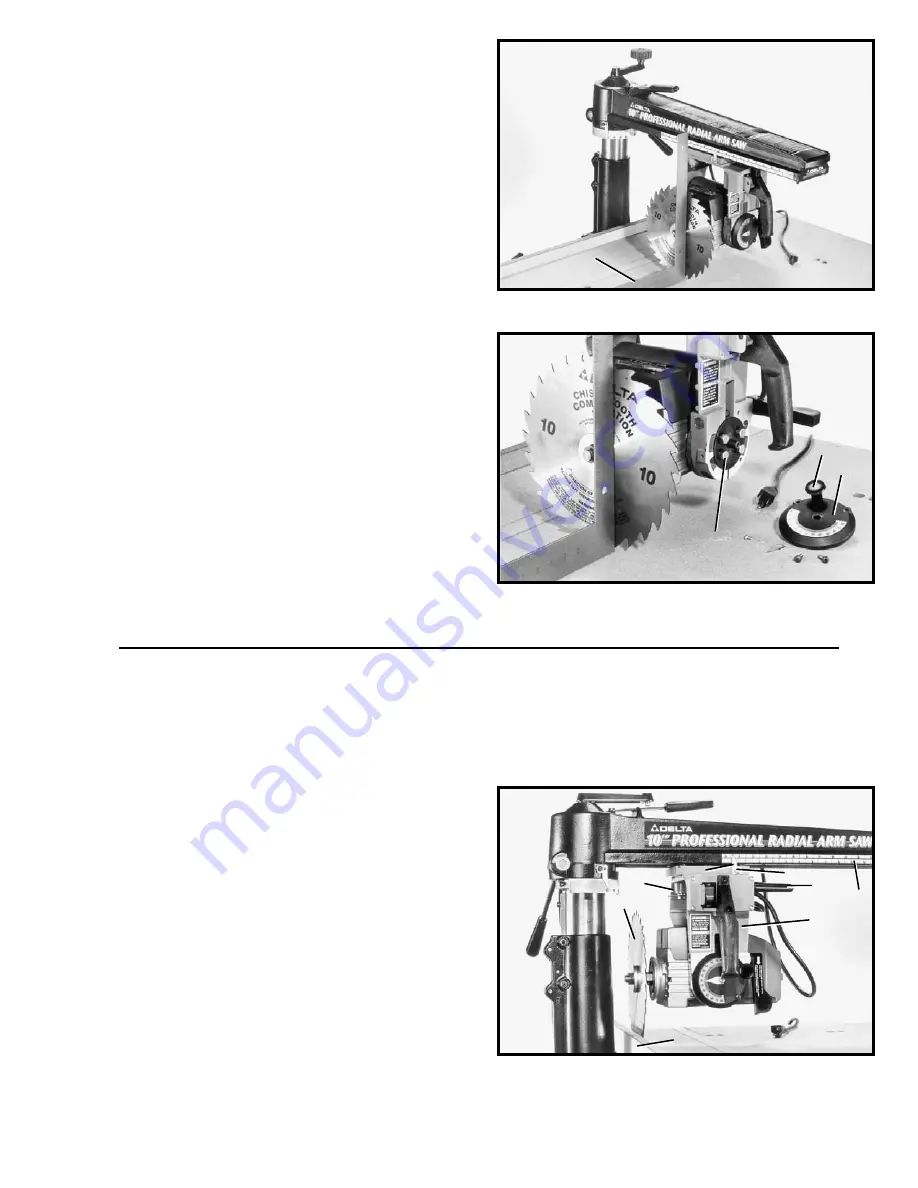
17
Fig. 41
Fig. 42
Fig. 43
5.
Place a square (D) Fig. 41, on the table and against
the saw blade, as shown, and check to see if the blade
is square with the table.
NOTE: The square should rest
between two teeth of the saw blade
.
6.
If an adjustment is necessary, make certain bevel
clamp lever (C) Fig. 40, is tight. Remove screw, flat
washer, and pointer (E) Fig. 40. Remove two screws (F)
Fig. 40, and bevel scale plate (H) Fig. 42, with index
knob (A).
7.
Loosen four hex head screws (G) Fig. 42. Tilt the
motor until the saw blade is flush with the square.
Tighten four hex head screws (G).
8.
Replace bevel scale plate (H) Fig. 42, with bevel
index release knob (A), two screws, and pointer that
were removed in
STEP 6
.
NOTE: Adjust pointer to
“zero” on the bevel index scale.
1.
DISCONNECT TOOL FROM POWER SOURCE
.
2. Loosen yoke clamp handle (A) Fig. 43. Release yoke
index by pressing yoke indexing release lever (B) up or
down, and rotating cutting-head (C) to the in-rip
position as shown. Tighten yoke clamp lever (A).
3.
Position fence (D) Fig. 43, at the rear of table as
shown.
4.
Loosen cutting-head clamp knob (G) Fig. 48 and
slide cutting-head (C) Fig. 43, to rear of track arm until
saw blade (F) is flush against fence (D).
5.
Tighten cutting-head clamp knob (G) Fig. 48 and
adjust pointer (H) Fig. 43, if necessary, to “zero” mark on
lower scale (J) by loosening screw (K). After adjustment
is made, tighten screw (K).
D
G
A
H
A
J
K
C
D
F
B
H
ADJUSTING IN/OUT RIP SCALE
Summary of Contents for 33-830
Page 28: ...28 NOTES...