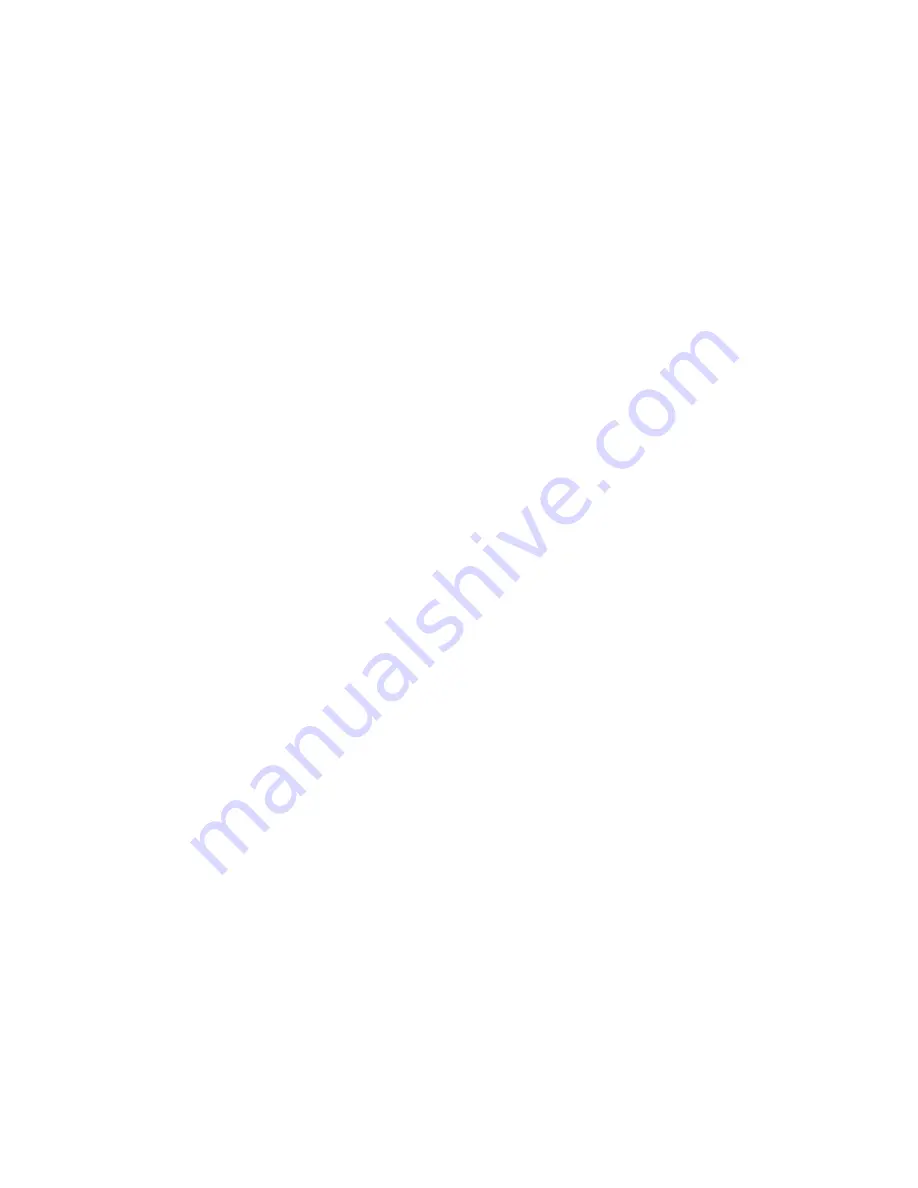
4
ADDITIONAL SAFETY RULES FOR
ABRASIVE CUT-OFF SAWS
1.
WARNING:
Do not operate your abrasive cut-off
saw until it is completely assembled and installed
according to the instructions.
2.
IF YOU ARE NOT
thoroughly familiar with the oper-
ation of abrasive cut-off saws, obtain advice from your
supervisor, instructor or other qualified person.
3.
WEAR
safety goggles, face shield, respirator, body
apron, headcovering, safety shoes, long tight-fitting
sleeves and gloves.
4.
USE ONLY
recommended reinforced abrasive wheels
with blotters.
5.
TIGHTEN
arbor screw and all clamps before operat-
ing.
6.
MAKE SURE
spindle lock is disengaged before
operating.
7.
ALWAYS
keep guards in place and working properly.
8.
KEEP
hands clear of cut-off wheel.
9.
SECURE
workpiece properly. Work should be
straight and firmly clamped to avoid possible movement
and pinching as the cut nears completion.
10.
NEVER
cut anything freehand.
11.
NEVER
reach behind or beneath the cut-off wheel.
12.
MAKE SURE
the wheel has come to a complete
stop before removing or securing workpiece or changing
workpiece angle.
13.
MAKE SURE
the inside surfaces of the wheel
flanges as well as the sides of the wheel are free from
any foreign matter.
14.
WHEN MOUNTING
the wheel, care should be taken
to tighten the arbor screw only enough to hold the wheel
firmly and to prevent wheel slippage. Excessive tighten-
ing may result in damaging the wheel and springing the
wheel flanges.
15.
USE ONLY
abrasive wheels rated at 3900 RPM or
higher.
16.
ALWAYS
check the wheel for cracks or other dam-
age before operation. Replace cracked or damaged
wheel immediately.
17.
USE ONLY
wheel flanges specified for your machine.
18.
MAKE SURE
abrasive wheel is not contacting
workpiece before switch is turned on.
19.
ALLOW
the motor to come up to full speed before
starting cut.
20.
AFTER TURNING MACHINE ON
, lower wheel lightly
until it comes into contact with the workpiece and then
draw wheel firmly through the cut.
DO NOT
allow the
wheel to chatter and jump as this may cause the wheel
to wear out of round, resulting in poor cutting and pos-
sible broken wheels.
21.
ANY
material can be cut more satisfactorily when
placed in position for the wheel to cut with the least arc
of contact.
22.
THE NUMBER
of cuts per wheel, as well as the
quality of cut, may vary considerably with the cutting
time. Fast cuts cause the wheel to wear more rapidly
but also help to reduce discoloration and burr. This is
especially noticeable when cutting light gage tubing.
When coming through the bottom wall, with the longer
arc of contact, do not slow-up but give a vigorous pull.
This keeps the metal from overheating and dragging off
in a heavy burr.
23.
USE
the wheel guard at all times.
24.
NEVER
operate the machine in an area with flam-
mable liquids or gases.
25.
TO AVOID
electric shock, do not use under damp
conditions or expose to rain.
26.
THIS
tool is designed for ferrous metals only.
DO
NOT
attempt to cut wood, masonry, aluminum or magne-
sium with this tool.
27.
AFTER
installing a new wheel, never start the tool
with a person in line with the wheel.
ALWAYS
run the
tool for approximately one minute before cutting. If the
wheel has an undetected crack or flaw, it could burst in
less than one minute.
28.
SHUT OFF
power before servicing or adjusting tool.
29.
SHOULD
any part of your machine be missing,
damaged or fail in any way, or any electrical component
fail to perform properly, shut-off switch and remove plug
from power supply outlet. Replace missing, damaged or
failed parts before resuming operation.
30.
ADDITIONAL INFORMATION
regarding the safe
and proper operation of this product is available from
the National Safety Council, 1121 Spring Lake Drive,
Itasca, IL 60143-3201 in the Accident Prevention Manual
for Industrial Operation and also in the Safety Data
Sheets provided by the NSC. Please also refer to the
American National Standard Institute ANSI 01.1 Safety
Require-ments for Woodworking Machinery and the
U.S. Depart-ment of Labor OSHA 1910.213
Regulations.